-
- News
- Books
Featured Books
- design007 Magazine
Latest Issues
Current IssueAll About That Route
Most designers favor manual routing, but today's interactive autorouters may be changing designers' minds by allowing users more direct control. In this issue, our expert contributors discuss a variety of manual and autorouting strategies.
Creating the Ideal Data Package
Why is it so difficult to create the ideal data package? Many of these simple errors can be alleviated by paying attention to detail—and knowing what issues to look out for. So, this month, our experts weigh in on the best practices for creating the ideal design data package for your design.
Designing Through the Noise
Our experts discuss the constantly evolving world of RF design, including the many tradeoffs, material considerations, and design tips and techniques that designers and design engineers need to know to succeed in this high-frequency realm.
- Articles
- Columns
- Links
- Media kit
||| MENU - design007 Magazine
Designers Notebook: Flexible and Rigid-Flex Circuit Design Principles, Part 6
May 26, 2016 | Vern Solberg, ConsultantEstimated reading time: 5 minutes
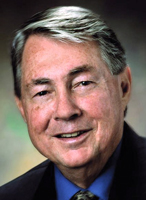
The designer is generally under pressure to release the documentation and get the flexible circuit into production. There is, however, a great deal at risk. Setting up for medium-to-high volume manufacturing requires significant physical and monetary resources. To avoid potential heat from management, the designer must insist on prototyping the product and a thorough design review prior to release.
DFM Review Criteria
Comprehensive documentation is vital. The intent is to provide the fabricator with a detailed list and description of the materials specified for the flexible circuit construction, materials stack-up, reinforced/stiffened areas, critical thickness areas, and to specify a solder-compatible surface finish for all component land pattern features. For the more complex multilayer and rigid-flex applications include cross-sectional views. Critical bend or radius locations must be identified with reference dimensions and it will be helpful to furnish separate views showing an installed flex configuration.
The primary references for evaluating the flexible circuit are tooling holes and fiducial targets. Non-plated tooling holes are commonly used for maintaining the position of the circuit during singulation and, when backed with or part of a rigid section, assembly processing. Fiducial features should be furnished in each circuit section or localized termination area to provide an unvarying ‘datum’ reference for more precise component placement. The optimum fiducial is a solid filled 0.25 to 0.5 mm (.010” to .020”) diameter circle. Cover layer material must provide enough clearance to ensure that it does not overlap onto the fiducial target features during the cover layer-to-base circuit lamination process.
The use of fiducial features is a common technique for:
- Solder stencil x, y and theta alignment
- Precise surface mount component placement
- Reducing the effects of variable material shrinkage conditions
- Compensation for any random distortions in flexible materials
Assembly documentation will include a bill of material, approved vendor list, component reference designators and any special requirements. Develop clear, detailed drawings and assembly instructions. This document should include component outlines and general locations. The CAD file will furnish precise component X-Y coordinates and orientation data needed for assembly processing. All SMT devices are aligned and placed onto their respective land patterns using the body center as a reference point for placement coordinates. The fiducial targets described above will assist in establishing these exact X-Y coordinates for solder printing, component placement and orientation. With flexibility comes inherent dimensional instability relative to hardboards or solid metal objects. When multiple component mounting sites are separated by excessive distance it is suggested that multiple fiducial features be provided. The use of multiple datum features is a common technique for reducing or eliminating the effects of variable shrinkage or process distortion in flexible materials. Multiple locations will provide a tighter tolerance within each datum zone or termination area while relaxing the need to maintain a tight tolerance of the flexible interface between other termination areas.
Nesting and Palletizing
Flexible circuit units can be furnished in panelized formats. This format will improve both fabrication and assembly process efficiency and maximizing material utilization. Automated handling for in-line assembly processing for flexible circuits furnished with a provisional rigid backing and multilayer rigid-flex circuits requires a somewhat uniform board outline. Conveyor systems on assembly process equipment are adjustable, but they rely on at least two parallel edges and systems may have different requirements as far as maximum and minimum panel size:
- Simple array format (rows and columns in one direction)
- Nested array format (maximizing area utilization)
- Opposing orientation array format (minimizing material waste)
Assembly Process Variations
The components selected—passive and active devices, surface mount and/or pin-in-hole, coarse pitch, fine-pitch, BGA, CSP—will influence the assembly methodologies adopted. The first stage for traditional surface mount assembly is solder paste deposition. Solder paste is commonly applied using precision dispensing systems or stencil printing. Dispensing is ideal for prototype or low-volume assembly because it can be programmed directly from the CAD data to apply solder to the component mounting sites in any pattern and volume (and it does not require additional tooling). For medium- to high-volume assembly, solder stencil printing is the most efficient. In developing the solder paste stencil for surface mount assembly, process engineers will likely utilize the basic land pattern feature geometries furnished in the CAD files developed for flexible circuit fabrication.
