-
- News
- Books
Featured Books
- pcb007 Magazine
Latest Issues
Current IssueVoices of the Industry
We take the pulse of the PCB industry by sharing insights from leading fabricators and suppliers in this month's issue. We've gathered their thoughts on the new U.S. administration, spending, the war in Ukraine, and their most pressing needs. It’s an eye-opening and enlightening look behind the curtain.
The Essential Guide to Surface Finishes
We go back to basics this month with a recount of a little history, and look forward to addressing the many challenges that high density, high frequency, adhesion, SI, and corrosion concerns for harsh environments bring to the fore. We compare and contrast surface finishes by type and application, take a hard look at the many iterations of gold plating, and address palladium as a surface finish.
It's Show Time!
In this month’s issue of PCB007 Magazine we reimagine the possibilities featuring stories all about IPC APEX EXPO 2025—covering what to look forward to, and what you don’t want to miss.
- Articles
- Columns
Search Console
- Links
- Media kit
||| MENU - pcb007 Magazine
Estimated reading time: 3 minutes
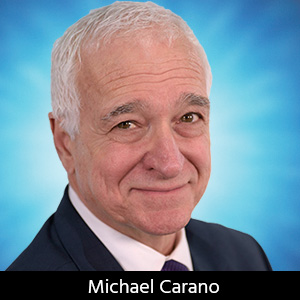
Contact Columnist Form
Trouble in Your Tank: Via Formation and Mechanical Drilling, Part 2
Introduction
In November’s column, I articulated the need to provide a quality drilled hole. I stated that a less than optimum mechanically drilled PTH will negatively impact the metallization processes as well as potentially affect the quality of the wave soldering of the PWB. In this month’s installment of Trouble in Your Tank, I will further explore the critical drilling parameters required to drill a “good hole” and provide information on some little-known parameters required for this operation.
What is a “good hole?”
A good hole is one that has a uniform and smooth sidewall, with no defects outside the tolerances defined by applicable specifications such as: smear, burrs, nail heading, debris, glass fibers, foreign material inclusion, etc. A good hole is drilled accurately with respect to size and location within the specified tolerances, and a hole wall perpendicular to the surface of the PCB. Deep drill gouges, torn-out glass bundles and the potential to create wedge voids severely impact the metallization process. When drilling is not optimized, many defects can and will occur. Unfortunately, if not recognized and corrected early in the PCB fabrication process, these drillinginduced defects may go undetected until the finished PCB has been sent to the assembly process! This is not a scenario you want to deal with.
Drilling-Induced
Defects One example that has many possible causes is the wedge void or wedging (Figure 1). One must be able to think about the entire fabrication process if wedge void is detected. A weak bond between the resin and copper, along with incomplete cure of the resin are two possible causes. However, excessive heat generated by the drilling process will also contribute. Generally, dull drill bits, excessive in-feed rates, and slow up-feeds contribute to the possibility for wedge voiding or wedging to occur.
Table 1 provides a concise overview with the causes and corrective actions when wedge voiding or wedging is occurring. As one further studies Figure 1, the plating fold is evident due to the wedge creation. Thus, even if this finished circuit board passes in circuit test (ICT), there exists the real possibility that the thin plated copper will fail during thermal cycling or while in service. Secondly, the thin copper in the fold area will often rupture during wave soldering, allowing gas to escape. This in turn will lead to blowholes.
Another defect that is drilling induced is “plowing.” This defect is characterized by furrows or grooves in the hole wall (Figure 2). Plowing is mainly caused by worn-out drill bit cutting edges, undercured laminate and excessive spindle speeds. Spindle speed is measured in RPMs. Therefore, check the spindle speed for that particular hole size and board thickness and adjust accordingly. The higher the RPM rate and the longer the drill bit stays in the hole, the more heat is generated. So, resin smear will also be an issue. If undercured resin material is the root cause, this issue resides within the lamination cycle, age of the pre-preg, moisture content and final cure temperatures.
Some Things to be Aware of
While engineers mostly focus the attention on drilling parameters such as feeds and speeds, there are other less obvious criteria that when not understood or maintained, will lead to poor hole wall drill quality. One such issue is spindle run-out. Runout or runout is an inaccuracy of the drill spindle. In this case, the drill tool or shaft does not rotate exactly in line with the main axis. For example, when drilling, run-out will result in a larger hole than the drill’s nominal diameter due to the drill being rotated eccentrically (off axis instead of in line) as opposed to concentrically (rotating in a very tight spiral). Excessive spindle run-out will cause the hole size to be larger than specified, lead to rifling in the hole wall and cause overall hole roughness. Rifling is a defect characterized by a groove or ridge in the hole wall. In general, when spindle run-out is affecting hole wall quality, the remedy is to clean out the spindle collet or replace the collet altogether.
Summary
It must be clear by now that there is more to drilling good holes than feeds and speeds. If anything, the information presented here underscores the difficult nature of troubleshooting and getting to the root cause of defects. Defects such as wedge voids and plowing may also have additional contributing factors such as under-cured laminate, poor lamination practices and moisture in the pre-preg.
Michael Carano is VP of technology and business development at RBP Chemical Technology. To read past columns or to contact Carano, click here.
Editor's Note: This column originally appeared in the December 2016 issue of The PCB Magazine.
More Columns from Trouble in Your Tank
Trouble in Your Tank: Causes of Plating Voids, Pre-electroless CopperTrouble in Your Tank: Organic Addition Agents in Electrolytic Copper Plating
Trouble in Your Tank: Interconnect Defect—The Three Degrees of Separation
Trouble in Your Tank: Things You Can Do for Better Wet Process Control
Trouble in Your Tank: Processes to Support IC Substrates and Advanced Packaging, Part 5
Trouble in Your Tank: Materials for PWB Fabrication—Drillability and Metallization
Trouble in Your Tank: Supporting IC Substrates and Advanced Packaging, Part 5
Trouble in Your Tank: Electrodeposition of Copper, Part 6