-
- News
- Books
Featured Books
- pcb007 Magazine
Latest Issues
Current IssueSales: From Pitch to PO
From the first cold call to finally receiving that first purchase order, the July PCB007 Magazine breaks down some critical parts of the sales stack. To up your sales game, read on!
The Hole Truth: Via Integrity in an HDI World
From the drilled hole to registration across multiple sequential lamination cycles, to the quality of your copper plating, via reliability in an HDI world is becoming an ever-greater challenge. This month we look at “The Hole Truth,” from creating the “perfect” via to how you can assure via quality and reliability, the first time, every time.
In Pursuit of Perfection: Defect Reduction
For bare PCB board fabrication, defect reduction is a critical aspect of a company's bottom line profitability. In this issue, we examine how imaging, etching, and plating processes can provide information and insight into reducing defects and increasing yields.
- Articles
- Columns
- Links
- Media kit
||| MENU - pcb007 Magazine
DFM 101: Edge Plating
March 18, 2022 | Anaya Vardya, American Standard CircuitsEstimated reading time: 4 minutes
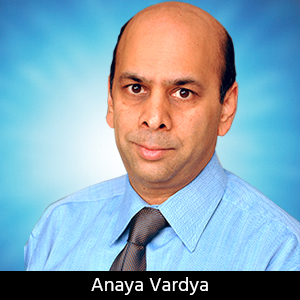
One of the biggest challenges facing PCB designers is not understanding the cost drivers in the PCB manufacturing process. This article is the latest in a series that will discuss these cost drivers (from the PCB manufacturer’s perspective) and the design decisions that will impact product reliability.
What is Edge Plating?
Edge plating is the encapsulation of the edges of printed circuit boards to improve EMI shielding of higher frequency designs, as well as for improving chassis ground in systems. The requirement for edge plating is being implemented for single axis, as well as multiple axis edges of the circuit board, including all four edges.
Edge plating is created when a rout path is implemented prior to the metallization of the circuitry features of the printed circuit board and is sometimes referred to as “plated rout.” The design requirements for implementing this technology are dependent on the requirement for the number of edges of each board, the size of the board, and whether the boards will be delivered in a multi-up array.
Stability of the material used for manufacturing of the board will also play a part in the development of the routing requirements. Materials where the reinforcement is not the standard glass-reinforced FR-4 type may require an alternative routing design to improve the structure of the parts inside the panel that is used to carry the parts during manufacturing. The parts are processed still intact inside the carrier panel, also called an array, used for manufacturing and assembly, requiring the development of tabs in some cases for edge plating. For a single edge requiring plating, tabs may not be required for stability.
Development of Tabs for Transporting the Panels
The drawing on the left in Figure 2 shows how perforated tabs are implemented for a circuit that is manufactured in a multiple-up array. The requirement is that the tabs being used to hold the board in the array will be broken off after the assembly operation (also called singulation). Figure 2 (right) shows a solid tab that is placed at the plated rout process. In both cases the internal and external layer artwork around the tabs must be void of metal. This will prevent the metal from being exposed in the singulation process. When a solid tab is used, the tab is removed at the final fabrication stage using a router (the same router that removes standard parts from the carrier panels). Removal of the tab will leave a small protrusion along the edge of the part.
Also detailed are the minimum requirements for the dimensions of the tabs. Placement of the tabs is based on assembly requirements and materials being used to construct the circuits. Less dimensionally stable materials, typically non-reinforced materials, as well as thin (0.200”), will require additional tabs for stability in processing. Conservatively, the tabs are placed every two inches along the plated edges. For non-FR-4 materials this is more the rule.
Design Rules for Plated Edges
It is required that the plating not only encapsulate the edge of the panel, but that the plating also wrap around to the surface of the panel. This is shown in Figure 3, and the minimum distance the plating is required to wrap around to the surface is 0.015”. The wrap-around is required for internal processing and adhesion of the plating to the edge. Also detailed is the minimum distance a feature can be placed to the wrap around plating (0.010”) as well as the distance required for an adjacent routed feature (0.100”).
