-
- News
- Books
Featured Books
- smt007 Magazine
Latest Issues
Current IssueIntelligent Test and Inspection
Are you ready to explore the cutting-edge advancements shaping the electronics manufacturing industry? The May 2025 issue of SMT007 Magazine is packed with insights, innovations, and expert perspectives that you won’t want to miss.
Do You Have X-ray Vision?
Has X-ray’s time finally come in electronics manufacturing? Join us in this issue of SMT007 Magazine, where we answer this question and others to bring more efficiency to your bottom line.
IPC APEX EXPO 2025: A Preview
It’s that time again. If you’re going to Anaheim for IPC APEX EXPO 2025, we’ll see you there. In the meantime, consider this issue of SMT007 Magazine to be your golden ticket to planning the show.
- Articles
- Columns
Search Console
- Links
- Media kit
||| MENU - smt007 Magazine
Is Your Electronics Manufacturing Factory 'Smart'?
September 15, 2016 | Neil Sharp, JJS ManufacturingEstimated reading time: 8 minutes
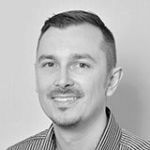
Not many people know the answer and, if we are honest, a large number of electronics manufacturing companies still don't fully understand this question. This is surprising given the amount of content being produced around "big data", Industry 4.0, digital manufacturing, mass customization and various other subjects.
So what exactly is a "smart" factory and should you care? And, if you do care, how do you go about assessing your own operation in order to make it smart(er)? In this article, we look to answer these questions and provide guidance on how you can assess your manufacturing facility without investing huge amounts of time and money upfront.
What is a smart factory?
Put simply, a smart factory contains a mix of hardware and software solutions, which work seamlessly together to improve results. The hardware – i.e. machines used to produce goods – are fitted with an array of sensors that capture huge amounts of data – often referred to as "big". Software solutions then analyze this data, in real time, enabling the factory to make a series of informed decisions. Of course, when we say "the factory" we really mean the other connected machines, which is where the smart element comes in.
Enhanced machine to machine (M2M) communication enables a higher level of automation, along with self-optimization and self-configuration. The vision, therefore, is that factories will be able to produce higher quality goods much more efficiently. Machines will be able to monitor and self-diagnose performance issues, even ordering replacement parts before failures occur, preventing machine down-time, a current efficiency killer for any electronics manufacturer. And finally, a smart factory will allow manufacturers to build and deliver highly customized products on a mass scale, processed far more efficiently than ever before, all at a reduced cost of course.
Why should I care if my factory is smart?
The degree to which you care will largely depend on the demands of your customers. Has their behavior changed over the past five years? Are they pressing you to deliver innovative new products at a reduced price within a shorter time frame? Are you seeing a shift towards greater personalization requirements? And more importantly how are your competitors responding to some of these new challenges – do you know?
With Industry 4.0 continuing to dominate manufacturing headlines, it's difficult to ignore the subject altogether. Of course, you may end up deciding it isn't relevant to you – the latest buzzword that will never amount to anything tangible. Alternatively, you may believe this newfound disruption could benefit your business and enhance the goods and services you offer customers if you act now. Regardless of where you stand on the matter today, it’s probably worth caring just a little while longer, even if it’s just to prove you were right all along.
How can I make my factory smart(er)?
The best approach is to tackle the subject head-on and I’d recommend you do this in a number of different ways:
- Read and digest – As mentioned earlier, the amount of content around these topics is overwhelming. To help give yourself a good grounding in the subject I would recommend reading through Barclays' "Future-proofing UK manufacturing" report, taking a look at the "digital compass" McKinsey & Company have produced, and then completing the "digital capability assessment" questionnaire provided by Accenture. Although these three resources are likely to throw up even more questions, they certainly help to highlight which areas of your business could be impacted by the next "revolution".
- Meet the experts – In addition to carrying out your own research, I would recommend talking to automation and robotics suppliers and visiting one or more of the exhibitions around the UK where you can see the technology in action. At Subcon 2016, Mike Wilson, general industry sales manager for ABB, delivered a compelling presentation regarding the growth potential collaborative robots (cobots) can offer to SMEs. Earlier in the year, a number of suppliers, including Rethink Robotics and Applied Automation, exhibited within the robotics demo zone at Drives & Controls 2016. These demonstrations really help visitors to the show visualize how advancements in technology can help to improve efficiency in the workplace. If you didn’t manage to get to either of these shows don’t worry. PPMA Total and Northern Manufacturing and Electronics 2016 are due to take place in the UK at the end of September 2016 with a number of robotic suppliers confirmed to attend. And of course, there is the Smart Factory Expo hosted by The Manufacturer taking place in early November 2016 – a show not to be missed if you are seriously considering your options.
