-
- News
- Books
Featured Books
- smt007 Magazine
Latest Issues
Current IssueIntelligent Test and Inspection
Are you ready to explore the cutting-edge advancements shaping the electronics manufacturing industry? The May 2025 issue of SMT007 Magazine is packed with insights, innovations, and expert perspectives that you won’t want to miss.
Do You Have X-ray Vision?
Has X-ray’s time finally come in electronics manufacturing? Join us in this issue of SMT007 Magazine, where we answer this question and others to bring more efficiency to your bottom line.
IPC APEX EXPO 2025: A Preview
It’s that time again. If you’re going to Anaheim for IPC APEX EXPO 2025, we’ll see you there. In the meantime, consider this issue of SMT007 Magazine to be your golden ticket to planning the show.
- Articles
- Columns
Search Console
- Links
- Media kit
||| MENU - smt007 Magazine
Happy’s Essential Skills: Failure Modes and Effects Analysis (FMEA)
April 6, 2016 | Happy HoldenEstimated reading time: 12 minutes
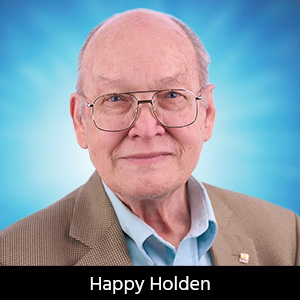
What is FMEA?
Failure modes and effects analysis (FMEA) is a systematic process to evaluate failure modes and causes associated with the design and manufacturing processes of a new product. It is somewhat similar to the potential problem analysis (PPA) phase of the Kepner-Tregoe program. Here is a list of activities for a FMEA:
1. Determine potential failure modes of each component or subassembly and causes associated with the designing and manufacturing of a product.
2. Identify actions which could be eliminate or reduce the chance of a potential failure occurring.
3. Document the process and give each mode a numeric rating for frequency of occurrence, criticality, and probability of detection.
4. Multiply these three numbers together to obtain the risk priority number (RPN), which is used to guide the design effort to the most critical problems first.
Two aspects of FMEA are particularly important: a team approach and timeliness. The team approach is vital because the broader the expertise that is brought to bear on making and assigning values to the failure mode list, the more effective the FMEA will be.
Timeliness is important because FMEA is primarily a preventive tool, which can help steer design decisions between alternatives before failure modes are designed-in, rather than redesigning after the failure occurs. FMEA is equally applicable to hardware or software, to components or systems.
Comparison to FTA
Another similar process is fault tree analysis (FTA). While FMEA is a bottom-up approach, FTA is top-down. FTA starts with the assumption of a system failure mode, and then works down through the system block diagram to look for possible causes of that mode.
Thus, FTA requires fairly complete, detailed information about the system, and is most effective after the system is well-defined. (FTA could be performed, in a limited way, on alternative system concepts; this could be used to help decide the best of several alternatives.) A separate FTA must be performed for each system failure mode.
FTA and FMEA are complimentary. Whenever possible, both should be used. For practical reasons, FTA should be limited to the really serious system-level failure modes, such as those involving safety or permanent system damage. FMEA can be used at the component, subassembly, and module level, to help optimize those modules. There are excellent discussions and examples of FTA in References 2 and 4, and it will not be discussed further in this column.
Benefits of FMEA
The RPN calculated by FMEA allows prioritization of the failure mode list, guiding design effort to the most critical areas first. It also provides a documentary record of the failure prevention efforts of the design team, which is helpful to management in gauging the quality and extent of the effort, to production in solving problems which occur despite these efforts, and to future projects which can benefit from all the work and thinking that went into the failure mode and cause lists.
Eliminating potential failure modes has both short term and long term benefits. The short term benefit is most often recognized because it represents savings of the costs of repair, retest, and downtime, which are objectively accountable. The long term benefit is much more difficult to measure, since it relates to the customer satisfaction or dissatisfaction with the product, and perception of its quality.
FMEA supports the design process by:
- Aiding in the objective evaluation of alternatives during design
- Increasing the probability that potential failure modes and their effects on system operation have been considered during design
- Providing additional information to aid in the planning of thorough and efficient test programs
- Developing a list of potential failure modes ranked according to their probable effect on the customer, thus establishing a priority system for design and test
- Providing an open, documented format for recommending and tracking risk-reducing actions
- Identifying known and potential failure modes which might otherwise be overlooked
- Exposing and documenting the ways a system can fail, and the effects of such failures
- Detecting primary but often minor failures which may cause serious secondary failures or consequent damage
- Detecting areas where "fail safe" or "fail soft" features are needed
- Providing a fresh viewpoint in understanding a system's functions
The uses of a FMEA report include:
- A formal record of the safety and reliability analysis and planning, to satisfy customers or regulatory agencies
- Evidence in litigation involving safety or reliability
- Design of diagnostic routines or built-in tests
- A basis for creating trouble-shooting procedures
- A means to consider and prevent manufacturing defects
- Problem follow-up and corrective action tracking
- A future reference to aid in analyzing field failures, evaluating design changes, or developing improved designs
Page 1 of 5
Suggested Items
The Shaughnessy Report: Solving the Data Package Puzzle
05/12/2025 | Andy Shaughnessy -- Column: The Shaughnessy ReportIf you ask fabricators about their biggest challenges, they’ll often point at PCB designers—the readers of this magazine. Yes, you! Why is it so difficult to create the ideal data package? It’s a fairly straightforward task. But this part of the design process keeps tripping up designers, even those who started in the industry before Pink Floyd split up.
I-Connect007 Editor’s Choice: Five Must-Reads for the Week
05/09/2025 | Andy Shaughnessy, Design007 MagazineTrade show season is wrapping up as we head into summer. Where has the time gone? I hope you all get the chance to take a vacation this year, because I know you’ve earned one. Speaking of which, when was my last vacay? If I can’t remember, it’s probably time for one. It’s been a busy week in electronics, with fallout from the back-and-forth on tariffs taking up most of the oxygen in the room. We have quite an assortment of articles and columns for you in this installment of Must-Reads. See you next time.
Imec Coordinates EU Chips Design Platform
05/09/2025 | ImecA consortium of 12 European partners, coordinated by imec, has been selected in the framework of the European Chips Act to develop the EU Chips Design Platform.
New Issue of Design007 Magazine: Are Your Data Packages Less Than Ideal?
05/09/2025 | I-Connect007 Editorial TeamWhy is it so difficult to create the ideal data package? Many of these simple errors can be alleviated by paying attention to detail—and knowing what issues to look out for. So, this month, our experts weigh in on the best practices for creating the ideal data package for your design.
RF PCB Design Tips and Tricks
05/08/2025 | Cherie Litson, EPTAC MIT CID/CID+There are many great books, videos, and information online about designing PCBs for RF circuits. A few of my favorite RF sources are Hans Rosenberg, Stephen Chavez, and Rick Hartley, but there are many more. These PCB design engineers have a very good perspective on what it takes to take an RF design from schematic concept to PCB layout.