Better Combustion for Power Generation
May 31, 2016 | DOE/Oak Ridge National LaboratoryEstimated reading time: 10 minutes
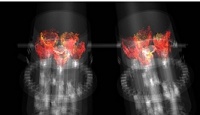
In the United States, the use of natural gas for electricity generation continues to grow. The driving forces behind this development? A boom in domestic natural gas production, historically low prices, and increased scrutiny over fossil fuels' carbon emissions. Though coal still accounts for about a third of US electricity generation, utility companies are pivoting to cleaner natural gas to replace decommissioned coal plants.
Low-maintenance, high-efficiency gas turbines are playing an important role in this transition, boosting the economic attractiveness of natural gas-derived electricity. General Electric (GE), a world leader in industrial power generation technology and the world's largest supplier of gas turbines, considers gas-fired power generation a key growth sector of its business and a practical step toward reducing global greenhouse gas emissions. When burned for electricity, natural gas emits half the carbon dioxide that coal does. It also requires fewer environmental controls.
"Advanced gas turbine technology gives customers one of the lowest installed costs per kilowatt," said Joe Citeno, combustion engineering manager for GE Power. "We see it as a staple for increased power generation around the world."
GE's H-class heavy-duty gas turbines are currently the world's largest and most efficient gas turbines, capable of converting fuel and air into electricity at more than 62 percent power-plant efficiency when matched with a steam turbine generator, a setup known as combined cycle. By comparison, today's simple cycle power plants (gas turbine generator only) operate with efficiencies ranging between 33 and 44 percent depending on the size and model.
GE is constantly searching for ways to improve the performance and overall value of its products. A single percent increase in gas turbine efficiency equates to millions of dollars in saved fuel costs for GE's customers and tons of carbon dioxide spared from the atmosphere. For a 1 gigawatt power plant, a 1 percent improvement in efficiency saves 17,000 metric tons of carbon dioxide emissions a year, equivalent to removing more than 3,500 vehicles from the road. Applying such an efficiency gain across the US combined-cycle fleet (approximately 200 gigawatts) would save about 3.5 million metric tons of carbon dioxide each year.
In 2015, the search for efficiency gains led GE to tackle one of the most complex problems in science and engineering--instabilities in gas turbine combustors. The journey led the company to the Titan supercomputer at the Oak Ridge Leadership Computing Facility (OLCF), a US Department of Energy (DOE) Office of Science User Facility located at DOE's Oak Ridge National Laboratory.
Balancing act
Simultaneously increasing the efficiency and reducing the emissions of natural gas-powered turbines is a delicate balancing act. It requires an intricate understanding of these massive energy-converting machines -- their materials, aerodynamics, and heat transfer, as well as how effectively they combust, or burn, fuel. Of all these factors, combustion physics is perhaps the most complex.
In an H-class gas turbine, combustion takes place within 6-foot-long chambers at high temperature and pressure. Much like a car engine has multiple cylinders, GE's H-class turbines possess a ring of 12 or 16 combustors, each capable of burning nearly three tons of fuel and air per minute at firing temperatures exceeding 1,500 degrees Celsius. The extreme conditions make it one of the most difficult processes to test at GE's gas turbine facility in Greenville, South Carolina.
At higher temperatures, gas turbines produce more electricity. They also produce more emissions, such as nitrogen oxides (NOx), a group of reactive gases that are regulated at the state and federal levels. To reduce emissions, GE's Dry Low NOx combustion technology mixes fuel with air before burning it in the combustor.
"When the fuel and air are nearly perfectly mixed, you have the lowest emissions," said Jin Yan, manager of the computational combustion lab at GE's Global Research Center. "Imagine 20 tractor-trailers full of combustible fuel-air mixture. One combustor burns that amount every minute. In the process, it produces less than a tea cup (several ounces) of NOx emissions."
Such precise burning can lead to other problems, specifically an unstable flame. Inside a combustor, instabilities in the flame can cause deafening acoustic pulsations--essentially noise-induced pressure waves. These pulsations can affect turbine performance. At their worst, they can wear out the machinery in a matter of minutes. For this reason, whenever a new pulsation is detected, understanding its cause and predicting whether it might affect future products becomes a high priority for the design team.
Page 1 of 3
Suggested Items
TRI to Unveil New High-Throughput AOI and AXI at productronica 2023
09/15/2023 | TRITest Research, Inc. (TRI), the leading test and inspection systems provider for the electronics manufacturing industry, will join productronica 2023, which will be held at Messe München Center from November 14 – 17, 2023.
UK Space Agency Launches Consultation on Variable Liability Limits for Orbital Operations
09/15/2023 | UK Space AgencyThe proposals from the UK Space Agency follow a review into the UK’s approach to setting the amount of an operator’s liability in licences for orbital operations, a key commitment of the government’s National Space Strategy.
MediaTek Successfully Develops First Chip Using TSMC's 3nm Process, Set for Volume Production in 2024
09/14/2023 | MediaTekMediaTek and TSMC announced that MediaTek has successfully developed its first chip using TSMC's leading-edge 3nm technology, taping out MediaTek’s flagship Dimensity system-on-chip (SoC) with volume production expected next year.
MKS’ Atotech to Participate in IPCA Expo 2023
09/14/2023 | MKS’ AtotechMKS’ Atotech, a leading surface finishing brand of MKS Instruments, will participate in the upcoming IPCA Expo at Bangalore International Exhibition Centre (BIEC) and showcase its latest PCB manufacturing solutions from September 13 – 15.
Comtech Unveils New BRIDGE Solutions to Increase Access to Global Hybrid Connectivity
09/12/2023 | Business WireComtech launched its new blended, resilient, integrated, digital, global, end-to-end (BRIDGE) connectivity solutions. Comtech’s BRIDGE solutions provide portable, adaptable, full-service communications networks that can be established in a matter of hours and help “bridge the gap” for traditional satellite and terrestrial infrastructures.