-
-
News
News Highlights
- Books
Featured Books
- smt007 Magazine
Latest Issues
Current IssueIntelligent Test and Inspection
Are you ready to explore the cutting-edge advancements shaping the electronics manufacturing industry? The May 2025 issue of SMT007 Magazine is packed with insights, innovations, and expert perspectives that you won’t want to miss.
Do You Have X-ray Vision?
Has X-ray’s time finally come in electronics manufacturing? Join us in this issue of SMT007 Magazine, where we answer this question and others to bring more efficiency to your bottom line.
IPC APEX EXPO 2025: A Preview
It’s that time again. If you’re going to Anaheim for IPC APEX EXPO 2025, we’ll see you there. In the meantime, consider this issue of SMT007 Magazine to be your golden ticket to planning the show.
- Articles
- Columns
Search Console
- Links
- Media kit
||| MENU - smt007 Magazine
The Jefferson Project: Educating the Next Generation in Applied Manufacturing Sciences (Pt. 1)
January 20, 2016 | Patty Goldman, I-Connect007Estimated reading time: 3 minutes
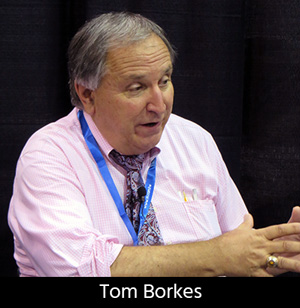
The Founder of The Jefferson Project and the forthcoming Jefferson Institute of Technology, Tom Borkes, sat down with me at SMTAI and provided his well-researched plan to bring manufacturing to engineering undergraduate students by bringing students to manufacturing, through a hands-on, real world learning experience.
Patty Goldman: Tom, I understand you founded the Jefferson project, why don’t you start by telling me what that’s all about.
Tom Borkes: It’s a very ambitious project. I wrote a paper years ago and coined the term ‘concurrent education’ because it became clear to me that there was this gap between academic preparation and industry need, that kept widening as the assembly technology got increasingly more complex. Obviously, schools are not able to respond to the needs of our industry in a timely fashion. I thought the only way to change that was to merge the two worlds – wrap a school around a for-profit contract manufacturing business. That’s what we’re in the process of putting together now. Students will be studying and working for four years towards a bachelor’s degree in applied design and manufacturing sciences and will have the opportunity to be educated in the real world for all four years. They will take all of the traditional courses needed for accreditation, but they will take them in the context of a for-profit, high tech, electronic product design and assembly business.
Goldman: Is the Jefferson Project a non-profit entity?
Borkes: The Jefferson Institute of Technology, the school part, will be a 501(c)(3) not-for-profit, but it’s important from the students’ preparation point of view that they receive their education in a real world, for-profit environment. One of the big problems, as anyone who’s gone to school and then gone out to the real world knows, is the long learning curve that one has to go up to become fully productive. We’re merging two environments that have been traditionally kept worlds apart.
Goldman: Are your goals, besides education, to get more and more people involved in this
Borkes: Yes. It turns out what we’ve done for the last five or six years really drills down into this issue about how to compete if you’re in a high labor rate market. In other words, if you’re in the United States you can pick up any newspaper and see the amount of manufacturing jobs that have been lost to low-labor-rate markets. It bothered me to hear and see that happen. What I tried to do was study in detail what the actual facts were surrounding this exodus of manufacturing jobs. It turns out you find that there is another way to reduce labor costs, other than just finding sources of low labor rate workers - and that is by reducing labor content. You do that through automation. Now, it sounds easy and obvious and I can give you examples. It is easy to pontificate about, but implementing is another story. In fact, the paper that I’m here to present this week addresses some important aspects of automation, because you find that it’s not enough to simply buy hundreds of thousands of dollars of equipment like we see here on the show floor. If you don’t have a workforce that can be successful in developing statistically capable processes and successful in maintaining those processes during a production run, you will fail. You will end up with a lot of products that have to be reworked. That rework consists of applying your high labor rate to troubleshooting, reworking, repairing, and then retesting a significant percentage of each product.
Goldman: You’ve also screwed up your cycle time and everything else.
Borkes: Absolutely. It occurred to me that we used to be very happy with 91% first pass incircuit testing, but that when you think about it another way of saying this is nine out of every 100 things we build have defects. You can’t do that and survive. Back in the ‘70s, and I talk about this in the paper, you could get away with that because there weren’t those low labor rate sources where you could throw labor at the product.
Goldman: People were more careless about improving because they didn’t have to.
Borkes: It started in the automobile business when Dr. Deming was shunned by Detroit and he ended up creating a manufacturing juggernaut in Japan.
Editor's Note: This article originally appeared in the January 2016 issue of SMT Magazine.
Suggested Items
APE, Automated Production Equipment, Marks 56-year Milestone
05/12/2025 | APEAutomated Production Equipment, or A.P.E. as the company has been known for more than a half century, is marking more than 50 years as a leading U.S. equipment supplier serving the printed circuit board assembly (PCBA) industry.
Real Time with... IPC APEX EXPO 2025: Technica's Innovations and Partnerships
04/11/2025 | Real Time with...IPC APEX EXPOJason Perry of Technica USA and Robert Beber of Reeco share about the engagement at their extra-large booth at this year's show, where they showcased 11 pieces of equipment and announced the new partnership for Technica with Reeco, supplier of ESD clothing and workbenches. With a positive industry outlook despite global trade uncertainties, Technica has plans to expand in North America.
BEST Inc. Presents StencilQuik for Simplifying BGA Rework Challenges
04/02/2025 | BEST Inc.BEST Inc., a leader in electronic component rework services, training, and rework tools is thrilled to announce StencilQuik™ rework stencils. This innovative product is specifically designed for placing Ball Grid Arrays (BGAs) or Chip Scale Packages (CSPs) during the rework process.
MacDermid Alpha Introduces Reworkable Edgebond for High-Reliability Electronics
02/06/2025 | MacDermid Alpha Electronics SolutionsIn an era where high-performance and sustainable manufacturing practices are crucial, MacDermid Alpha Electronics Solutions is redefining industry standards with the launch of ALPHA® HiTech® CF31-4026.
PDR Offers Advanced Infrared Heating Technology for BGA Rework
12/02/2024 | PDRPDR Americas is proud to highlight its industry-leading solutions for BGA and SMT rework. As a trusted partner in electronics manufacturing, PDR’s rework stations deliver precision, reliability, and simplicity, setting a new standard for addressing the challenges of modern rework applications.