-
- News
- Books
Featured Books
- smt007 Magazine
Latest Issues
Current IssueIntelligent Test and Inspection
Are you ready to explore the cutting-edge advancements shaping the electronics manufacturing industry? The May 2025 issue of SMT007 Magazine is packed with insights, innovations, and expert perspectives that you won’t want to miss.
Do You Have X-ray Vision?
Has X-ray’s time finally come in electronics manufacturing? Join us in this issue of SMT007 Magazine, where we answer this question and others to bring more efficiency to your bottom line.
IPC APEX EXPO 2025: A Preview
It’s that time again. If you’re going to Anaheim for IPC APEX EXPO 2025, we’ll see you there. In the meantime, consider this issue of SMT007 Magazine to be your golden ticket to planning the show.
- Articles
- Columns
Search Console
- Links
- Media kit
||| MENU - smt007 Magazine
The Reliability Factor in Solder Paste Printing
June 24, 2016 | Stephen Las Marias, I-Connect007Estimated reading time: 1 minute
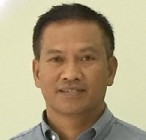
Knoll Evangelista is the director of the EMS Components and Group Operations of Laguna, Philippines-based electronics manufacturing services firm EMS Components Assembly Inc.
With more than 25 years in the electronics assembly industry, Evangelista has seen the evolution of the soldering process—from adhesive component mounting with the solder wave machines to screen printing with reflow ovens. He had also set up over 35 SMT lines for high volume production of products ranging from storage devices, consumer electronics, automotive electronics, and medical devices.
In an interview with SMT Magazine, Evangelista speaks about the solder paste printing challenge, what factors impact the process, and best practices to consider.
Stephen Las Marias: From your perspective, what are the biggest challenges when it comes to solder paste printing?
Knoll Evangelista: Reliability of solder joints in electronic products is the biggest challenge, and it depends on the following factors: stencil printing and quality of reflow soldering.
Las Marias: How does the solder paste material impact the process?
Evangelista: The size of the solder paste granules has an impact on the process as it depends on components to be mounted. The pitch distance of ICs, the ball array size, and the distance of BGAs have to be considered in selecting the solder paste material.
Las Marias: How do the tighter tolerances and even narrower PCB lines and spacing affect the solder paste printing process?
Evangelista: More than 50% of defects in assembly of printed circuit boards are attributed to the solder paste printing process. The volume of paste deposit during screen printing is a big factor impacting the quality of solder joints. It requires design of experiments (DOE) to get the right parameters of screen printing machine. It also involves optical inspection to measure the volume of paste deposit to assure consistency of paste application.
The surface mount components such as chip scale packages (CSP), fine pitch BGAs are the challenges in stencil printing and reflow profiling capabilities. Due to tighter tolerances, 3D X-ray inspection is required, which offers capabilities beyond those of microscopes and naked eye.
Editor's Note: This article originally appeared in the June 2016 issue of SMT Magazine.
Suggested Items
Solder Paste Exploration
06/02/2016 | Stephen Las Marias, I-Connect007From the manufacturers of solder pastes, to equipment makers, all the way to the solder paste inspection guys, and the electronics assemblers who are using their products, I talked to the supply chain to find out what’s going on in the solder paste printing process, what factors impact the process, the challenges, and the best practices to consider to be able to address those challenges and improve efficiencies and yield in the SMT line.
June 2016 Issue of SMT Magazine Available Now
06/02/2016 | I-Connect007The June 2016 issue of SMT Magazine discusses the challenges, best practices, and critical factors to consider in solder paste printing amid tighter tolerances and smaller pitches, lines and spaces.