-
-
News
News Highlights
- Books
Featured Books
- smt007 Magazine
Latest Issues
Current IssueWhat's Your Sweet Spot?
Are you in a niche that’s growing or shrinking? Is it time to reassess and refocus? We spotlight companies thriving by redefining or reinforcing their niche. What are their insights?
Moving Forward With Confidence
In this issue, we focus on sales and quoting, workforce training, new IPC leadership in the U.S. and Canada, the effects of tariffs, CFX standards, and much more—all designed to provide perspective as you move through the cloud bank of today's shifting economic market.
Intelligent Test and Inspection
Are you ready to explore the cutting-edge advancements shaping the electronics manufacturing industry? The May 2025 issue of SMT007 Magazine is packed with insights, innovations, and expert perspectives that you won’t want to miss.
- Articles
- Columns
- Links
- Media kit
||| MENU - smt007 Magazine
Mentor’s Michael Ford on Lean for Surface Mount Processes
November 25, 2015 | Andy Shaughnessy, I-Connect007Estimated reading time: 6 minutes
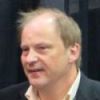
I had the opportunity to sit down with Michael Ford at the recent SMTA show in Chicago. As the senior marketing development manager with Mentor Graphics, Valor Division, Michael had a busy few days, which included the presentation of a paper on lean systems in surface mount processes.
Andy Shaughnessy: Michael, why don't you tell me a bit about the paper you presented.
Michael Ford: We presented a paper on lean manufacturing and the lean flow on the factory floor, with a focus on surface mount. Customers came along and said they want some flexibility with the way that factories deliver, and in response we have lean manufacturing cells set up, so that the final stages in production could then deliver according to the customer need.
This didn't flow back to surface mount, because there is one very, very significant problem with it: The more changes you have, the more inefficient the process becomes. Every time you change something, you've got to change over products, which means changing materials. Materials change-over takes time. We see that there is a 50% reduction in overall productivity.
Some of the software guys here will say they can do common set-up plans, so you don't need to change materials. In reality, what happens is the machine program efficiency reduces. Then the machine vendors come along and say "You can use our removable trolley tables for machines." That works fine, except it increases your materials cost, because you've got more excess materials on the floor. There's never been a good solution to apply lean into surface mount.
Shaughnessy: So, what's the answer?
Ford: We decided to take a completely different point of view, because traditional people will apply lean to processes and make those processes more efficient by reducing the waste in the process.
Think about it this way: When we came to the show, we all went through an airport to get here. We got to the check-in queue, waited behind people for five or 10 minutes. Some people checked in online, but they still have to wait to drop off their bags. They eventually got to the desk, and they eventually got their tickets and everything. Then it was straight into the queue for security. You showed the passport, got everything sorted, showed ID, etc. Then it was into the security scans for bag scanning.
You got out of there and realized that you still had an hour before your plane leaves. You had a couple of beers, maybe a sandwich, and you got on the plane. Bad news: air traffic control problems and another 10, 20, or 30 minutes to wait. It will take you two to three hours from arriving at the airport to taking off.
Now think about how much time was actually necessary at the airport. How long did you interact with the guy at the desk? How long did it take to scan your bag? You add the whole thing up and within five minutes you could have been done and out of there. Of the two-hour experience, five minutes was the added value.
For surface mount it is exactly the same. Products come into electronics manufacturing, and they go through one process as part of maybe a hundred or a thousand others. Then they are waiting for the next process while other things happen, and if you analyze it, you will see it’s exactly the same. Between one and five percent of the time in the factory is added value. The rest is waste.
Part of this kind of lean approach for Industry 4.0, in order to make things very flexible, is to get the products through really quickly. That's what we need to do. We need to stop focusing on the endless optimization processes, which are still important, but let’s think about the optimization from the point of view of the product. The product’s experience, if it had one, going through the factory. This is what we can make lean.
Shaughnessy: What's Mentor's take on this and what's your approach?
Ford: First of all, we're throwing away the rule book. The rule book for lean says that you follow the pulse signal and you supply goods as they are needed. Sorry guys, that doesn't work for us. In surface mount, what we do instead is provide a finite planning team. Now, the key word there is finite, because it means that we understand all of the relevant situations of manufacturing.
That's going to include understanding from the machines, by direct communication, where we are according to the current schedule. It means getting information about the requirements for delivery. What are the changed requirements? What are the exact materials that we've got available and are allocated? What are the choices for the production lines that we can use for all of the particular models or products? Once we've got all of that information, you just press the button and the whole thing just optimizes and understands all those considerations.
