-
- News
- Books
Featured Books
- pcb007 Magazine
Latest Issues
Current IssueVoices of the Industry
We take the pulse of the PCB industry by sharing insights from leading fabricators and suppliers in this month's issue. We've gathered their thoughts on the new U.S. administration, spending, the war in Ukraine, and their most pressing needs. It’s an eye-opening and enlightening look behind the curtain.
The Essential Guide to Surface Finishes
We go back to basics this month with a recount of a little history, and look forward to addressing the many challenges that high density, high frequency, adhesion, SI, and corrosion concerns for harsh environments bring to the fore. We compare and contrast surface finishes by type and application, take a hard look at the many iterations of gold plating, and address palladium as a surface finish.
It's Show Time!
In this month’s issue of PCB007 Magazine we reimagine the possibilities featuring stories all about IPC APEX EXPO 2025—covering what to look forward to, and what you don’t want to miss.
- Articles
- Columns
Search Console
- Links
- Media kit
||| MENU - pcb007 Magazine
Happy’s Essential Skills: Design for Manufacturing and Assembly, Part 1
June 29, 2016 | Happy HoldenEstimated reading time: 9 minutes
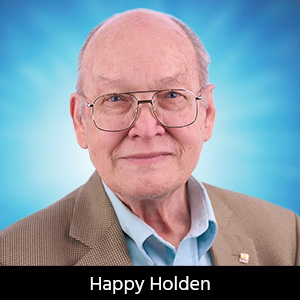
Advances in interconnection technologies have occurred in response to the evolution of component packages, electronic technology and increasing complex functions. Therefore, it comes as no surprise that various forms of printed wiring remain the most popular and cost-effective method of interconnections.
Manufacturing, assembly and test technologies have responded by improvements in their technologies. These increased capabilities have made selection of technologies, design rules and features so complex that a new function has developed to allow for the prediction and selection of design parameters and performance versus manufacturing costs. This is the planning for design, fabrication and assembly. This activity has also been called design for manufacturing and assembly (DFM/A) or sometimes predictive engineering. It is essentially the selection of design features and options that promote cost-competitive manufacturing, assembly, and test practices. Later in this column, I will offer a process to define producibility unique to each design or manufacturing process.
The purpose of this column is to provide information, concepts, and processes that lead to a thoughtfully and competitively designed printed circuit, ensuring that all pertinent design and layout variables have been considered.
Originators: Dewhurst & Boothroyd
Modern DFMA stems from the ideas of university professors Goefrey Dewhurst at University of Massachusetts -Amherst and Jeffery Boothroyd at University of Rhode Island [1]. These Manufacturing Engineering professors came up with the concept that you could predict the assembly time, dificulty and cost by cateloging and summing all the kinematic actions it takes during assembly. This concept became so accurate that it was used to predict assembly while a product was still in the design phase. Thus as a predictive metric, it became Design for Manufacturing—DfM. Today this technology is taught in universities and used by most large OEMs around the world. The Dewhurst & Boothroyd software (Table 1 and Figures 1a & b) consists of:
The D&B techniques consist of analyzing an assembly for these features:
- The need for this part
- How many fasteners are required
- The number of different fastener types
- The number of difficult-to-assemble parts or subassemblies
- The number of motions and twist/turns involved in each assembly step
- The role of tooling and fixturing
The resulting analysis shows a:
- Total part count
- Theoretical minimum of parts or preassembled item (Pmin)
- Assembly efficiency (ease of assembly—AE)
- Assembly time
The analysis uses software to measure:
- Prototype evaluations based on either actual or 3D models using Boothroyd and Dewhurst method.
- Pmin is a measure of the complexity of the product. In general, the more functionality there is in a product, the higher the Pmin value.
- Assembly Efficiency (AE) is a ratio of the theoretical minimum number of parts (Pmin) to the estimated assembly time. An approximation is used to compute AE (2.933 seconds per part), so AE values are used for relative comparisons only.
Table 1: The Dewhurst & Boothroyd DFMA software.
Figure 1a: The Dewhurst & Boothroyd DFMA software.
Figure 1b: The Dewhurst & Boothroyd DFMA software.
Page 1 of 4
Suggested Items
Benchmark Reports Revenue of $632 Million in 1Q 2025 Results
04/30/2025 | BUSINESS WIREBenchmark Electronics, Inc. announced financial results for the first quarter ended March 31, 2025.
Fresh PCB Concepts: Key Considerations for Reliability, Performance, and Compliance in PCBs
04/29/2025 | Team NCAB -- Column: Fresh PCB ConceptsAs a field application engineer with many years of experience, I’ve conducted thousands of designs for manufacturing (DFM) analyses on printed circuit boards (PCBs). From basic one-layer boards to complex high density interconnect (HDI) designs, I’ve provided technical advice across a wide spectrum of technologies.
TMEIC Breaks Ground on Third Manufacturing Facility in Texas
04/29/2025 | TMEICTMEIC Corporation Americas, a subsidiary of TMEIC Corporation (Japan), proudly announces the groundbreaking of its third U.S. manufacturing facility, located in Waller County, Texas.
Libra Industries Joins the National Association of Manufacturers (NAM) to Advance American Manufacturing
04/29/2025 | Libra IndustriesLibra Industries, a leading provider of systems integration and electronics manufacturing services (EMS), is pleased to announce its new membership with the National Association of Manufacturers (NAM), the largest and most influential manufacturing trade association in the United States.
QuantumScape, Murata Announce Framework for Ceramics Collaboration
04/25/2025 | BUSINESS WIREQuantumScape Corporation, a global leader in next-generation solid-state lithium-metal battery technology, and Murata Manufacturing Co. have entered into the first phase of an agreement to explore a collaboration for high-volume manufacturing of ceramic film for QS’s solid-state battery technology.