-
- News
- Books
Featured Books
- pcb007 Magazine
Latest Issues
Current IssueInventing the Future with SEL
Two years after launching its state-of-the-art PCB facility, SEL shares lessons in vision, execution, and innovation, plus insights from industry icons and technology leaders shaping the future of PCB fabrication.
Sales: From Pitch to PO
From the first cold call to finally receiving that first purchase order, the July PCB007 Magazine breaks down some critical parts of the sales stack. To up your sales game, read on!
The Hole Truth: Via Integrity in an HDI World
From the drilled hole to registration across multiple sequential lamination cycles, to the quality of your copper plating, via reliability in an HDI world is becoming an ever-greater challenge. This month we look at “The Hole Truth,” from creating the “perfect” via to how you can assure via quality and reliability, the first time, every time.
- Articles
- Columns
- Links
- Media kit
||| MENU - pcb007 Magazine
Better to Light a Candle: Chapter One—Prepping the Next Generation
January 8, 2019 | Marc Carter, Independent ContributorEstimated reading time: 8 minutes
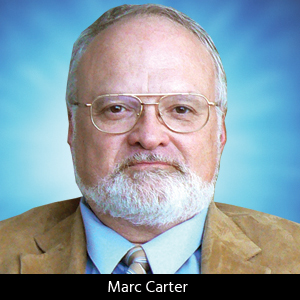
Editor’s Note: This is the first in a series of columns on a new university course in PCB manufacturing at Michigan Technological University. Marc will chronicle the progress of this class, interview the guest lecturers, introduce the students, etc.
There has been a considerable amount of (electronic) ink and words shared in our industry bemoaning the graying-out of our industry and the growing shortage of skilled people at all levels. (See the May 2017 PCB007 Magazine column “Help Wanted—and How!” for just one example). As is usually the case, though, when all is said and done, more has been said than done.
That is why it was so refreshing to learn of someone who has decided to do something about it. Enter Dr. Christopher Middlebrook, a professor at Michigan Technological University (MTU) in Houghton, Michigan. On January 14, 2019, he will open the first session of “EE4800: Printed Circuit Board Fabrication”—a hands-on engineering class intended to give undergraduate students an introduction to the basics of printed circuit design, fabrication, and assembly. Here’s an abridged excerpt of the course description:
“Printed circuit board fabrication techniques are presented and explored utilizing wet-chemical process techniques. Single and multilayer boards using internal layers for power and ground planes as well as plated feed-through via structures, solder masks, and silk screens will be discussed. While hands-on fabrication will be the main focus, students will be introduced to software design packages specific to circuit layout and design. Final testing and evaluation of the fabricated boards will be performed.”
I have had the pleasure of working with Dr. Middlebrook along with a growing number of other well-seasoned PCB professionals who share a concern about our ability to sustain a viable printed circuit industry into the future here in North America. The equipment, materials, and processes available are very basic (and some show evidence of scrounging and “shoestring engineering”), but it all works. The class will allow each student to complete a multilayer PCB, using the same underlying processes used to build a conventional multilayer PCB in production from start to finish (Figure 1).
Figure 1: MTU’s equipment suite for their new course in PCB fabrication.
From one perspective, the students get a closer experience of the basic principles than they would be in a highly-automated or conveyorized operation. They will also gain some exposure to the more industrial and high-tech world due to the active involvement of nearby Calumet Electronics Corporation, with opportunities to see the larger-scale versions of the processes used in the class. The value of proximity to a highly supportive active printed circuit operation is a significant force multiplier in making this an effective experience for the students.
Much of the classroom input will come from guest lecturers (that same body of well-seasoned veterans) and companies volunteering their time and efforts. The common thread among them is that they can see the long-term benefits to the industry of this small initial effort, and can imagine others like it that may follow. Using this small class of 18 students as a starting point and demonstrating and debugging the concept, the prospect of expanding into more sophisticated design tools, advanced structures, and robust operations in future classes at MTU is realistic.
Dr. Christopher Middlebrook Interview
The following interview I did with Dr. Middlebrook may give you a little insight into the driver behind this effort.
Marc Carter: How did you start thinking about a class like this?
