-
- News
- Books
Featured Books
- design007 Magazine
Latest Issues
Current IssueShowing Some Constraint
A strong design constraint strategy carefully balances a wide range of electrical and manufacturing trade-offs. This month, we explore the key requirements, common challenges, and best practices behind building an effective constraint strategy.
All About That Route
Most designers favor manual routing, but today's interactive autorouters may be changing designers' minds by allowing users more direct control. In this issue, our expert contributors discuss a variety of manual and autorouting strategies.
Creating the Ideal Data Package
Why is it so difficult to create the ideal data package? Many of these simple errors can be alleviated by paying attention to detail—and knowing what issues to look out for. So, this month, our experts weigh in on the best practices for creating the ideal design data package for your design.
- Articles
- Columns
- Links
- Media kit
||| MENU - design007 Magazine
Slash Sheets and Material Selection
June 1, 2023 | I-Connect007 Editorial TeamEstimated reading time: 2 minutes
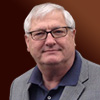
In a recent I-Connect007 survey to PCB designers, about one third of respondents said they consult IPC’s so-called slash sheets, such as IPC-4101/126, that contain a variety of information about PCB materials. But many designers say these specs don’t contain enough information. Some ask their fabricator to pick a material, and still others say, “It’s an RF board, and I always use supplier X for RF.” What’s the best process for selecting your PCB materials?
Doug Sober helped pioneer the development of IPC’s first slash sheets in 1996 for IPC-4101 Specification for Base Materials for Rigid and Multilayer Printed Boards and we asked him to discuss slash sheets—what they are, what they are not, and why PCB designers might benefit from an IPC materials guide developed specifically for designers.
Andy Shaughnessy: Doug, let’s start with your work with IPC and slash sheet development.
Doug Sober: I started in the laminate and prepreg business in 1978 for General Electric and was sent to my first IPC meeting in 1980. I got heavily involved right away with the task groups regarding specifications for laminates, prepregs, copper foils, glass fabric, resin coated foil, etc. The first standard we did was IPC-4101, but it did not just come out of thin air. We had a document from the military called MIL-S-13949H that had requirements for base materials. The requirements were physical such as flex strength and peel strength, electrical such as Dk and Df, thermal such as Tg and solder float, and environmental such as moisture absorption and fungus resistance. After IPC-4101 was all finished, it had specification sheets for simple FR-4s and polyimide base materials of various types.
The military had these specification sheets which described specific base materials and, as laminate and prepreg producers, we had to qualify our products to the requirements of the sheets. With specification sheet 21, for example, a bevy of lab tests proved that we met the requirements. Then the Defense Electronics Supply Center (DESC) would list our product by commercial name on their qualified product list (QPL). For example, Westinghouse’s FR-4 product 65M38 as listed on the QPL for specification sheet 21. Once a year, Lowell Sherman or Dave Corbett from DESC came to audit each base material supplier. When the 3-11 subcommittee created IPC-4101, we duplicated MIL-S-13949 because we wanted the military to sign off on it, discontinue their document, and use IPC-4101 in its place. In 1996, with the help of Dave Bergman negotiating with the military higher-ups, IPC-4101 was launched and Mil-S-13949 was discontinued.
To read this entire conversation, which appeared in the May 2023 issue of Design007 Magazine, click here.
Suggested Items
Knocking Down the Bone Pile: Addressing End-of-life Component Solderability Issues, Part 4
07/15/2025 | Nash Bell -- Column: Knocking Down the Bone PileIn 1983, the Department of Defense identified that over 40% of military electronic system failures in the field were electrical, with approximately 50% attributed to poor solder connections. Investigations revealed that plated finishes, typically nickel or tin, were porous and non-intermetallic.
SHENMAO Strengthens Semiconductor Capabilities with Acquisition of PMTC
07/10/2025 | SHENMAOSHENMAO America, Inc. has announced the acquisition of Profound Material Technology Co., Ltd. (PMTC), a premier Taiwan-based manufacturer of high-performance solder balls for semiconductor packaging.
KYZEN to Highlight Understencil and PCB Cleaners at SMTA Querétaro Expo and Tech Forum
07/09/2025 | KYZEN'KYZEN, the global leader in innovative environmentally responsible cleaning chemistries, will exhibit at the SMTA Querétaro Expo & Tech Forum, scheduled to take place Thursday, July 24, at Centro de Congresos y Teatro Metropolitano de Querétaro.
Driving Innovation: Direct Imaging vs. Conventional Exposure
07/01/2025 | Simon Khesin -- Column: Driving InnovationMy first camera used Kodak film. I even experimented with developing photos in the bathroom, though I usually dropped the film off at a Kodak center and received the prints two weeks later, only to discover that some images were out of focus or poorly framed. Today, every smartphone contains a high-quality camera capable of producing stunning images instantly.
Hands-On Demos Now Available for Apollo Seiko’s EF and AF Selective Soldering Lines
06/30/2025 | Apollo SeikoApollo Seiko, a leading innovator in soldering technology, is excited to spotlight its expanded lineup of EF and AF Series Selective Soldering Systems, now available for live demonstrations in its newly dedicated demo room.