Magnetic Field Affects Electrons During Etching
March 31, 2016 | University of TokyoEstimated reading time: 1 minute
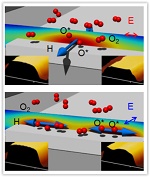
A Japanese and French international research group, using surface polishing employing light with a controlled direction of oscillation, has for the first time demonstrated that a magnetic field with extremely high frequency (in the petahertz rage. One petahertz corresponds to one trillion oscillation per second) can be used for nanofabrication.
The technology to create nanoscale flat surfaces is essential for the development of electronic devices and optical devices. However, conventional chemical and mechanical polishing methods damage the surface and leave behind impurities. To solve this problem, a University of Tokyo research group developed a non-contact light-based polishing technique called near-field etching that is capable of eliminating surface unevenness. However, it was thought that it was the electric field, not the magnetic field, which contributed to the polishing effect in near-field etching.
The research group of Associate Professor Takashi Yatsui at the University of Tokyo Graduate School of Engineering and Associate Professor Katsuyuki Nobusada at the Institute for Molecular Science and their colleagues examined surface irregularities of zirconia (ZrO2, a transparent material with a high refractive index also known as a type of imitation diamond) during the near-field etching process, and found that the magnetic field determined the properties of the etching process rather than the electric field.
“This discovery revealed that magnetic field oscillating with light frequency can be utilized for fabrication. Although light is an oscillating electric and magnetic field, a magnetic field oscillating with the frequency of visible light does not have any effect on materials. Thus, the effect of the magnetic field was ignored and only the effect of the electric field was considered for applications in light-based fabrication,” explains Yatsui. He continues, “Therefore this is a very surprising result that is in contradiction with what is considered common knowledge. We hope that this discovery will contribute not only to basic research but also to the fabrication of nanostructures for advanced optical and electrical devices.”
Suggested Items
Knocking Down the Bone Pile: Addressing End-of-life Component Solderability Issues, Part 4
07/15/2025 | Nash Bell -- Column: Knocking Down the Bone PileIn 1983, the Department of Defense identified that over 40% of military electronic system failures in the field were electrical, with approximately 50% attributed to poor solder connections. Investigations revealed that plated finishes, typically nickel or tin, were porous and non-intermetallic.
STMicroelectronics, Metalenz Sign a New License Agreement to Accelerate Metasurface Optics Adoption
07/14/2025 | STMicroelectronicsSTMicroelectronics, a global semiconductor leader serving customers across the spectrum of electronics applications and Metalenz, the pioneer of metasurface optics, announced a new license agreement.
Digital Twin Concept in Copper Electroplating Process Performance
07/11/2025 | Aga Franczak, Robrecht Belis, Elsyca N.V.PCB manufacturing involves transforming a design into a physical board while meeting specific requirements. Understanding these design specifications is crucial, as they directly impact the PCB's fabrication process, performance, and yield rate. One key design specification is copper thieving—the addition of “dummy” pads across the surface that are plated along with the features designed on the outer layers. The purpose of the process is to provide a uniform distribution of copper across the outer layers to make the plating current density and plating in the holes more uniform.
Global PCB Connections: Embedded Components—The Future of High-performance PCB Design
06/19/2025 | Jerome Larez -- Column: Global PCB ConnectionsA promising advancement in this space is the integration of embedded components directly within the PCB substrate. Embedded components—such as resistors, capacitors, and even semiconductors—can be placed within the internal layers of the PCB rather than mounted on the surface. This enables designers to maximize available real estate and improve performance, reliability, and manufacturability.
Preventing Surface Prep Defects and Ensuring Reliability
06/10/2025 | Marcy LaRont, PCB007 MagazineIn printed circuit board (PCB) fabrication, surface preparation is a critical process that ensures strong adhesion, reliable plating, and long-term product performance. Without proper surface treatment, manufacturers may encounter defects such as delamination, poor solder mask adhesion, and plating failures. This article examines key surface preparation techniques, common defects resulting from improper processes, and real-world case studies that illustrate best practices.