-
- News
- Books
Featured Books
- smt007 Magazine
Latest Issues
Current IssueThe Path Ahead
What are you paying the most attention to as we enter 2025? Find out what we learned when we asked that question. Join us as we explore five main themes in the new year.
Soldering Technologies
Soldering is the heartbeat of assembly, and new developments are taking place to match the rest of the innovation in electronics. There are tried-and-true technologies for soldering. But new challenges in packaging, materials, and sustainability may be putting this key step in flux.
The Rise of Data
Analytics is a given in this industry, but the threshold is changing. If you think you're too small to invest in analytics, you may need to reconsider. So how do you do analytics better? What are the new tools, and how do you get started?
- Articles
- Columns
Search Console
- Links
- Media kit
||| MENU - smt007 Magazine
Rework and Reball Challenges for Wafer Level Packages
October 16, 2017 | Lauren Cummings and Priyanka Dobriyal, Ph.D., Intel Corp.Estimated reading time: 6 minutes
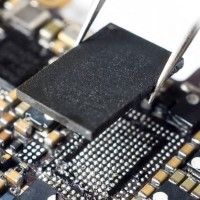
There is a growing consumer demand for smart wearable products, including watches, fitness bands, eyewear, and headphones. Barriers to the market still exist, as many consumers are concerned with style, battery life, functionality, and cost. The mature smartphone market faces similar challenges, with consumers desiring thinner phones with longer battery life and increased sensor functionality. High-density and stacked PCB designs, system in package (SiP) assemblies, and small form factor packages have all emerged as solutions for sleeker styles and improved functionality. In particular, WLPs are gaining popularity for their low cost, small footprint, and thin profile. The newest smartphone models contain an average of 5-7 WLPs, with many WLPs used as RF transceivers, power management units, audio amplifiers, and BlueTooth and GPS modules.
Figure 1: Cross-section schematics of (a) a traditional fan-in wafer level package, and (b) a newer fan-out wafer level package.
Unlike traditional packages, WLPs are packaged and bumped first, then diced. Passivation and dielectric layers are added to the die frontside, followed by metallic redistribution layers. A second dielectric layer is deposited, then the underbump metallization and solder balls are attached. Lastly, the packages are singulated from the wafer. Figure 1 illustrates the two different categories of WLPs: the traditional a) fan-in WLP, and the newer b) fan-out WLP. The dielectric is exposed on the edges and frontside of fan-in WLPs, while the silicon backside is often covered with a protection tape. As the name suggests, fan-out WLPs “fan out” interconnects from the smaller silicon die to the larger package dimensions. The fan-out design allows for ball pitch customization, higher I/O density, and easy integration with SiPs and other multidie packages. The board-level reliability is also improved by protecting the silicon die with an epoxy mold compound.
Though WLPs offer considerable advantages, they also pose challenges for failure analysis—particularly when reball and component-level testing are required. Figure 2 illustrates the typical FA process flow for a failing system, such as a mobile phone, tablet, or wearable device.
Figure 2: Diagram showing the typical process flow for system-level failure analysis
Fault isolation is performed first to identify the failing component, then nondestructive FA is used to inspect for failures at both the board- and package-level. If the failure is subtle or cannot be found non-destructively, the package must be reworked and reballed before proceeding with socketed component-level testing and further FA. Due to their small form factor and fragility, WLPs can prove particularly difficult for the rework and reball process steps. The present work provides an overview of the FA process flow, emphasizing component rework and reball methodologies. The challenges of a specific WLP case study are discussed, and rework and reball improvements are implemented to minimize thermally- or mechanically-induced artifacts.
Fault isolation is an important first step in the system-level FA process. By isolating the failure to a specific package or interconnect, an optimal FA approach can be assessed and throughput time can be greatly reduced. Several fault isolation techniques can be used to measure for opens and shorts, including hand probing, time domain reflectometry and the newer electro optic terahertz pulse reflectometry. High-resistance shorts can also be detected by powering the board and measuring the localized temperature increase using infrared thermal imaging techniques.
