-
- News
- Books
Featured Books
- pcb007 Magazine
Latest Issues
Current IssueSales: From Pitch to PO
From the first cold call to finally receiving that first purchase order, the July PCB007 Magazine breaks down some critical parts of the sales stack. To up your sales game, read on!
The Hole Truth: Via Integrity in an HDI World
From the drilled hole to registration across multiple sequential lamination cycles, to the quality of your copper plating, via reliability in an HDI world is becoming an ever-greater challenge. This month we look at “The Hole Truth,” from creating the “perfect” via to how you can assure via quality and reliability, the first time, every time.
In Pursuit of Perfection: Defect Reduction
For bare PCB board fabrication, defect reduction is a critical aspect of a company's bottom line profitability. In this issue, we examine how imaging, etching, and plating processes can provide information and insight into reducing defects and increasing yields.
- Articles
- Columns
- Links
- Media kit
||| MENU - pcb007 Magazine
Estimated reading time: 1 minute
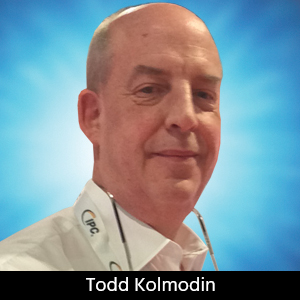
Where Do We Go From Here?
This month, Gardien’s resident expert Todd Kolmodin answers questions as posed by Dan Beaulieu of D.B. Consulting about the future of electrical test.
Dan Beaulieu: Todd, do you see E-test as something that stays in the board shops or something that eventually gets so high-tech that it has to be done by experts?
Todd Kolmodin: That’s a great question. Technology is evolving so fast now that there will be a break-point as to whether a board shop can continue to successfully test the product they are building with the equipment they have. Advances in PCB technology are quickly pulling ahead of many of the older grid test machines and forcing more of the product to flying probes, which can cause issues in capacity and velocity for testing product and force new capital investments in electrical test equipment. This can be a difficult position for a board shop as this capital expense is difficult to justify.
Capital for ET machines in one sense is buying an insurance policy rather than adding any “value-add” to the PCB itself. This can be a very difficult decision for manufacturing budgets. So it is fairly safe to project that as we continue on this technology roadmap we will see more outsourcing; as for the manufacturer, it is more cost effective on the bottom line.
Beaulieu: Do you see the equipment itself getting more sophisticated and thus very expensive?
Kolmodin: The test equipment manufacturers will still try to make the equipment as affordable as possible, but the demands of technology are still to be addressed. In Asia, the use of quad-density grid testers and automated dedicated testers is the norm. Here in North America we have not seen too much of this technology as of yet. I have recently seen some new designs here in the U.S. that the standard double-density grid test machine cannot even test. This forces the flying probe. Soon, the need for the quad density machines will be required to effectively provide the economical test solution. This also means capital investments and yes, these machines do have higher price tags.
Read the full column here.
Editor's Note: This column originally appeared in the September 2014 issue of The PCB Magazine.
More Columns from Testing Todd
Testing Todd: Why 4-wire Kelvin?Testing Todd: Why TDR?
Testing Todd: Positivity Boosts Employee Morale
Testing Todd: Preparing Employees for the Long Haul
Testing Todd: Where Can We Improve?
Testing Todd: Turning Into the Wind
Testing Todd: Coming Back to Life—Design Recovery
Testing Todd: Decision Time—Invest or Delegate?