-
- News
- Books
Featured Books
- pcb007 Magazine
Latest Issues
Current IssueThe Hole Truth: Via Integrity in an HDI World
From the drilled hole to registration across multiple sequential lamination cycles, to the quality of your copper plating, via reliability in an HDI world is becoming an ever-greater challenge. This month we look at “The Hole Truth,” from creating the “perfect” via to how you can assure via quality and reliability, the first time, every time.
In Pursuit of Perfection: Defect Reduction
For bare PCB board fabrication, defect reduction is a critical aspect of a company's bottom line profitability. In this issue, we examine how imaging, etching, and plating processes can provide information and insight into reducing defects and increasing yields.
Voices of the Industry
We take the pulse of the PCB industry by sharing insights from leading fabricators and suppliers in this month's issue. We've gathered their thoughts on the new U.S. administration, spending, the war in Ukraine, and their most pressing needs. It’s an eye-opening and enlightening look behind the curtain.
- Articles
- Columns
- Links
- Media kit
||| MENU - pcb007 Magazine
The Institute of Circuit Technology Autumn Seminar
October 3, 2019 | Pete Starkey, I-Connect007Estimated reading time: 10 minutes
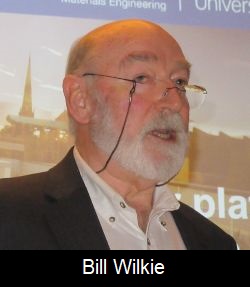
An ancient monument dating back more than 500 years stands proudly on the green in the village of Meriden with a plaque stating that, by tradition, it marks the centre of England. But more recently, GPS technology argues that the true geographical centre is 11 miles north! Either way, Meriden has been established as a popular Midlands venue for Institute of Circuit Technology (ICT) meetings. On September 19, a multitude of Fellows, Members, and Associates gathered for the Institute’s autumn seminar, which was organised and hosted by ICT Technical Director Bill Wilkie. The agenda included five informative technical presentations, describing current research and development on significant topics relevant to the industry.
Sophia Danilova, a Ph.D. student worker from the Research Centre for Manufacturing and Materials Engineering at Coventry University, discussed the importance of selective metallisation in the electronics sector. Her presentation titled entitled “Selective Electroless Copper Plating on a Non-Conductive Substrate Via Magnetic Field Application” included a discussion of PCBs, moulded interconnect devices, microelectronics, printed electronics, wearable technology, and radio-frequency identification devices.
It had been estimated that 30–40% of the total manufacturing cost of an electronic device was due to photolithography, a time-consuming, multi-step process with high material wastage due to coating the entire surface with photoresist before exposure and development to create a resist pattern. Patterning by magnetic field was being investigated as a lower-cost alternative with shorter processing time. The objective was to selectively deposit a catalyst and then to build the conductor pattern by electroless copper deposition.
The first step was to prepare a suitable magnetic catalyst. Initial attempts to combine silver and iron powders by ball-milling resulted in particle sizes that were too large for accurate patterning. Iron-palladium nano-particles supplied by the specialists at the Jožef Stefan Institute in Slovenia were found to be unsuitable for the application. Wet chemical synthesis of a composite of silver and iron oxide using arginine as reducing agent gave promising results, and wet chemical synthesis of a composite of silver with silica and iron oxide using tin as a reducing agent gave particles with a regular distribution of magnetic and catalytic sites.
The conditions for magnetic deposition of a catalyst had been optimised in terms of time and pH as determined by the uniformity of electroless copper coverage. Magnetic templates were designed using finite element method magnetics (FEMM) software for the simulation of magnetic field distribution. Copper patterns with micron-scale features had been successfully produced by electroless plating, and the research had progressed from idea to proof of concept. The main goal of future work was to selectively deposit copper in sub-micron patterns by creating mono-dispersed magnetic nanoparticles, continuing work on template modelling using 3D simulation software and the optimisation of catalyst and copper plating conditions.
Professor and ICT Chairman Andy Cobley from Coventry University gave a two-part presentation, including an update on the MATUROLIFE project in which the university was a partner and an introduction to the ReCollect project in which the Institute was a partner. The Horizon 2020 funded MATUROLIFE project was in its 20th month out of 36, and Cobley reported its progress in the areas of design, materials, electronics integration, and prototype manufacturing. The consortium of 20 partners from nine European countries brought a creative and artistic design together with materials science and electronic manufacturing to produce innovative assistive technology co-created with older adults across Europe to support independent ageing and well-being.
Fundamental to the concept of smart textiles was a practical metallisation process, and extensive work had been carried out to compare different catalysts for the electroless copper plating of polyester, nylon, and cotton fibres. A copper-nanoparticle formulation had given better results than standard colloidal palladium, based on the conductivity of the electroless deposit. By adding polyethylene glycol to adjust viscosity, an inkjet-printable version of this formulation had been produced which had been used to produce high-resolution images on fine polyester fabric. Various organic post-treatments were evaluated for the protection of conductive tracks against perspiration and repeated washing.
