-
- News
- Books
Featured Books
- pcb007 Magazine
Latest Issues
Current IssueSales: From Pitch to PO
From the first cold call to finally receiving that first purchase order, the July PCB007 Magazine breaks down some critical parts of the sales stack. To up your sales game, read on!
The Hole Truth: Via Integrity in an HDI World
From the drilled hole to registration across multiple sequential lamination cycles, to the quality of your copper plating, via reliability in an HDI world is becoming an ever-greater challenge. This month we look at “The Hole Truth,” from creating the “perfect” via to how you can assure via quality and reliability, the first time, every time.
In Pursuit of Perfection: Defect Reduction
For bare PCB board fabrication, defect reduction is a critical aspect of a company's bottom line profitability. In this issue, we examine how imaging, etching, and plating processes can provide information and insight into reducing defects and increasing yields.
- Articles
- Columns
- Links
- Media kit
||| MENU - pcb007 Magazine
The Future of Computer-Integrated Manufacturing in the PCB Industry
May 9, 2016 | Pete Starkey, I-Connect007Estimated reading time: 7 minutes
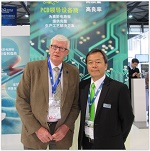
Computer-integrated manufacturing is already a proven reality in the PCB industry for those prepared to make the investment, and results in improved quality and reduced costs. The biggest barrier to its general adoption is the reluctance of some equipment manufacturers to communicate in a uniform data format. But trade associations such as TPCA are promoting cooperation and equipment suppliers are realising the benefits of uniformity, and that the long-term consequence of not cooperating is to be left out of the game. I sat down in the booth of Manz China Souzhou Ltd. During CPCA recently, and I spoke to Alex Liu, head of the PCB business unit, who explained the situation.
Pete Starkey: Alex, good morning and thank you for joining us. Alex, we are discussing computer-integrated manufacturing. Maybe you could explain to us how this fits into the PCB manufacturing process. What is the current state of the art? And what will be the developments going forward?
Alex Liu: Okay, so let me first explain why we first came up with this idea of computer-integrated manufacturing systems. The PCB manufacturing process is physically divided into different areas—some in the clean room, some is in the yellow-light area, and some in the plating areas, so how do we interconnect all the data? The first idea that we came up with was to use a computing system to interlink all of the signals and all of the parameter settings. Secondly, PCB manufacture relies heavily on labor to operate machines. And now, even in China, labor costs are getting higher and higher. And training costs are high also, not to mention that the people-exchange rates are very high in some areas, which means that the investment in operator experience is lost when people transfer. And thirdly, we are selling it as a packaged solution; we want to sell an integrated solution to the customer. So we should be able to connect all our systems into one so that the customer gets the best benefits. These were the three ideas behind our systems.
What most benefits the customer is having very easy access over the computing system. For example, if you are at a different manufacturing location, then you can easily use this system to have the same parameter settings, tracking, and a constant process, which will also improve your quality. So I think that’s a major benefit to the customer.
Starkey: If we take the PCB manufacturing process, typically where would you derive the information and where would you make the connections?
Liu: Our first product release is in the plating area, especially after de-smear, PTH and copper plating. Our system was first launched with a Korean customer. They want tracking of all the copper thicknesses being plated. So they have inspection feeding back to their data bank and their data bank will give references to compare to the original data. If they find something different, then their data bank will give us an instruction that will connect to our control system. And that will automatically change the manufacturing parameters on the line to improve the quality to reach their target.
Starkey: So, when we talk about manufacturing parameters in the context of a plating process, what specific parameters would you be measuring, recording, and feeding back?
Liu: Take plating, because our first project was in PTH. It's pretty thin copper, so you need a cross-section. Cross-sectioning cannot be in-line, you have to do it off-line. So once the quality control engineer has input the cross-section data to the system, the system automatically analyses what parameters resulted in this thickness of copper being plated. Of course the reference data was created by the customer as best-experience data and they would give us a recommendation that, for example, we should change the line speed, the spray, or whatever, and then we control the outcome and the results.
Starkey: So you can customize the system to suit the particular requirements of each customer at each stage of the manufacturing process.
Liu: Correct. I just mentioned that was our first approach. Our second approach was in the yellow-light area. We have our etching solutions and also we integrate with our LDI. As you may know, we merged with another company, KLEO in Germany, for LDI last year. So we are able to integrate from the imaging process until etching. We connect with the visual inspections system, taking the picture and then measuring the line space and width to verify that the etching results meet their requirements.
If not, they feedback a signal to us. We can easily change the parameters in the imaging system or the etching process. For example, we change the line speed, we change the spray or we activate the pneumatic etching or not. So we relay to the customer’s data bank so that they can give us the best recipe to create the pattern that they want. So that is the second approach that we have taken.
Then, combining these two projects, we found that we were able to connect the lines so they can export signals for us, then it's easier to control the whole line integrated into one. So for customers it's very easy. They just key in what kind of result they want, and everything is controlled by computing. It makes life really easy.
Page 1 of 2
Testimonial
"The I-Connect007 team is outstanding—kind, responsive, and a true marketing partner. Their design team created fresh, eye-catching ads, and their editorial support polished our content to let our brand shine. Thank you all! "
Sweeney Ng - CEE PCBSuggested Items
Designers Notebook: Basic PCB Planning Criteria—Establishing Design Constraints
07/22/2025 | Vern Solberg -- Column: Designer's NotebookPrinted circuit board development flows more smoothly when all critical issues are predefined and understood from the start. As a basic planning strategy, the designer must first consider the product performance criteria, then determine the specific industry standards or specifications that the product must meet. Planning also includes a review of all significant issues that may affect the product’s manufacture, performance, reliability, overall quality, and safety.
I-Connect007 Editor’s Choice: Five Must-Reads for the Week
07/18/2025 | Nolan Johnson, I-Connect007It may be the middle of the summer, but the news doesn’t quit, and there’s plenty to talk about this week, whether you’re talking technical or on a global scale. When I have to choose six items instead of my regular five, you know it’s good. I start by highlighting my interview with Martyn Gaudion on his latest book, share some concerning tariff news, follow that up with some promising (and not-so-promising) investments, and feature a paper from last January’s inaugural Pan-European Design Conference.
Elephantech Launches World’s Smallest-Class Copper Nanofiller
07/17/2025 | ElephantechJapanese deep-tech startup Elephantech has launched its cutting-edge 15 nm class copper nanofiller – the smallest class available globally. This breakthrough makes Elephantech one of the first companies in the world to provide such advanced material for commercial use.
Copper Price Surge Raises Alarms for Electronics
07/15/2025 | Global Electronics Association Advocacy and Government Relations TeamThe copper market is experiencing major turbulence in the wake of U.S. President Donald Trump’s announcement of a 50% tariff on imported copper effective Aug. 1. Recent news reports, including from the New York Times, sent U.S. copper futures soaring to record highs, climbing nearly 13% in a single day as manufacturers braced for supply shocks and surging costs.
I-Connect007 Editor’s Choice: Five Must-Reads for the Week
07/11/2025 | Andy Shaughnessy, Design007 MagazineThis week, we have quite a variety of news items and articles for you. News continues to stream out of Washington, D.C., with tariffs rearing their controversial head again. Because these tariffs are targeted at overseas copper manufacturers, this news has a direct effect on our industry.I-Connect007 Editor’s Choice: Five Must-Reads for the Week