Dr. Chris Middlebrook: Feedback was received from the industry and DoD with regard to the lack of experience and exposure of prospective students in aspects of printed circuit design and fabrication, and I wanted to address this deficiency. In addition, as a result of a previous research product, we had pieces of the basic fabrication equipment available, and combining those with other older equipment from back in the day when we performed board manufacturing made it realizable. It also helps to have Calumet Electronics in our geographic location as a resource. One of MTU’s strengths is that we pride ourselves in being a technological university that educates and develops our student body to hit the ground running with hands-on experience when they start their careers, and printed circuits and electronics is a perfect match.
Carter: Was it hard to sell the value of this concept given that it has to compete for other MTU resources?
Middlebrook: Many areas in electrical engineering are hot and growing right now, and developing a new program that may compete for resources is certainly a challenge. MTU, being a relatively smaller university, allows itself to be more agile and attentive to industrial, DoD, and student needs. Connecting the areas—such as illustrating that cloud-based computing has to exist physically somewhere where hardware is utilized—shows the integration of a multidisciplinary approach to education. When I poll students, they are always excited about learning printed circuit fabrication and obtaining hands-on experience to understand the complete design, fabrication, testing, and implementation process. Having outside input from places such as Calumet Electronics, Plexus, and Gentex that hire our students has been critical.
Carter: Have you been surprised by the industry response?
Middlebrook: Beginning this program implementation, I knew we had the support of Calumet Electronics and other experts such as yourself, but I am continually amazed by the response and guidance from industry. We have been in discussions with several industry experts who have expressed great interest in not only advising on our specific fabrication processes but also contributing to guest lectures and seminars. Having this talent directly interact with students brings a larger global perspective to a typical university offered course.
Carter: What would help you make this course as effective as possible in this first iteration? What do you need right now?
Middlebrook: Continued guidance in the shaping of the course and soon-to-be-developed courses from subject matter experts is critical to ensure our students gain the necessary skills that employers are looking to fill. While we have some of the basic equipment in place to launch the course, we are always looking for companies and organizations that might be willing to donate or loan used equipment that is being replaced, underutilized, or upgraded. We strive to develop and align the program to the state-of-the-art techniques and equipment. From a student perspective, they may not necessarily have to have the latest and greatest equipment to understand basic printed circuit fabrication techniques.
Page 1 of 2
Testimonial
"Advertising in PCB007 Magazine has been a great way to showcase our bare board testers to the right audience. The I-Connect007 team makes the process smooth and professional. We’re proud to be featured in such a trusted publication."
Klaus Koziol - atgSuggested Items
Indium Promotes Huang to Senior Manager, Marketing Communications
08/28/2025 | Indium CorporationWith its commitment to innovation and growth through employee development, Indium Corporation announces the promotion of Jingya Huang to Senior Manager, Marketing Communications, to continue to lead the company’s branding and promotional efforts.
Rehm Academy Expands Its Training Program
08/28/2025 | Rehm Thermal SystemsThe demands on modern industrial companies and employees continue to rise, and therefore, the topic of further education is becoming increasingly important today.
MacDermid Alpha Awarded for Innovation: Driving Process Optimization and Efficiency with Major Indian EMS Provider
08/28/2025 | MacDermid Alpha Electronics SolutionsMacDermid Alpha Electronics Solutions, a leading global supplier of integrated materials for the electronics industry, is recognized by one of India’s top EMS providers, Syrma SGS, with an award for innovation that advanced process optimization, enhanced operational efficiency, and yield gains.
Integrated Solutions for Board-level Reliability: A Smarter Path Forward
08/27/2025 | Alan Gardner, MacDermid Alpha Electronics SolutionsIn today’s electronics manufacturing landscape, reliability is no longer just a benchmark but a business imperative. As industries such as automotive, aerospace, and high-performance computing (HPC) push the boundaries of innovation, the demand for dependable board-level performance under extreme conditions has never been greater.
ZESTRON Expands Capabilities with Addition of the EPS by i-Tech AG 75 Pallet Cleaning System
08/26/2025 | ZESTRONZESTRON, the global leader in high-precision cleaning solutions and services, is excited to announce the addition of a new capability in its Technical Center in Manassas, VA: