-
- News
- Books
Featured Books
- design007 Magazine
Latest Issues
Current IssueShowing Some Constraint
A strong design constraint strategy carefully balances a wide range of electrical and manufacturing trade-offs. This month, we explore the key requirements, common challenges, and best practices behind building an effective constraint strategy.
All About That Route
Most designers favor manual routing, but today's interactive autorouters may be changing designers' minds by allowing users more direct control. In this issue, our expert contributors discuss a variety of manual and autorouting strategies.
Creating the Ideal Data Package
Why is it so difficult to create the ideal data package? Many of these simple errors can be alleviated by paying attention to detail—and knowing what issues to look out for. So, this month, our experts weigh in on the best practices for creating the ideal design data package for your design.
- Articles
- Columns
- Links
- Media kit
||| MENU - design007 Magazine
Estimated reading time: 1 minute
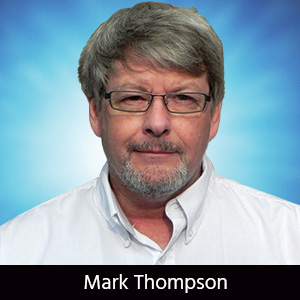
Qualifying Your Fabricator: Identifying Winners (and Losers)
This month, I am once again weighing in with tips on qualifying a fabricator. In previous columns, I mentioned three things everyone should expect from their fabricators:
- Quick quote responses;
- Outstanding quality; and
- Consistent on-time delivery.
I would like to add that, based on today’s board complexities, a review should be done prior to quote to make sure no manufacturing issues occur. This is critical when it comes to things like minimum pre-preg interfaces on high-copper coil boards or jobs with unique reference planes for various impedance scenarios. A potential customer would much rather be told up front that a given design is not producible than to wait three days for a quote, only to have the part go on hold after release to manufacturing because a good review was not done prior to release.
Quote Me on This
So, let’s start with the quote process. Whether the part is a simple double-sided part or a complex multilayer with numerous needs, you really would like to see a quote response back in a few hours, not a few days. Additionally you want accurate quotes that have taken into consideration all aspects of the board, such as drill time based on hole quantity, additional time for AS-9102 or Class 3 6012, first article reports, and any additional time if outside services are needed.
A three-day quote should be just that, regardless of your location and any outsources you may require. It is never good when a three-day is quoted but due to outside services or time zones still results in delays. Make sure any questions you have are asked up front to avoid these delays. Also, make sure there is a contact available for expedites.
Read the full column here.
Editor's Note: This column originally appeared in the November 2013 issue of The PCB Design Magazine.
More Columns from The Bare (Board) Truth
The Bare (Board) Truth: My Top Six Design ChallengesThe Bare (Board) Truth: Via Basics
The Bare (Board) Truth: 5 Questions About Improving Thermal Management
The Bare (Board) Truth: Teaching the Next Generation—An Overview of Today’s University Courses
The Bare (Board) Truth: Fabrication Starts With Solid Design Practices
Board Negotiations: Design Rules and Tolerances
The Bare (Board) Truth: Eliminate Confusion
The Bare (Board) Truth: Getting on the Same Page—A Data Story