Cobley also showed examples of the integration of electronics by embedding smart textiles into a range of clothing, furniture, and footwear solutions. Concept prototypes had been manufactured, and opportunities for industrial scalability were explored. And in the second part of his presentation, Cobley introduced the ReCollect project funded by Innovate U.K., in which ICT had undertaken to support the stimulation and dissemination of U.K. industry feedback on the developments.
It had been estimated that the annual world demand for FR-4 glass-epoxy circuit boards was approaching 20 billion square metres, of which about 15% was single- and double-sided. It was not practical to salvage the fibreglass and epoxy-resin components at end of life. Generally, recycling was limited to shredding and incinerating to recover precious metals. The ReCollect project proposed an alternative route to managing end-of-life circuit boards by removing glass-epoxy materials from the supply chain and establishing an efficient manufacturing process for non-toxic, recyclable, composite laminates.
One of the project partners had already demonstrated the feasibility of reinforcing water-soluble materials with natural fibres to use as substrates for single- and double-sided PCBs. The primary aim of the project was to demonstrate the feasibility of producing this material in high volumes within the U.K. and show that it could match the performance of CEM 1 and FR-4. The secondary aim was to investigate means of chemically protecting the material from existing aqueous processes used in PCB manufacturing. Another of the project partners was developing a novel process for the continuous production of sheet material. The overall market opportunity was substantial, although there would inevitably be a need to overcome the expected inertia in transitioning from a long-standing existing technology.
Recognised for many years in the printed circuit industry for his outstanding contribution to science and technology—both academically and practically—as well as for his environmental awareness and commitment, Professor Martin Goosey drew delegates’ attention to the finite supply of key raw materials to the electronics industry. Particularly, he emphasised the scarcity of platinum-group metals (PGMs), the growing global demand, and the importance of recovering and recycling these materials to bridge the increasing gap between supply and demand.
Goosey had a long-standing interest in recovering materials from PCBs and waste electrical and electronic equipment (WEEE). Indeed, I remember him chairing the Environmental Working Group of the Printed Circuit Interconnection Federation, studying opportunities for PCB recycling over twenty years ago. More recently, changes in technology have been driving the demand for critical raw materials. Examples include the move from CRT towards LCD and OLED displays, the replacement of incandescent lighting with LED, the evolution of battery technology from nickel-cadmium through nickel-metal-hydride to lithium-ion, and the transition of vehicle propulsion systems from the internal combustion engine to battery power.
Europe had been estimated to have the highest annual demand of PGMs in the world—40 tonnes, worth over 1100 million Euros—and globally, there was currently an annual shortfall of about 20 tonnes between demand and what could be supplied from primary sources. And the shortfall was forecast to continue to grow. End-of-life recycling became even more relevant, especially considering that the concentration of PGMs could be at least 100 times greater in electronics wastes than in natural ores. The traditional method was to shred the waste and burn it; there was an urgent need to develop viable methods for recovering valuable materials at end of life.
Page 1 of 2
Suggested Items
SHENMAO Strengthens Semiconductor Capabilities with Acquisition of PMTC
07/10/2025 | SHENMAOSHENMAO America, Inc. has announced the acquisition of Profound Material Technology Co., Ltd. (PMTC), a premier Taiwan-based manufacturer of high-performance solder balls for semiconductor packaging.
KYZEN to Highlight Understencil and PCB Cleaners at SMTA Querétaro Expo and Tech Forum
07/09/2025 | KYZEN'KYZEN, the global leader in innovative environmentally responsible cleaning chemistries, will exhibit at the SMTA Querétaro Expo & Tech Forum, scheduled to take place Thursday, July 24, at Centro de Congresos y Teatro Metropolitano de Querétaro.
Driving Innovation: Direct Imaging vs. Conventional Exposure
07/01/2025 | Simon Khesin -- Column: Driving InnovationMy first camera used Kodak film. I even experimented with developing photos in the bathroom, though I usually dropped the film off at a Kodak center and received the prints two weeks later, only to discover that some images were out of focus or poorly framed. Today, every smartphone contains a high-quality camera capable of producing stunning images instantly.
Hands-On Demos Now Available for Apollo Seiko’s EF and AF Selective Soldering Lines
06/30/2025 | Apollo SeikoApollo Seiko, a leading innovator in soldering technology, is excited to spotlight its expanded lineup of EF and AF Series Selective Soldering Systems, now available for live demonstrations in its newly dedicated demo room.
Indium Corporation Expert to Present on Automotive and Industrial Solder Bonding Solutions at Global Electronics Association Workshop
06/26/2025 | IndiumIndium Corporation Principal Engineer, Advanced Materials, Andy Mackie, Ph.D., MSc, will deliver a technical presentation on innovative solder bonding solutions for automotive and industrial applications at the Global Electronics A