-
- News
- Books
Featured Books
- design007 Magazine
Latest Issues
Current IssueAll About That Route
Most designers favor manual routing, but today's interactive autorouters may be changing designers' minds by allowing users more direct control. In this issue, our expert contributors discuss a variety of manual and autorouting strategies.
Creating the Ideal Data Package
Why is it so difficult to create the ideal data package? Many of these simple errors can be alleviated by paying attention to detail—and knowing what issues to look out for. So, this month, our experts weigh in on the best practices for creating the ideal design data package for your design.
Designing Through the Noise
Our experts discuss the constantly evolving world of RF design, including the many tradeoffs, material considerations, and design tips and techniques that designers and design engineers need to know to succeed in this high-frequency realm.
- Articles
- Columns
- Links
- Media kit
||| MENU - design007 Magazine
What Happens When You Assume?
July 5, 2022 | I-Connect007 Editorial TeamEstimated reading time: 4 minutes
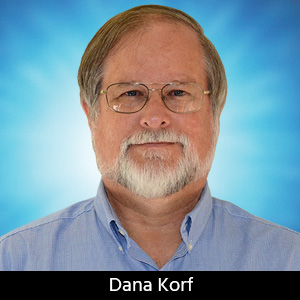
When we started planning a recent issue of Design007 Magazine on design with manufacturing, or DWM, we knew we needed I-Connect007 columnist Dana Korf to weigh in on this new acronym, and what true DWM would look like in operation. In this interview, Dana explains what it will take to achieve total communication among all the stakeholders in the PCB development cycle. He also stresses the need for everyone involved in PCB design and manufacturing to stop making assumptions, even at the risk of being labeled as “that guy” who asks too many questions.
Andy Shaughnessy: Dana, we’re hearing more talk about design with manufacturing, or DWM. For all the talk about DFM, communication among the designers, fabricators, and assemblers just doesn’t happen as often as we might expect. In your opinion, what does true DWM look like? And how do we get designers and manufacturers to embrace it?
Dana Korf: When I first heard about DWM, I thought it implied we were currently designing without manufacturing. I’m not clear what it actually means because that’s what we’re doing today. I’ve simplified the problem into three parts. First, the fabricators don’t provide all the design rules that front-end engineering uses to evaluate a design for their customers. In some companies, the process engineers won’t tell the front-end engineers all the rules.
Second, the data transfer we’re using is based on an N/C technique from the 1950s, with a lot of files, and people have to unintelligently guess what the data is supposed to be instead of using more intelligent formats like IPC-2581 or ODB++. Neither intelligent format is perfect, but they’re definitely better than Gerber-based packages. Third, the design tool can’t utilize the fabricator design rules even if they were provided.
I did a design review a couple of years ago with a tier one software supplier. I found that even if they were provided all the fabricator design rules electronically, they’d still have to perform a lot of scripting to incorporate most of the provided DFM rules. A common example I give is the minimum space between a conductor to the edge of a board. Is the edge scored? Is it routed? Is it punched? How are you making this? These have different sets of rules, most likely, and the design doesn’t necessarily have the right rules because the design system doesn’t have knowledge of how the edge will be created.
Over the years, we’ve just accepted this problem. In the `70s when I first got into this, we hand-taped artwork on Mylar. They photographically reduced it down to the proper size, and they built it. It was pretty simple. Then we invented CAM tools. That was where we went downhill, along with the first manufacturer who said, “I’ll fix your design for free.” That’s when design data quality went downhill.
Happy Holden: Yes. I’m not sure that DWM is actually real, because who in manufacturing has that kind of time to devote to a customer?
Dan Feinberg: My first thought is: Do you design for manufacturing, or do you design for the performance of the device? What comes first when you have to make a choice between cost and reliability?
Korf: Right. There are two problems for me. One is that board fabricators may not be selected until after the design is done, and they’re selected by procurement or the EMS company. They go out, source it, then select the suppliers at the end of the layout. You don’t know who you’re designing for. I teach a DFM class for IPC, and one of the things I teach is the IPC definition of DFM. It’s something along the lines of, “Design for optimum cost to manufacturability,” and I add, “and meets the design intent.”
To your comment, Dan, you’re really trying to make the board work first and then ensure it’s producible. Cost is actually third, because if they all come back and they don’t work, you’ve lost all your money anyway. I teach students that if you’re going to design for a manufacturer, figure out whether it’s the right one for you. Not every fabricator can build every capability, and not everyone has the same set of design rules for a given technology. That’s part of the problem, too. We’re chasing cost/price along with quality and performance. It’s a triangle; the old saying is that you can only get two out of three of those.
Shaughnessy: It sounds like a lot of these issues arose out of outsourcing. None of this happened during the time of captives.
Korf: That’s right. When you had in-house manufacturing, the factory could be tuned toward the product and everything was optimized. You had a lot less variability, a lot better chance of getting good designs out, and getting them right the first time. But, even then, they still had data errors.
To read this entire conversation, which appeared in the June 2022 issue of Design007 Magazine, click here.
Suggested Items
Delta SEA Partner Event 2025 Unites Regional Partners to Embrace a “Future Ready” Vision
07/03/2025 | Delta ElectronicsDelta Electronics (Thailand) Public Company Limited, successfully hosted its Delta SEA Partner Event 2025: Future Ready at Delta Chungli Plant 5, Taiwan on June 10 – 11 , 2025.
Murray Percival Company Welcomes CeTaQ to Its Line Card, Optimizing SMT Processes for PCB Manufacturers
07/03/2025 | Murray Percival CompanyThe Murray Percival Company, a trusted supplier to the Midwest's electronics industry, is pleased to announce that it has added CeTaQ to its line card, a global expert in Surface Mount Technology (SMT) measurement systems.
RBB’s Jeff Schartiger Appointed to SMTA Ohio Board as Technical Advisor
07/03/2025 | RBBRBB, a trusted leader in electronics manufacturing since 1973, is proud to announce that Jeff Schartiger, Operations Manager at RBB, has been appointed to the SMTA Ohio Chapter Board as a Technical Advisor.
Kitron Receives EUR 4 Million Contract for Defense Airborne Radar Application
07/02/2025 | KitronKitron has received an order valued at EUR 4 million to produce electronics modules for airborne radar application, destined for the US market.
Zollner Completes Full Acquisition of Bluechips Microhouse
07/01/2025 | Zollner Elektronik AGZollner Elektronik AG has successfully finalized its complete takeover of Bluechips Microhouse Co., Ltd., in Thailand. In the future the company will operate as part of the Zollner Group of companies under the leadership of Thomas Kiefl—strategically networked, technologically focused and internationally oriented.