-
- News
- Books
Featured Books
- design007 Magazine
Latest Issues
Current IssueAll About That Route
Most designers favor manual routing, but today's interactive autorouters may be changing designers' minds by allowing users more direct control. In this issue, our expert contributors discuss a variety of manual and autorouting strategies.
Creating the Ideal Data Package
Why is it so difficult to create the ideal data package? Many of these simple errors can be alleviated by paying attention to detail—and knowing what issues to look out for. So, this month, our experts weigh in on the best practices for creating the ideal design data package for your design.
Designing Through the Noise
Our experts discuss the constantly evolving world of RF design, including the many tradeoffs, material considerations, and design tips and techniques that designers and design engineers need to know to succeed in this high-frequency realm.
- Articles
- Columns
- Links
- Media kit
||| MENU - design007 Magazine
A Textbook Look: Signal Integrity and Impedance
May 18, 2022 | Pete Starkey, I-Connect007Estimated reading time: 5 minutes
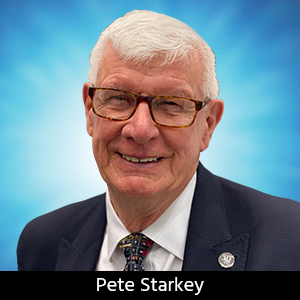
Believing that I knew a bit about signal integrity and controlled impedance, I was pleased to take the opportunity to connect with an educational webinar that I hoped would extend my knowledge. In the event I was surprised at how little I actually knew, and the webinar was an excellent learning opportunity.
Jointly organised by NCAB Group, Polar Instruments and Phoenix Contact, it brought together three expert speakers who shared their knowledge on the theoretical basis of signal integrity, the customer technical and engineering support provided by a global PCB supplier, and the design and optimization of high-speed data connectors.
The webinar was introduced and expertly moderated by Anna Brockman, team leader campaigns and media management at Phoenix Contact in Germany.
Hermann Reischer, managing director of Polar Instruments in Austria, gave the clearest first-principles explanation of signal integrity and controlled impedance that I have experienced in many years. He made the topic intelligible and understandable by breaking it into its most basic elements and explaining each in plain language with meaningful illustrations.
Against a background of high-speed requirements such as 77 GHz analogue frequencies in automotive radar applications, and ever-rising digital data rates with pico-second rise times, the printed circuit board ceased to be a passive interconnecting substrate and became a complex component in its own right. A PCB trace behaved like a transmission line when its physical length was of the same order as the electrical wavelength of the transmitted signal.
He examined the properties of a transmission line: in addition to its DC resistance it experienced a propagation delay depending on the dielectric characteristics of the material surrounding it, which also contributed to losses as well as those attributed to copper roughness and line length. The transmission line had a characteristic impedance determined by trace width, dielectric spacing, and relative permittivity. All of these parameters needed to be considered in order to ensure signal integrity, which became increasingly difficult to maintain as frequency increased. PCB material selection and stack-up, trace width, dielectric separation, design and layout, and component placement were all critical.
Reischer explained how a transmission line could be considered in terms of a series of inductors and capacitors and described how a signal was propagated along it, charging each successive capacitor element. The goal was to achieve constant impedance across the entire length of the line, with a uniform voltage and current wave-front in order to ensure good signal integrity. The propagation speed of an electromagnetic wave was a function of the speed of light and the permittivity of the dielectric, which for air or vacuum was 1.0. In typical PCB materials with relative permittivity around 4.0, the propagation speed was reduced from the speed of light to about half that value.
The “critical line length,” beyond which a conductor would be considered a transmission line, was related to the rise time of the signal. Early semiconductor devices had rise times of around 5 nanoseconds, giving a bandwidth of 70 MHz and a critical length of 36 cm. Current gallium arsenide devices had rise times of 0.3 nanoseconds, giving bandwidth of 1.166 GHz and a critical length of 2 cm.
He clarified the differences in propagation characteristics between low-speed and high-speed signals, and he explained the ways in which electromagnetic waves were reflected at impedance discontinuities. Impedance matching offered a solution, and he gave an example of a typical transmission system where the impedances of the source, the transmission line, and the termination were matched at 50 ohms. This was generic in a radio frequency environment; 75 ohms was typical in video applications, 90 ohms in USB transmission, and 100 ohms for Ethernet.