Shaughnessy: Once they have all the information, I guess the main challenge at that point is making sure you have all the information to plug in, then?
Ford: Yeah, that's the biggest thing. In the industry, trying to get all that information usually resides in many different systems. Being able to connect with one integrated system would be great, but in practical terms, people need to attach things to their MES, their EOP, maybe the machine’s bender solutions need to come into play, so its consolidating all the time.
Shaughnessy: That’s interesting, because we talked to our PCB Design Magazine readers, and some designers are using a value-stream mapping right now; they are trying to get and extra hour out of the design software. It’s funny, because it's catching on, where you wouldn't expect it. I didn't expect it.
Ford: Transactional lean. It’s interesting.
For the designers, if I was a designer, I would be real frustrated with the kind of tools that they generally use. You need to be able to understand that design is perfect for production. These guys don't even know production. They don't know what an SMT machine is or an in-circuit task. To be honest, it’s hardly worth training them to do that. It takes years of experience.
One of the actual tools we have in that area is the ability to do design for manufacturing that is task-based on the actual conditions in manufacturing itself. The designer can sit there. What's he going to do? Is he going to finalize his design and then in a couple of weeks or months face endless requests for changes and improvements? Or is he going to simply run the design for manufacturing software based on the manufacturing rules. A few mouse clicks and all is set, and he can relax and move onto the next one and he saves all of that time for all of those interruptions that come later. I guess that's what they're looking for—to save the time.
Shaughnessy: They're all looking to see if they can save minutes.
Ford: The kind of direction we're moving towards is to look at Industry 4.0 a little more. In the U.S., I think the term Industry 4.0 is not so strong, but the feeling behind it is very strong.
Shaughnessy: A lot of people are talking about it. But I see a lot of talk and nothing going on yet.
Ford: The real understanding of how to do something on a site basis is very important. All the little functions we see the machine vendors doing are great. It promotes the gathering of information. They're providing real value back for their customers. It needs to be taken one step further. It needs to be the whole factory operation to keep everything running efficiently in terms of material, in terms of finite plant, and in terms of delivery for the customer, which can change every day. What we said about the production planning and the finite planning, that's one essential part of our whole story. It includes the offerings we see from machine vendors, from MES systems, from all these different kinds of operators playing together. The ultimate goal is factory best.
Shaughnessy: That sounds good. We'll leave it there. Thank you very much.
Ford: Thank you, Andy.
Suggested Items
Best Papers from SMTA International Announced
04/10/2025 | SMTAThe SMTA is pleased to announce the Best Papers from SMTA International 2024. The winners were selected by members of the conference technical committee. Awards are given for "Best of Proceedings" as well as "Best Practical and Applications-Based Knowledge" categories. A plaque is given to primary authors of all winning papers for these exceptional achievements.
Technica USA Showcases PCBA Supply Partners at IPC APEX EXPO 2025
03/13/2025 | Technica USATechnica USA is thrilled to highlight its full portfolio of PCBA supply partners at the 2025 APEX/IPC Expo in Anaheim, California. Featuring some of the world’s leading suppliers, Technica’s PCBA product lineup continues to drive innovation and excellence in the industry.
Designer’s Notebook: DFM Principles for Flexible Circuits
09/14/2023 | Vern Solberg -- Column: Designer's NotebookFlexible circuit applications can be as basic as furnishing electrical interconnect between two conventional circuit board assemblies, or to prove a platform for placing and interconnecting electronic components. During the planning and pre-design phase of the flexible circuit, there will be several material and process related questions that need to be addressed. Most flexible circuit fabricators welcome the opportunity to discuss their customers’ flexible circuit objectives prior to beginning the actual design process.
ZESTRON to Showcase Innovative Cleaning Solutions and Process Support at SMTA International 2023
09/11/2023 | ZESTRONZESTRON, the leading global provider of high-precision cleaning products, services, and training solutions in the electronics manufacturing and semiconductor industries, is thrilled to announce its participation in the upcoming Surface Mount Technology Association (SMTA) International Conference and Exhibition, scheduled to take place from October 9-12, 2023.
Austin American Technology Creates Buzz with Justin Worden’s 1st SMTA Presentation
09/07/2023 | Austin American Technology (AAT)Justin Worden, the dynamic Global Sales and Marketing Director at Austin American Technology (AAT), is no stranger to creating a buzz in the electronics industry.