-
-
News
News Highlights
- Books
Featured Books
- smt007 Magazine
Latest Issues
Current IssueWhat's Your Sweet Spot?
Are you in a niche that’s growing or shrinking? Is it time to reassess and refocus? We spotlight companies thriving by redefining or reinforcing their niche. What are their insights?
Moving Forward With Confidence
In this issue, we focus on sales and quoting, workforce training, new IPC leadership in the U.S. and Canada, the effects of tariffs, CFX standards, and much more—all designed to provide perspective as you move through the cloud bank of today's shifting economic market.
Intelligent Test and Inspection
Are you ready to explore the cutting-edge advancements shaping the electronics manufacturing industry? The May 2025 issue of SMT007 Magazine is packed with insights, innovations, and expert perspectives that you won’t want to miss.
- Articles
- Columns
- Links
- Media kit
||| MENU - smt007 Magazine
The Benefits of Applying Flux Directly to a Micro BGA
May 12, 2017 | Richard Barratt, JJS ManufacturingEstimated reading time: 5 minutes
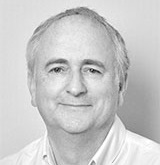
Technology trends continue to drive miniaturization in electronic components. As a result, product designers are often forced into specifying smaller and smaller devices on their bill of materials (BOM). Sometimes, miniature devices offer original equipment manufacturers (OEMs) cost savings, which is seen as a good thing; other times, there is simply no choice.
Component manufacturers continue to make devices obsolete in an attempt to release new technologies to market and keep up with consumer trends. This can be a problem for OEMs that have "old" versions of the part designed into their industrial hardware, as they may have to go through a redesign process.
Product designers are not always aware of the challenges redesigning their products to include miniature devices can cause. You could argue there is a disconnect between design and the manufacturing process. While electrically the new device may be fine, if it is located next to a much larger device then the electronics manufacturer may need to modify their build process and conduct additional trials to satisfy themselves they can consistently manufacture the product. All of which takes additional time and, in some cases, requires specialist equipment and tooling.
In this article, we share with you a case study featuring a printed circuit board assembly (PCBA) with a micro ball grid array (BGA) located next to a SIM card holder. We walk you through the process steps we took to ensure a consistent solder joint was made and share with you the results of the trials we conducted.
Unfortunately, we can’t tell you who the customer is. As with all our customers, we have a confidentially agreement in place but we can tell you they are a global security services company. We also can’t tell you much about the product either, sorry. But we can tell you that the PCBA is doubled sided, 8 up on a panel and includes a 0.4" pitch micro BGA (measuring 2.7mm x 2.4mm) located next to a SIM card reader measuring 26mm x 20mm, which is quite a difference.
Multi-level solder stencil
This presented us with a challenge. The micro BGA would require a solder paste height of 0.08mm compared to the SIM card reader that would need 0.125mm. The conventional way to approach this particular challenge and achieve varying solder paste heights is to specify a multi-level solder stencil. There are two common techniques (stepped and additive) in creating multi-level stencils, and if you would like to read more about the pros and cons of each, we recently wrote an article covering this topic.
Unfortunately, after using a stepped stencil we identified solder shorts and an approximate 25 percent failure rate on the micro BGA.
Left image: BGA with shorts. Right image: BGA without shorts.
Although we felt it possible to make further improvements to the stencil material and design (change to electro-formed nickel with a reduced solder deposit and nano coating), we wanted to minimize the risk of shorts completely and decided to look into applying flux to the micro BGA directly.
Direct flux application
We trialed Mycronic's dip unit as it attached to our pick and place surface mount equipment. The unit consists of a squeegee and flux transfer plate, which has several cavities at different depths cut into it. Flux is dispensed and the squeegee then wipes it across the cavities leaving them filled, after which the micro BGA is picked and dipped directly into them.
During our trials, we built two panels consisting of 16 micro BGAs in total. We trialed two different flux depths and ran one panel with 0.1mm and the other with 0.14mm, with the aim of covering at least 50 per cent of the ball height (0.2mm) with flux. Too much flux can result in the part sticking in the cavity. There is also a danger that when it reflows the gaps between the balls become filled with flux residue which can be a problem if you need to make the joint stronger by underfilling with resin.
After the devices had been fitted to the board and reflowed, we re-inspected the boards to look for potential issues.
The results
We inspected the panels using X-ray, no shorts were found and we saw good placement. Although X-ray images can provide confidence and offer a good level of detail, we always recommend several inspection methods when validating results.
Page 1 of 2
Suggested Items
Silicon Mountain Contract Services Enhances SMT Capabilities with New HELLER Reflow Oven
07/17/2025 | Silicon Mountain Contract ServicesSilicon Mountain Contract Services, a leading provider of custom electronics manufacturing solutions, is proud to announce a significant upgrade to its SMT production capability with the addition of a HELLER 2043 MK5 10‑zone reflow oven to its Nampa facility.
Knocking Down the Bone Pile: Addressing End-of-life Component Solderability Issues, Part 4
07/16/2025 | Nash Bell -- Column: Knocking Down the Bone PileIn 1983, the Department of Defense identified that over 40% of military electronic system failures in the field were electrical, with approximately 50% attributed to poor solder connections. Investigations revealed that plated finishes, typically nickel or tin, were porous and non-intermetallic.
SHENMAO Strengthens Semiconductor Capabilities with Acquisition of PMTC
07/10/2025 | SHENMAOSHENMAO America, Inc. has announced the acquisition of Profound Material Technology Co., Ltd. (PMTC), a premier Taiwan-based manufacturer of high-performance solder balls for semiconductor packaging.
KYZEN to Highlight Understencil and PCB Cleaners at SMTA Querétaro Expo and Tech Forum
07/09/2025 | KYZEN'KYZEN, the global leader in innovative environmentally responsible cleaning chemistries, will exhibit at the SMTA Querétaro Expo & Tech Forum, scheduled to take place Thursday, July 24, at Centro de Congresos y Teatro Metropolitano de Querétaro.
Driving Innovation: Direct Imaging vs. Conventional Exposure
07/01/2025 | Simon Khesin -- Column: Driving InnovationMy first camera used Kodak film. I even experimented with developing photos in the bathroom, though I usually dropped the film off at a Kodak center and received the prints two weeks later, only to discover that some images were out of focus or poorly framed. Today, every smartphone contains a high-quality camera capable of producing stunning images instantly.