-
- News
- Books
Featured Books
- design007 Magazine
Latest Issues
Current IssueRules of Thumb
This month, we delve into rules of thumb—which ones work, which ones should be avoided. Rules of thumb are everywhere, but there may be hundreds of rules of thumb for PCB design. How do we separate the wheat from the chaff, so to speak?
Partial HDI
Our expert contributors provide a complete, detailed view of partial HDI this month. Most experienced PCB designers can start using this approach right away, but you need to know these tips, tricks and techniques first.
Silicon to Systems: From Soup to Nuts
This month, we asked our expert contributors to weigh in on silicon to systems—what it means to PCB designers and design engineers, EDA companies, and the rest of the PCB supply chain... from soup to nuts.
- Articles
- Columns
Search Console
- Links
- Media kit
||| MENU - design007 Magazine
Crosshatched Planes in Impedance-Controlled Flex-Rigid PCBs
July 20, 2010 | Polar InstrumentsEstimated reading time: 4 minutes
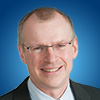
by Martyn Gaudion
Flex and flex-rigid PCB fabricators have long requested a practical method of predicting the impedance of stripline and microstrip PCB traces when crosshatching return paths are deployed, rather than the solid copper return paths of traditional rigid PCBs. Whilst RF purists may feel discomfort at the thought of using crosshatch as a high-frequency return path with all the implications of lengthened return path, etc., in practical terms, using crosshatched planes on flex and flex-rigid PCBs is a practical and realistic method of keeping impedance-controlled traces at a manufacturable dimension, and also retaining the desired flexibility of the assembly. Whilst this technique is in widespread use in circuits up to around 2GHz, further research is needed for suitable techniques at higher frequencies where line losses and ultimately signal integrity effects of the crosshatch itself may come into play.
Algebraic Equations
Prior to the widespread use of field solvers, closed form equations were widely used for the calculation of impedance; an example below is shown from Wadell [1]. Whilst a wide number of structures are described in Waddell, the closed form equations had limitations when addressing small geometries and their inability to take into account etch taper often encountered on fine line traces. Furthermore, Wadell does not cite any closed form equations for the handling of structures using crosshatched ground planes. The flexible circuits community has often requested a solution, but the market space is usually deemed too small for an economic approach. Modelling is possible, however, with the resort to high-cost 3-D field solvers requiring skilled operation [2]. An example closed form equation for a solid ground plane is shown in Figure 1.Figure 1: Surface microstrip.
Parameter w' is the equivalent width of a track of zero w.
Field Solvers
In the 1999 IPC Expo paper "Calculation of PCB Track Impedance," [3] it was shown that computer processing power had put the use of numerical field solving techniques within reach of PCB fabricators, who could now benefit from 2-D field solving technology with commonly available computer hardware. However, at this time, the demand for crosshatch modelling was still too small to justify the development of dedicated tools for the flex and flex-rigid industry.
Flexible Material Tolerance
It is widely accepted that material tolerances encountered in flex and flex rigid fabrication are significantly higher, in some cases up to three times those of FR4 [4], therefore designers planning to deploy high-speed transmission lines on flexible substrates should take these variations into account and plan for more variation at an early stage whilst in discussion with their chosen fabricator(s).
XFE
In early 2010, an alternate approach to modelling crosshatch was proposed using a proprietary technique, "XFE" from Polar Instruments (see Figure 2); this technique uses traditional 2-D field solvers, but runs with multiple passes using a unique algorithm to correct for the effects of flex over a wide range of typical impedance controlled structures.
This multi-pass approach has given beneficial improvements in the capability of solvers to model more closely the effects of a wide variety of crosshatch geometries. Initial results compare favourably with cross section and measurement data from three industry partners [5].Figure 2: XFE hatch configuration.
Analysis was performed over a wide range of pitches, widths and structures. However, the authors recognise that further analysis is still required to prove the method in the wide variety of structures and geometries that are commonly encountered in the flex and flex rigid environment.
Higher Frequencies Whilst crosshatching has been proven by the industry over the years to be a practical approach to designing flexible transmission lines with a reasonable line width for the desired impedance, caution should be employed when deploying such a solution at frequencies above 2GHz or when line losses become significant.
In lossy line applications, such as modern ultra-high-speed differential signalling applications, the design authority should resort to rigorous modelling and testing prior to deploying crosshatching for raising impedance of a line.
Alternative structures, such as coplanar waveguide, may give a better solution in these areas; however, this should be confirmed by a thorough 3-D modelled approach.
Results
Two enhanced methods were modelled against a range of physical samples; at the time of submission, the data is still being correlated and a representative sample of final results is included in Appendix A found at the end of this presentation.
Discussion
The proposed XFE technique using multiple 2-D solver passes shows promise in offering PCB fabricators a reduction in the number of prototype turns required to achieve the desired impedance on flex-rigid PCBs. The technique, however, is only regarded suitable for PCBs with line losses small enough to be ignored.
Conclusion
The authors have shown that this field solver enhancement can be used to model more closely the real-world impedance as fabricated on a flex-rigid PCB using crosshatch return planes. Designers are cautioned that because material tolerances and stability are significantly looser on polyimide than on FR4 their design targets for impedance tolerance should be adjusted to reflect this material variation and specifications should be set realistically.
References
1. Waddell, Brian C.; "Transmission Line Design Handbook," Artech House, Inc., ISBN 0-89006-436-9.2. Bogatin, Eric; Justice, Mike; DeRego, Todd and Zimmer, Steve, "Field Solvers and PCB Stack-up Analysis: Comparing Measurements and Modelling,"IPC Printed Circuit Expo 1998, paper 505-3.3. Burkhardt, Andrew; Gregg Christopher; Staniforth, J, Alan, "Calculation of PCB track impedance," IPC Printed Circuit Expo 1999.4. Gallant, Mark, "Guide to flex rigid design," PCD&F, October, 2006.5. The authors wish to acknowledge the assistance of Würth Elektronik GmbH & Co. KG and other cooperating companies.
Appendix A: Impedance variations versus solid/cross-hatch configurations.