After the failing component has been isolated, nondestructive FA is performed to inspect for gross board- or package-level failures. OM can be used to inspect for external board or package defects, such as foreign materials or superficial die and overmold cracks. Since WLPs have exposed dielectric layers (and since fan-in WLPs have exposed bulk Si), it is especially important to perform a first pass inspection for external chips or cracks. It is recommended that optical inspection be performed again after rework and reball, to confirm that no artifacts were introduced.
CSAM, a popular non-destructive technique, can be utilized to detect internal defects or to evaluate the extent of external damage. CSAM uses an ultrasound transducer to raster-scan the package backside. At material interfaces, an acoustic pulse is reflected to the transducer and recorded as signal amplitude. Air-solid interfaces occur at the locations of cracks, voids, or delamination, and return high-intensity reflections. CSAM is thus a valuable metrology for identifying gross internal package defects that cannot be detected with simple optical inspection. CSAM can also be used to screen for rework and reball artifacts, particularly thermally- induced delamination.
2D X-ray is another common technique that provides an effective “quick pass” inspection for board-level solder defects, such as voids and bridging. By optimizing the sample tilt and rotation angles, subtler non-wet open and noncontact open defects can also be detected. However, 2D X-ray is not capable of detecting submicron defects, such as board-level solder or via cracks.
Recently, more advanced imaging metrologies have emerged as powerful non-destructive FA techniques. In particular, 3D X-ray computed tomography has proven effective at detecting both board-level and package-level sub-micron defects. Multiple 2D X-ray images are collected as the sample is rotated at fixed angle increments. The 2D X-ray images are then superimposed to generate a three-dimensional volume. The superimposed image can be manipulated to display virtual “slices” of the sample, allowing for inspection of the solder joints, via barrels, and traces.
If board-level or gross package-level failures are not detected using non-destructive techniques, the package must be sent for socketed component-level testing and further FA. Standard test sockets use a spring-loaded floating base that is guided by the solder balls instead of the package edge. Reball is thus required to align the package and enable good electrical contact with each pin. It is very important to preserve the defect signature prior to testing; accordingly, precautions must be taken to improve the reball yield and reduce thermal and mechanical artifacts.
Page 1 of 2
Suggested Items
AIM Solder Promotes Kelly Cardone to Vice President, Customer Experience
01/21/2025 | AIMAIM Solder, a global leader in solder assembly materials for the electronics industry, is thrilled to announce the promotion of Kelly Cardone to Vice President, Customer Experience. This promotion highlights AIM’s commitment to offering superior support and customer experience.
Indium to Showcase Durafuse Solder Technology at NEPCON Japan
01/21/2025 | Indium CorporationAs one of the leading materials providers in the electronics assembly industry, Indium Corporation® is looking forward to featuring its innovative Durafuse® solder technology at NEPCON Japan, taking place January 22-24, in Tokyo, Japan.
Peters Leverages Inkjet Technology to Optimize PCB Manufacturing
01/17/2025 | PetersPeters has put the second SUSS LP50 ‘Pixdro’ inkjet printer into operation. This machine enables the application of solder resist in digital additive technology by means of the inkjet process, thus providing Peters Research, in this relatively new segment, with more possibilities in research and process technology, in addition to the conventional coating processes (screen printing, curtain coating and spray coating).
TopLine’s Martin Hart to Present at Microelectronics Reliability and Qualification Workshop (MRQW)
01/16/2025 | TopLine CorporationTopLine Corporation’s Founder and CEO Martin Hart has been invited to deliver a presentation on the topic of how “Braided Solder Columns reduce mechanical stress in large heterogeneous 2.5D advanced packages for space and commercial applications” at The Aerospace Corporation’s Microelectronics Reliability and Qualification Workshop (MRQW) in Los Angeles (El Segundo), California on February 12, 2025.
AIM to Highlight NC259FPA Ultrafine No Clean Solder Paste at SMTA Austin Expo & Tech Forum
01/16/2025 | AIMAIM Solder, a leading global manufacturer of solder assembly materials for the electronics industry, is pleased to announce its participation in the upcoming SMTA Austin Expo & Tech Forum taking place on February 6 at the Travis County Exposition Center in Austin, Texas.