- Ask for support - facilities like the Manufacturing Technology Centre (MTC) in Coventry develop and prove innovative manufacturing processes and technologies in partnership with industry, academia and other institutions. Whether you are unsure where to start, or have a specific project in mind, the MTC can probably help with varying levels of professional consultancy. Typically, this would consist of an in-house process review, assessment of the impact automation would have on your business, the provision of cost models and then advising on the full scope of automation options.
Once you have a clearer understanding of the solutions available, and have seen first-hand how similar tasks and processes to your own can be completed using automation, it’s time to walk your own factory floor. Pay close attention to the day-to-day tasks that are being carried out, especially the 3D ones, which are usually classified as:
- Dull
- Dangerous
- Dirty
Try not to dismiss any idea due to the amount of investment it may require or the lack of third party support available to you in turning these ideas into reality. The key is to think big and ignore boundaries (for the time being) – otherwise, you will stifle this critical brainstorming session.
Make sure you spend time in every department. It might be tempting to head straight over to the production line but chances are there will be a number of tasks carried out in areas such as Goods Inwards and Dispatch that could also benefit from a greater use of automation.
Document every task you feel could be improved and your list of "smart" opportunities should start to build up nicely. However, if you are struggling to spot suitable tasks, or simply want a head start, here are some to get you going:
Incoming materials – How are they currently tracked when en route from suppliers? Would an improvement in material visibility benefit your production planning?
Production requirements – How do you physically transfer material to the production line? Is stock manually processed and delivered to your operators? Are there any elements that could be automated? Which 3D tasks could be removed or reduced through a software or hardware solution?
Component preparation – Could tasks, such as device cropping, taping and reeling, pre-forming, programming, oven baking, dry storing or the application of serial number labels, benefit from being automated? What would you save and how would this make you more efficient?
Page 1 of 2
Suggested Items
Real Time with... IPC APEX EXPO 2025: Aster—Enhancing Design for Effective Testing Strategies
04/18/2025 | Real Time with...IPC APEX EXPOWill Webb, technical director at Aster, stresses the importance of testability in design, emphasizing early engagement to identify testing issues. This discussion covers the integration of testing with Industry 4.0, the need for good test coverage, and adherence to industry standards. Innovations like boundary scan testing and new tools for cluster testing are introduced, highlighting advancements in optimizing testing workflows and collaboration with other tools.
Real Time with… IPC APEX EXPO 2025: Schmoll America Showcasing Four Advanced Machines
03/05/2025 | Real Time with...IPC APEX EXPOIn an expansive booth, Schmoll America is showcasing three advanced Schmoll machines and one from Impex, its partner company. Kurt emphasizes Schmoll's commitment to growth and excellence as Schmoll America approaches its first anniversary. Stop by booth 4123 to see the action.
Smart Factory Insights: The Costs of Legacy Thinking
12/01/2021 | Michael Ford -- Column: Smart Factory InsightsAs humans, we learn facts, gain impressions, create solutions, put practices into place, and move onto our next challenge. Over time, our intent is to create a legacy of value, but in many cases, we are creating legacies in a different sense. Our knowledge, experience, and creations age or become superseded, but there is resistance to replace or update. An increasing gap develops between perception and reality. Younger, more agile peers take advantage, get ahead, and we look away, thinking that they don’t know what they are doing. Though a natural human phenomenon, decision-makers in manufacturing today need to bear this mind more than ever.
Managing Cyber-Threats Within Electronics Manufacturing
11/16/2018 | Neil Sharp, JJS ManufacturingThe rise of the 4th Industrial Revolution (4IR) has brought with it digital interconnectivity that offers unprecedented opportunities for original equipment manufacturers (OEMs). But with that openness there also comes risk—the threat of the loss of data, the theft of capital or intellectual property, and the disruption of access to systems or operational technology—all of which can impede businesses and impact on trade.
IoT: Driving Change in Manufacturing
10/15/2018 | Stephen Las Marias, I-Connect007In the manufacturing world, the Internet of Things (IoT) can be seen as an element of Industry 4.0. The idea behind it is that factories would evolve to become smarter, to become a lot more flexible—to be able to make the products that customers want, basically at any time that they need.