-
- News
- Books
Featured Books
- design007 Magazine
Latest Issues
Current IssueCreating the Ideal Data Package
Why is it so difficult to create the ideal data package? Many of these simple errors can be alleviated by paying attention to detail—and knowing what issues to look out for. So, this month, our experts weigh in on the best practices for creating the ideal design data package for your design.
Designing Through the Noise
Our experts discuss the constantly evolving world of RF design, including the many tradeoffs, material considerations, and design tips and techniques that designers and design engineers need to know to succeed in this high-frequency realm.
Learning to Speak ‘Fab’
Our expert contributors clear up many of the miscommunication problems between PCB designers and their fab and assembly stakeholders. As you will see, a little extra planning early in the design cycle can go a long way toward maintaining open lines of communication with the fab and assembly folks.
- Articles
- Columns
Search Console
- Links
- Media kit
||| MENU - design007 Magazine
Good In, Good Out: Bay Area Circuits Discusses Data Strategies
December 2, 2015 | Barry Matties, I-Connect007Estimated reading time: 2 minutes
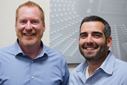
A lot of companies talk about the importance of good data management, but for some firms, this amounts to little more than lip service. Then there are companies like fabricator Bay Area Circuits. I recently sat down with Bay Area Circuits President Stephen Garcia and COO Brian Paper to discuss how automating and upgrading their data systems has significantly cut down overall process time, as well as their drive to educate young PCB designers and actively promote the industry to the emerging electronics industry workforce.
Barry Matties: Let’s talk about how you manage your data. Are you a completely electronic company?
Stephen Garcia: We have tried to go as paperless as possible, and we're talking actual production data starting from the Gerber. We use Ucamco's Integr8tor software, which is the entire company's backbone. That is our database. Everything is automated. And then we've tied in our own software to connect supplement Integr8tor.
Matties: When you say your own software, is that something you developed?
Garcia: Yes, it's basically a customized CRM platform. Some production data, like process cards, are still printed, but eventually everything is digitized and stored on our servers for easy access which is especially important given that a good portion of our engineering staff works remotely and needs real-time access to data.
As we continue to grow and identify bottlenecks, we make sure employees have the access they need. Not long ago, QC may have been inspecting a job but may not have all the details. Maybe they just had a fab print and the process card, so would have to walk over to Planning and say “I'm seeing something out of the ordinary; was this approved by the customer?” Today they have full access. Each job gets a tool number, and then everything is saved on our server for employees to access the data required.
That's the hardest part of our job: incomplete or conflicting customer data. Every customer is different when it comes to Gerbers and their fab prints. We have a handful of customers who often provide us with Gerbers that rarely match the fab print. It might be a non-plated hole on their fab print, but then their Gerber is plated, things of that nature. Our system allows employees to have access to the data to investigate any issues and prevent production hiccups.
Brian Paper: We've put more emphasis on the netlist too, as far as ensuring that the customers are providing us with that type of information. We just posted a whole blog post on what a netlist is, and why it's important.
Garcia: With every customer being different, our biggest challenge is trying to educate them about what we need to successfully manufacture their project and why we need it. It’s amazing that even when some of our larger customers put on a generic fab print, half of it doesn't apply to the actual board, and we need to get approval. We say, “Hey, can we deviate away from your fab print?” and they say, “Yeah, that shouldn't be there. Just ignore it.” It definitely slows things down. We've really tried to automate as much as possible from the minute we get Gerbers.
To read this entire article, which appeared in the November 2015 issue of The PCB Design Magazine, click here.
Suggested Items
In Pursuit of Perfection: Defect Reduction—May 2025 PCB007 Magazine Now Available
05/15/2025 | I-Connect007 Editorial TeamFor bare PCB board fabrication, defect reduction is a critical aspect of a company's bottom line profitability. In the May 2025 issue of PCB007 Magazine, we examine the imaging, etching, and plating processes, as well as product traceability on the shop floor, providing information and insight into how you can reduce your defects and increase yields.
Pluritec: Growth Depends on Developing Next-gen Products
05/15/2025 | Marcy LaRont, PCB007 MagazineMaurizio Bonati, VP of sales at Pluritec, says a new generation of products has driven strong business performance and a significant backlog. However, there’s a concern about the potential negative impact of tariffs. Pluritec is taking proactive measures to minimize these effects by focusing on enhancing equipment capabilities, automating processes, and expanding customer support.
Corning Collaborates with Broadcom to Accelerate AI Data Center Processing Capacity
05/14/2025 | BUSINESS WIRECorning Incorporated, a world leader in glass science and optical physics, today announced a collaboration with Broadcom Incorporated, a leading supplier in the semiconductor field, on a co-packaged optics (CPO) infrastructure that will significantly increase processing capacity within data centers.
Breaking Down Barriers: The Connectivity of Machines in SMT Production Lines
05/14/2025 | Bill Cardoso, Creative ElectronAs the world increasingly moves toward erecting trade barriers, we find ourselves in a paradox. Across the globe, the rise in tariffs and protectionist policies is creating a more fragmented global economy, with nations seeking to insulate themselves from external economic pressures. However, within the confines of the SMT production line, the trend is moving in precisely the opposite direction—toward greater connectivity, integration, and collaboration. Rather than isolating one machine from another, SMT production lines are increasingly interconnected, with data being shared across various stages of the process to improve quality, efficiency, and defect detection.
indie Semiconductor Reports Q1 2025 Results
05/13/2025 | BUSINESS WIREindie Semiconductor, Inc., an automotive solutions innovator, today announced first quarter results for the period ended March 31, 2025. Q1 revenue was up 3.3 percent year-over-year to $54.1 million with Non-GAAP gross margin of 49.5 percent. On a GAAP basis, first quarter 2025 operating loss was $38.9 million compared to $49.6 million a year ago.