-
- News
- Books
Featured Books
- design007 Magazine
Latest Issues
Current IssueShowing Some Constraint
A strong design constraint strategy carefully balances a wide range of electrical and manufacturing trade-offs. This month, we explore the key requirements, common challenges, and best practices behind building an effective constraint strategy.
All About That Route
Most designers favor manual routing, but today's interactive autorouters may be changing designers' minds by allowing users more direct control. In this issue, our expert contributors discuss a variety of manual and autorouting strategies.
Creating the Ideal Data Package
Why is it so difficult to create the ideal data package? Many of these simple errors can be alleviated by paying attention to detail—and knowing what issues to look out for. So, this month, our experts weigh in on the best practices for creating the ideal design data package for your design.
- Articles
- Columns
- Links
- Media kit
||| MENU - design007 Magazine
Brooks' Bits: How Many Vias Does It Take To…?
May 4, 2016 | Douglas G. BrooksEstimated reading time: 2 minutes
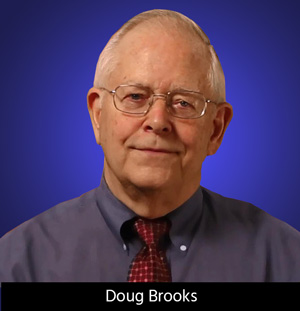
Sounds like the opening words of a bad joke. Well, here’s the answer, and it’s no joke: One! That’s right. No matter how much current you are putting down the trace, all you need is a single via. And a small one, at that.
OK, that last statement might not be true in EVERY single case. But it is true in a LOT more cases than you think. I will explain why in this column.
During 2015, I enjoyed a very productive collaboration with Dr. Johannes Adam, from Leimen, Germany. That collaboration resulted in several papers, but one in particular is relevant for this column, “Via Currents and Temperatures.” In that paper, we used a simulation tool, thermal risk management (TRM), developed by Dr. Adam, to simulate current flowing through a via and then determine the temperature of the via. The conventional wisdom is that the conducting cross-sectional area of the via should be the same as (or greater than) the cross-sectional area of the trace (conductor.) IPC 2152 explicitly endorses this:
The cross-sectional area of a via should have at least the same cross-sectional area as the conductor or be larger than the conductor coming into it. If the via has less cross-sectional area than the conductor, then multiple vias can be used to maintain the same cross-sectional area as the conductor.
But our results contradicted this; they suggested that the temperature of the via was controlled by the trace, and as long as the trace was sized correctly, any old (single) via was good enough.
If there was ever a result that cried out “show me,” this was it.
So I set out on a path to build a test board, test it, and verify the simulation results. This type of study would not have been possible without the cooperation of several people and organizations. In particular, I want to thank my longtime partner Dave Graves (now with Monsoon Solutions in Bellevue, Washington) for helping prepare the final artwork for the test board. C-Therm Technologies (Fredericton, New Brunswick) graciously measured the thermal conductivity of the board material to facilitate the simulation. And a special thanks to Prototron Circuits of Redmond, Washington, who provided the test boards and also the microsectioning work and measurements. And my collaborator on trace thermal issues, Johannes Adam, continues to be a great help in evaluating results.
Figure 1 illustrates the relevant portion of the test board. There are two 0.5 oz. test traces, each six inches long, each consisting of two, three-inch segments (top and bottom) connected by a single 10 mil diameter via. The via is plated to approximately one ounce. One test trace is 27 mil wide, providing approximately the same cross-sectional area as the conducting area of the via. The other trace is 200 mil wide. It is important to note that the vias are identical for the two traces.
To read this entire article, which appeared in the March 2016 issue of The PCB Design Magazine, click here.
Suggested Items
TRI Unveils New platform for Diverse Board Sizes Search Submit
07/14/2025 | TRITest Research, Inc. (TRI), the leading test and inspection systems provider for the electronics manufacturing industry, proudly introduces a new size configuration for SPI and AOI Models.
Seeing a Future in Mexico
07/09/2025 | Michelle Te, I-Connect007The Global Electronics Association (formerly known as IPC) has been instrumental in fostering a partnership with Guanajuato, a state north of Mexico City with 12 industrial clusters and close to 150 companies involved in electronics. This past spring, Alejandro Hernández, the undersecretary for investment promotion in Guanajuato, attended IPC APEX EXPO 2025 at the invitation of IPC Mexico Director Lorena Villanueva, where he met with several companies to discuss the opportunities available in Mexico. He is inviting electronics-related companies seeking long-term investment in a centrally located area with access to highways, railways, and ports.
The Global Electronics Association Releases IPC-8911: First-Ever Conductive Yarn Standard for E-Textile Application
07/02/2025 | Global Electronics AssociationThe Global Electronics Association announces the release of IPC-8911, Requirements for Conductive Yarns for E-Textiles Applications. This first-of-its-kind global standard establishes a clear framework for classifying, designating, and qualifying conductive yarns—helping to address longstanding challenges in supply chain communication, product testing, and material selection within the growing e-textiles industry.
IPC-CFX, 2.0: How to Use the QPL Effectively
07/02/2025 | Chris Jorgensen, Global Electronics AssociationIn part one of this series, we discussed the new features in CFX Version 2.0 and their implications for improved inter-machine communication. But what about bringing this new functionality to the shop floor? The IPC-CFX-2591 QPL is a powerful technical resource for manufacturers seeking CFX-enabled equipment. The Qualified Product List (QPL) helps streamline equipment selection by listing models verified for CFX compliance through a robust third-party virtual qualification process.
The Knowledge Base: A Conference for Cleaning and Coating of Mission-critical Electronics
07/08/2025 | Mike Konrad -- Column: The Knowledge BaseIn electronics manufacturing, there’s a dangerous misconception that cleaning and coating are standalone options, that they operate in different lanes, and that one can compensate for the other. Let’s clear that up now. Cleaning and conformal coating are not separate decisions. They are two chapters in the same story—the story of reliability.