-
- News
- Books
Featured Books
- design007 Magazine
Latest Issues
Current IssueAll About That Route
Most designers favor manual routing, but today's interactive autorouters may be changing designers' minds by allowing users more direct control. In this issue, our expert contributors discuss a variety of manual and autorouting strategies.
Creating the Ideal Data Package
Why is it so difficult to create the ideal data package? Many of these simple errors can be alleviated by paying attention to detail—and knowing what issues to look out for. So, this month, our experts weigh in on the best practices for creating the ideal design data package for your design.
Designing Through the Noise
Our experts discuss the constantly evolving world of RF design, including the many tradeoffs, material considerations, and design tips and techniques that designers and design engineers need to know to succeed in this high-frequency realm.
- Articles
- Columns
- Links
- Media kit
||| MENU - design007 Magazine
DFM 101: Final Finishes—OSP
March 9, 2023 | Anaya Vardya, American Standard CircuitsEstimated reading time: 1 minute
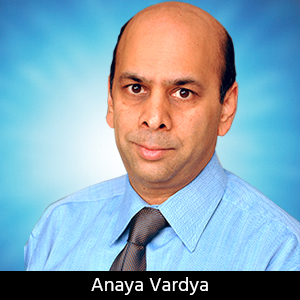
Introduction
One of the biggest challenges facing PCB designers is not understanding the cost drivers in the PCB manufacturing process. The next final finishes to discuss in this series is OSP. As with all surface finishes there are pros and cons with the decision of which to use. It is a combination of application, cost, and the properties of the finish. OSP is RoHS-compliant as there is zero lead content in the finish.
Final Finishes
OSP (Organic Solderability Preservative)
OSP is a thin organic coating, typically 5.9 to 11.8 µin [0.15 to 0.30 µm] thick, designed to prevent the oxidation of copper to maintain solderability over an extended period. Compared with other surface finish technologies, OSP is somewhat different. It uses a chemical process to produce an organic film on the bare copper surface which acts as a barrier to copper oxidation. OSP is organic, not metallic, and its cost is lower than most surface treatment technologies.
As with all surface finishes, the primary purpose is to protect the solderable surfaces on the PCB from oxidation and to aid in assembly soldering. This process coats a very thin coating of an organic material that inhibits copper oxidation. It is so thin that it is nearly impossible to see and measure. The organic material is removed by the assembly flux. Boards that have been OSP coated will have bright copper pad coloration. OSP is specially designed for mixed metal applications, such as electroless nickel immersion gold (ENIG). The OSP selectively deposits on copper while leaving gold connectors or metallic heat sinks free of contamination.
There are a couple of common OSP finishes widely used in the industry:
ENTEK CU-56: This is used for assemblies that will only go through a single reflow process. This finish is not being utilized much anymore because of the use of mixed technology boards (SMT and through-hole).
ENTEK CU-106A: This is the most prevalent version primarily due to the ability to survive multiple thermal assembly operations. PCBs that have multiple surface finishes can use the CU-106A(X) finish.
To read this entire article, which appeared in the February 2023 issue of Design007 Magazine, click here.
Suggested Items
The Evolution of Picosecond Laser Drilling
06/19/2025 | Marcy LaRont, PCB007 MagazineIs it hard to imagine a single laser pulse reduced not only from nanoseconds to picoseconds in its pulse duration, but even to femtoseconds? Well, buckle up because it seems we are there. In this interview, Dr. Stefan Rung, technical director of laser machines at Schmoll Maschinen GmbH, traces the technology trajectory of the laser drill from the CO2 laser to cutting-edge picosecond and hybrid laser drilling systems, highlighting the benefits and limitations of each method, and demonstrating how laser innovations are shaping the future of PCB fabrication.
Day 2: More Cutting-edge Insights at the EIPC Summer Conference
06/18/2025 | Pete Starkey, I-Connect007The European Institute for the PCB Community (EIPC) summer conference took place this year in Edinburgh, Scotland, June 3-4. This is the third of three articles on the conference. The other two cover Day 1’s sessions and the opening keynote speech. Below is a recap of the second day’s sessions.
Day 1: Cutting Edge Insights at the EIPC Summer Conference
06/17/2025 | Pete Starkey, I-Connect007The European Institute for the PCB Community (EIPC) Summer Conference took place this year in Edinburgh, Scotland, June 3-4. This is the second of three articles on the conference. The other two cover the keynote speeches and Day 2 of the technical conference. Below is a recap of the first day’s sessions.
Preventing Surface Prep Defects and Ensuring Reliability
06/10/2025 | Marcy LaRont, PCB007 MagazineIn printed circuit board (PCB) fabrication, surface preparation is a critical process that ensures strong adhesion, reliable plating, and long-term product performance. Without proper surface treatment, manufacturers may encounter defects such as delamination, poor solder mask adhesion, and plating failures. This article examines key surface preparation techniques, common defects resulting from improper processes, and real-world case studies that illustrate best practices.
RF PCB Design Tips and Tricks
05/08/2025 | Cherie Litson, EPTAC MIT CID/CID+There are many great books, videos, and information online about designing PCBs for RF circuits. A few of my favorite RF sources are Hans Rosenberg, Stephen Chavez, and Rick Hartley, but there are many more. These PCB design engineers have a very good perspective on what it takes to take an RF design from schematic concept to PCB layout.