It is typical that the plating be continuous along the entire edge of the circuit, but interruptions in the plating can be designed with two methods. By placing a tab at the interruption, and subsequently removing it, the tab prevents the plating (Figure 4a). Alternatively, the plating interruptions can be removed at the final routing stages. The subsequent removal of the plating will leave a small tab or an indentation into the circuit (Figure 4b). The indentation is created when the router bit contacts the edge where the plating is removed and advances into the circuit to completely remove the plating. When the interruption of the plating is a minimum of 0.200” the use of a tab to prevent the continuous plating can be used. When less than 0.200” the edge will be plated entirely across and subsequently removed by the routing process described.
Edge plating typically involves the connection of one or more of the internal planes in a board. These planes extend to the edge of the board and are electrically connected by the plating process. Those layers are typically fabricated with a polarity border (ref. 0.050”) to prevent exposed copper when they are routed and removed from a panel.
Figure 4: a) By placing a tab at the interruption, and subsequently removing it, the tab prevents the plating; b) the subsequent removal of the plating will leave a small tab or an indentation into the circuit.
Understanding the cost drivers in PCB fabrication and early engagement between the designer and the fabricator are crucial elements that lead to cost-effective design success. Following your fabricator’s DFM guidelines is the first place to start.
Anaya?Vardya?is president and CEO of American Standard Circuits;?co-author of The Printed Circuit Designer’s Guide to…?Fundamentals of RF/Microwave PCBs?and?Flex and Rigid-Flex Fundamentals; and author of?Thermal Management: A Fabricator's Perspective.?Visit?I-007eBooks.com?to download these and other?free, educational?titles. He?also?co-authored?“Fundamentals of Printed Circuit Board?Technologies” and provides a discussion of flex and rigid flex PCBs at RealTime with… American Standard Circuits.
Suggested Items
I-Connect007 Editor’s Choice: Five Must-Reads for the Week
07/18/2025 | Nolan Johnson, I-Connect007It may be the middle of the summer, but the news doesn’t quit, and there’s plenty to talk about this week, whether you’re talking technical or on a global scale. When I have to choose six items instead of my regular five, you know it’s good. I start by highlighting my interview with Martyn Gaudion on his latest book, share some concerning tariff news, follow that up with some promising (and not-so-promising) investments, and feature a paper from last January’s inaugural Pan-European Design Conference.
Elephantech Launches World’s Smallest-Class Copper Nanofiller
07/17/2025 | ElephantechJapanese deep-tech startup Elephantech has launched its cutting-edge 15 nm class copper nanofiller – the smallest class available globally. This breakthrough makes Elephantech one of the first companies in the world to provide such advanced material for commercial use.
Copper Price Surge Raises Alarms for Electronics
07/15/2025 | Global Electronics Association Advocacy and Government Relations TeamThe copper market is experiencing major turbulence in the wake of U.S. President Donald Trump’s announcement of a 50% tariff on imported copper effective Aug. 1. Recent news reports, including from the New York Times, sent U.S. copper futures soaring to record highs, climbing nearly 13% in a single day as manufacturers braced for supply shocks and surging costs.
I-Connect007 Editor’s Choice: Five Must-Reads for the Week
07/11/2025 | Andy Shaughnessy, Design007 MagazineThis week, we have quite a variety of news items and articles for you. News continues to stream out of Washington, D.C., with tariffs rearing their controversial head again. Because these tariffs are targeted at overseas copper manufacturers, this news has a direct effect on our industry.I-Connect007 Editor’s Choice: Five Must-Reads for the Week
Digital Twin Concept in Copper Electroplating Process Performance
07/11/2025 | Aga Franczak, Robrecht Belis, Elsyca N.V.PCB manufacturing involves transforming a design into a physical board while meeting specific requirements. Understanding these design specifications is crucial, as they directly impact the PCB's fabrication process, performance, and yield rate. One key design specification is copper thieving—the addition of “dummy” pads across the surface that are plated along with the features designed on the outer layers. The purpose of the process is to provide a uniform distribution of copper across the outer layers to make the plating current density and plating in the holes more uniform.