-
-
News
News Highlights
- Books
Featured Books
- design007 Magazine
Latest Issues
Current IssueAll About That Route
Most designers favor manual routing, but today's interactive autorouters may be changing designers' minds by allowing users more direct control. In this issue, our expert contributors discuss a variety of manual and autorouting strategies.
Creating the Ideal Data Package
Why is it so difficult to create the ideal data package? Many of these simple errors can be alleviated by paying attention to detail—and knowing what issues to look out for. So, this month, our experts weigh in on the best practices for creating the ideal design data package for your design.
Designing Through the Noise
Our experts discuss the constantly evolving world of RF design, including the many tradeoffs, material considerations, and design tips and techniques that designers and design engineers need to know to succeed in this high-frequency realm.
- Articles
- Columns
- Links
- Media kit
||| MENU - design007 Magazine
Book Excerpt: 'The Printed Circuit Designer’s Guide to… High Performance Materials', Chapter 1
March 17, 2022 | I-Connect007 Editorial TeamEstimated reading time: 1 minute
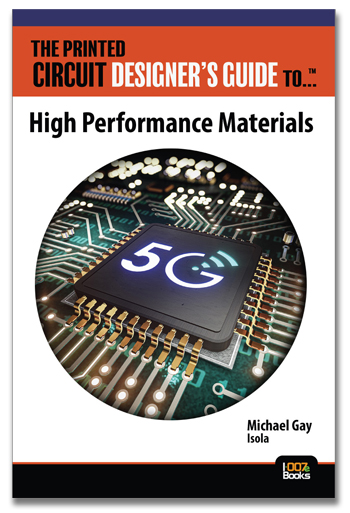
Evolution of the Resin System
Most basic resin systems have been around for a long time. Here is a little timeline of developments through more recent introductions.
- In 1907, the first laminate was made with pure phenolic resin by Westinghouse in Pittsburgh, Pennsylvania. Formica became the first true sheet laminate.The first application—a radio by Paul Eisler in 1936—led to practical manufacturing for military radios in the U.S., and use of single-sided copper-clad phenolic laminate started in about 1943 using paper and cotton as the structural component. Epoxy resin was introduced shortly after in 1947.
- Still reigning as the lowest loss resin system, a PTFE, RT/Duroid® was introduced in 1949.
- The first polyimide was discovered in 1908 by Bogart and Renshaw. However, the high heat-resistant polyimide laminate material was brought to the market in 1951.
- Isola began production of copper-clad laminate in 1956.
- Epoxy-based laminate systems followed around 1960 and used woven E-glass fabric.
- Shortly after, G-10 epoxy laminate (non-flame retardant epoxy resin plus E-glass) and a flame-retardant epoxy version called FR-4 (flame-retardant epoxy resin plus E-glass) were introduced in 1968.
From that time forward, there have been various blends, such as PPO (polyphenylene oxide)/epoxy, CE (cyanate ester)/epoxy, and polyimide/epoxy, that were created to balance properties of pure resin systems to achieve specific enhanced properties. Each new resin system was built on learning from previous products. Resin system developments for high heat applications such as LED lighting, ultra-thin non-reinforced films for capacitance and halogen-free systems to meet RoHS and REACH environmental requirements, continue to be developed to address the performance and reliability needs. With each new need, laminate material manufacturers go into the lab and see what new raw material can be used to improve resin system performance.
The process of developing a new resin system requires deep knowledge of how the PCB will be manufactured. PCB designers are most concerned with assembly process capability, long term reliability, thermal cycling performance, CAF resistance, and electrical performance, therefore, all these attributes must be balanced within the design of a resin system. The market requirements mean that laminate manufacturers must continue to research available options that will provide incremental improvements to the resin system performance.
Suggested Items
The Evolution of Picosecond Laser Drilling
06/19/2025 | Marcy LaRont, PCB007 MagazineIs it hard to imagine a single laser pulse reduced not only from nanoseconds to picoseconds in its pulse duration, but even to femtoseconds? Well, buckle up because it seems we are there. In this interview, Dr. Stefan Rung, technical director of laser machines at Schmoll Maschinen GmbH, traces the technology trajectory of the laser drill from the CO2 laser to cutting-edge picosecond and hybrid laser drilling systems, highlighting the benefits and limitations of each method, and demonstrating how laser innovations are shaping the future of PCB fabrication.
Day 2: More Cutting-edge Insights at the EIPC Summer Conference
06/18/2025 | Pete Starkey, I-Connect007The European Institute for the PCB Community (EIPC) summer conference took place this year in Edinburgh, Scotland, June 3-4. This is the third of three articles on the conference. The other two cover Day 1’s sessions and the opening keynote speech. Below is a recap of the second day’s sessions.
Day 1: Cutting Edge Insights at the EIPC Summer Conference
06/17/2025 | Pete Starkey, I-Connect007The European Institute for the PCB Community (EIPC) Summer Conference took place this year in Edinburgh, Scotland, June 3-4. This is the second of three articles on the conference. The other two cover the keynote speeches and Day 2 of the technical conference. Below is a recap of the first day’s sessions.
Preventing Surface Prep Defects and Ensuring Reliability
06/10/2025 | Marcy LaRont, PCB007 MagazineIn printed circuit board (PCB) fabrication, surface preparation is a critical process that ensures strong adhesion, reliable plating, and long-term product performance. Without proper surface treatment, manufacturers may encounter defects such as delamination, poor solder mask adhesion, and plating failures. This article examines key surface preparation techniques, common defects resulting from improper processes, and real-world case studies that illustrate best practices.
RF PCB Design Tips and Tricks
05/08/2025 | Cherie Litson, EPTAC MIT CID/CID+There are many great books, videos, and information online about designing PCBs for RF circuits. A few of my favorite RF sources are Hans Rosenberg, Stephen Chavez, and Rick Hartley, but there are many more. These PCB design engineers have a very good perspective on what it takes to take an RF design from schematic concept to PCB layout.