Land pattern geometries for a majority of the passive surface mount components are relatively uniform while lead-frame, ball grid array and fine-pitch ball grid array packaged ICs are furnished in a wide number of pitch and contact geometry variations. To ensure solder paste volumes are optimized, the assembly specialist may choose to modify the CAD data to make subtle changes to the land pattern aperture geometry. And depending on the solder alloy composition selected, the engineer may choose to reduce or increase solder paste print volumes at key locations.
Following solder paste deposition and inspection, the unit will shuttle to the assembly system(s) for surface mount component placement and another inspection step to ensure all components are in position. The final step of the surface mount assembly process is reflow soldering. In this process, the circuit assembly is gradually heated to 235°C allowing the solder composition to become liquidus, completing the joining of component terminals to the circuit land patterns.
Although several methodologies are available for mass reflow soldering, forced air/gas convection systems will likely remain the preferred method for electro-mechanical joining surface mount components to flexible and rigid-flex products. Solder attachment of PiH devices, on the other hand, may employ a simple hand soldering process. For higher-volume applications it may be more efficient to utilize selective wave or fountain soldering, programmed laser heated wire soldering or, for ribbon type contact interface, hot bar thermo compression bond processing.
Design guidelines for flexible and rigid flex circuit applications are detailed further in IPC-2223 while workmanship criteria is defined in IPC-6013, Qualification and Performance Specification for Flexible Printed Boards. Always consult with suppliers during the planning phase of the design program. Review and understand the supplier’s design rules, capabilities and limitations. When the supplier is selected, designate a primary contact and establish a review cycle throughout design program.
Vern Solberg is an independent technical consultant based in Saratoga, California, specializing in SMT and microelectronics design and manufacturing technology. To reach Solberg click here.
Suggested Items
KYZEN to Highlight Understencil and PCB Cleaners at SMTA Querétaro Expo and Tech Forum
07/09/2025 | KYZEN'KYZEN, the global leader in innovative environmentally responsible cleaning chemistries, will exhibit at the SMTA Querétaro Expo & Tech Forum, scheduled to take place Thursday, July 24, at Centro de Congresos y Teatro Metropolitano de Querétaro.
Driving Innovation: Direct Imaging vs. Conventional Exposure
07/01/2025 | Simon Khesin -- Column: Driving InnovationMy first camera used Kodak film. I even experimented with developing photos in the bathroom, though I usually dropped the film off at a Kodak center and received the prints two weeks later, only to discover that some images were out of focus or poorly framed. Today, every smartphone contains a high-quality camera capable of producing stunning images instantly.
Hands-On Demos Now Available for Apollo Seiko’s EF and AF Selective Soldering Lines
06/30/2025 | Apollo SeikoApollo Seiko, a leading innovator in soldering technology, is excited to spotlight its expanded lineup of EF and AF Series Selective Soldering Systems, now available for live demonstrations in its newly dedicated demo room.
Indium Corporation Expert to Present on Automotive and Industrial Solder Bonding Solutions at Global Electronics Association Workshop
06/26/2025 | IndiumIndium Corporation Principal Engineer, Advanced Materials, Andy Mackie, Ph.D., MSc, will deliver a technical presentation on innovative solder bonding solutions for automotive and industrial applications at the Global Electronics A
Fresh PCB Concepts: Assembly Challenges with Micro Components and Standard Solder Mask Practices
06/26/2025 | Team NCAB -- Column: Fresh PCB ConceptsMicro components have redefined what is possible in PCB design. With package sizes like 01005 and 0201 becoming more common in high-density layouts, designers are now expected to pack more performance into smaller spaces than ever before. While these advancements support miniaturization and functionality, they introduce new assembly challenges, particularly with traditional solder mask and legend application processes.