-
- News
- Books
Featured Books
- design007 Magazine
Latest Issues
Current IssueProper Floor Planning
Floor planning decisions can make or break performance, manufacturability, and timelines. This month’s contributors weigh in with their best practices for proper floor planning and specific strategies to get it right.
Showing Some Constraint
A strong design constraint strategy carefully balances a wide range of electrical and manufacturing trade-offs. This month, we explore the key requirements, common challenges, and best practices behind building an effective constraint strategy.
All About That Route
Most designers favor manual routing, but today's interactive autorouters may be changing designers' minds by allowing users more direct control. In this issue, our expert contributors discuss a variety of manual and autorouting strategies.
- Articles
- Columns
- Links
- Media kit
||| MENU - design007 Magazine
A Deep Look Into Embedded Technology
July 4, 2017 | Barry Matties and Patty Goldman, I-Connect007Estimated reading time: 2 minutes
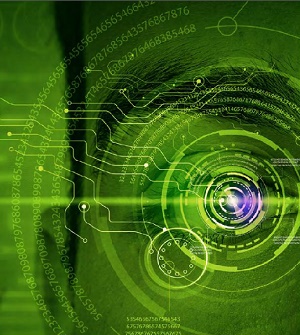
In preparation for this month’s magazine, we set up a conference call with the goal of uncovering the challenges and opportunities related to embedded technology. Invited were a handful of the industry’s heavy hitters in the embedded world: Retired technologist and I-Connect007 Contributing Editor Happy Holden, and Ohmega’s Technical Director Daniel Brandler and Design & Test Engineer Manuel Herrera. This informative, comprehensive discussion focuses on the state of embedded materials and components, today and into the future, as well as a variety of promising processes.
Patty Goldman: Gentlemen, thanks for joining us. Some of the things we want to learn are: What’s going on? What’s the latest? Additionally, what are some of the things that you think that your customers want to know? Dan, Ohmega Technology has been doing embedded components for over 30 years. Can you provide an overview of that work?
Dan Brandler: Ohmega Technology primarily makes materials used in embedding resistors, planar resistors, even surface resistors under the solder mask, but mostly it’s a multilayer structure. We electrically deposit a nickel-phosphorous alloy, which is the resistor material. It’s been around since World War II, so it’s a very well established material. We electrically deposit on standard ED copper foil of different levels of roughness, which will be discussed later in the conversation, and we supply that material to either laminators for PCB or microwave applications or to board shops who make their own laminate and PCBs with the embedded resistors.
In some cases, we subcontract laminates out to companies. But our primary business is just applying the resistive copper foil and we’ve been doing that for a long time. We’re not the only ones doing it; there are other alloys out there like Nichrome, but we’re the oldest. About 30−40% of our business is aerospace defense, things like power dividers, microwave applications for satellites, phased array antennas, and microwave absorbers. That didn’t used to be the case, but the majority now for commercial use is mainly for sensor technology, particularly in cell phones. I would guess almost all of you or at least certainly half of you I’m speaking to right now will probably have cellphones with you with our resistors in it. Our resistor material is in the largest American cellphone manufacturer’s products.
To read the full version of this interview which appeared in the June 2017 issue of The PCB Magazine, click here.
Testimonial
"In a year when every marketing dollar mattered, I chose to keep I-Connect007 in our 2025 plan. Their commitment to high-quality, insightful content aligns with Koh Young’s values and helps readers navigate a changing industry. "
Brent Fischthal - Koh YoungSuggested Items
BEST Inc. Provides High-Reliability BGA Reballing and Component Rework Services
08/22/2025 | BEST Inc.BEST Inc., a leader in electronic component services, is pleased to announce its component rework services are available for all types of area array devices including ball grid array, land grid array and quad flat no-lead SMT packages.
Indium Corporation Promotes Two Leaders in EMEA (Europe, Middle East, and Africa) Markets
08/05/2025 | Indium CorporationWith its commitment to innovation and growth through employee development, Indium Corporation today announced the promotions of Andy Seager to Associate Director, Continental Sales (EMEA), and Karthik Vijay to Senior Technical Manager (EMEA). These advancements reflect their contributions to the company’s continued innovative efforts with customers across Europe, the Middle East, and Africa (EMEA).
MacDermid Alpha Electronics Solutions Unveils Unified Global Website to Deepen Customer, Talent, and Stakeholder Engagement
07/31/2025 | MacDermid Alpha Electronics SolutionsMacDermid Alpha Electronics Solutions, the electronics business of Elements Solutions Inc, today launched macdermidalpha.com - a unified global website built to deepen digital engagement. The launch marks a significant milestone in the business’ ongoing commitment to delivering more meaningful, interactive, and impactful experiences for its customers, talent, and stakeholders worldwide.
KOKI to Showcase Analytical Services and New HF1200 Solder Paste at SMTA Guadalajara 2025
07/31/2025 | KOKIKOKI, a global leader in advanced soldering materials and process optimization services, will exhibit at the SMTA Guadalajara Expo & Tech Forum, taking place September 17 & 18, 2025 at Expo Guadalajara, Salón Jalisco Halls D & E in Guadalajara, Mexico.
Weller Tools Supports Future Talent with Exclusive Donation to SMTA Michigan Student Soldering Competition
07/23/2025 | Weller ToolsWeller Tools, the industry leader in hand soldering solutions, is proud to announce its support of the upcoming SMTA Michigan Expo & Tech Forum by donating a limited-edition 80th Anniversary Black Soldering Set to the event’s student soldering competition.