Reischer commented that his system example illustrated the essential interaction between the three companies contributing to the webinar: Phoenix Contact supplying interconnects, NCAB Group supplying printed circuit boards, and Polar Instruments supplying simulation tools for calculating impedance.
So how to make sure that the transmission path had the correct impedance? He took a familiar example of a coaxial cable, whose impedance was determined by its geometry and the permittivity of the insulating material and demonstrated how the principles could be adapted to the planar structure of a PCB in the form of an offset stripline. The geometry and the permittivity of the material determined the impedance, and he showed a range of examples of “single-ended” structures. In contrast were “differential” structures, widely used in digital transmission systems, usually consisting of two traces running in parallel and coupled with a capacitor. The advantages of differential signalling included improved noise immunity, lower voltage requirements, and higher data rates.
Reischer listed the factors influencing impedance. Trace width was the most significant and was simple to modify. Substrate height, relative permittivity, and copper thickness were determined by material selection, and etch-back was process-dependent. Solder mask thickness could have a significant effect on the properties of edge-coupled microstrip designs, as could the influence of local resin-rich areas if similar features were embedded within the structure of the PCB. He discussed the practical aspects of resin distribution and thickness control during multilayer pressing.
Vias gave some interesting effects; they were generally quite small compared with the wavelength of the signal, so they could normally be ignored except at extremely high frequencies. But on thick boards, as via stub-length approached a quarter of the wavelength of the signal, they could cause undesirable resonance. Back-drilling was a technique used to mitigate these effects.
Future challenges included tighter impedance tolerance specifications, lower dielectric thicknesses and narrower trace widths. Frequencies beyond 5 GHz resulted in “lossy” transmission lines; dielectric losses could be reduced by using new base materials and smoother copper could reduce skin effects, both at increased material cost. From a design point of view, Reischer recommended keeping traces as short as possible and ensuring uninterrupted signal return paths. For various reasons it was preferred to place critical lines on inner layers. And he emphasised the importance of consulting with the PCB vendor on stack-up design and material selection before commencing the layout.
To read this entire article, which appeared in the May 2022 issue of Design007 Magazine, click here.
Suggested Items
Driving Innovation: Direct Imaging vs. Conventional Exposure
07/01/2025 | Simon Khesin -- Column: Driving InnovationMy first camera used Kodak film. I even experimented with developing photos in the bathroom, though I usually dropped the film off at a Kodak center and received the prints two weeks later, only to discover that some images were out of focus or poorly framed. Today, every smartphone contains a high-quality camera capable of producing stunning images instantly.
Hands-On Demos Now Available for Apollo Seiko’s EF and AF Selective Soldering Lines
06/30/2025 | Apollo SeikoApollo Seiko, a leading innovator in soldering technology, is excited to spotlight its expanded lineup of EF and AF Series Selective Soldering Systems, now available for live demonstrations in its newly dedicated demo room.
Indium Corporation Expert to Present on Automotive and Industrial Solder Bonding Solutions at Global Electronics Association Workshop
06/26/2025 | IndiumIndium Corporation Principal Engineer, Advanced Materials, Andy Mackie, Ph.D., MSc, will deliver a technical presentation on innovative solder bonding solutions for automotive and industrial applications at the Global Electronics A
Fresh PCB Concepts: Assembly Challenges with Micro Components and Standard Solder Mask Practices
06/26/2025 | Team NCAB -- Column: Fresh PCB ConceptsMicro components have redefined what is possible in PCB design. With package sizes like 01005 and 0201 becoming more common in high-density layouts, designers are now expected to pack more performance into smaller spaces than ever before. While these advancements support miniaturization and functionality, they introduce new assembly challenges, particularly with traditional solder mask and legend application processes.
Knocking Down the Bone Pile: Tin Whisker Mitigation in Aerospace Applications, Part 3
06/25/2025 | Nash Bell -- Column: Knocking Down the Bone PileTin whiskers are slender, hair-like metallic growths that can develop on the surface of tin-plated electronic components. Typically measuring a few micrometers in diameter and growing several millimeters in length, they form through an electrochemical process influenced by environmental factors such as temperature variations, mechanical or compressive stress, and the aging of solder alloys.