-
-
News
News Highlights
- Books
Featured Books
- design007 Magazine
Latest Issues
Current IssueAll About That Route
Most designers favor manual routing, but today's interactive autorouters may be changing designers' minds by allowing users more direct control. In this issue, our expert contributors discuss a variety of manual and autorouting strategies.
Creating the Ideal Data Package
Why is it so difficult to create the ideal data package? Many of these simple errors can be alleviated by paying attention to detail—and knowing what issues to look out for. So, this month, our experts weigh in on the best practices for creating the ideal design data package for your design.
Designing Through the Noise
Our experts discuss the constantly evolving world of RF design, including the many tradeoffs, material considerations, and design tips and techniques that designers and design engineers need to know to succeed in this high-frequency realm.
- Articles
- Columns
- Links
- Media kit
||| MENU - design007 Magazine
Estimated reading time: 1 minute
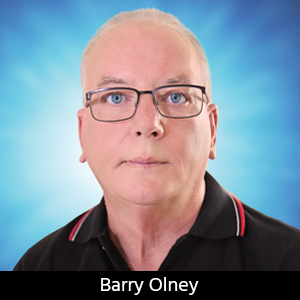
Effects of Surface Roughness on High-Speed PCBs
At frequencies below 1GHz, the effect of copper surface roughness on dielectric loss is negligible. However, as frequency increases, the skin effect drives the current into the surface of the copper, dramatically increasing loss. When the copper surface is rough, the effective conductor length extends as current follows along the contours of the surface up and down with the topography of the copper surface. At high frequencies, the effective resistance of the copper increases relative to the additional distance over which the current must transverse the contours of the surface. The total loss comprises of the sum of the conductor loss and dielectric loss.
Whilst it may be possible to manufacture copper foil with a perfect mirror-smooth finish, the foil-to-resin adhesion would be compromised. This would considerably increase the possibility of delamination during the thermal stress of the PCB fabrication and assembly processes. For this reason, a reduced oxide coating is applied to the inner core layers to promote adhesion of the prepreg resin as it flows under the applied heat and pressure to cure.
Skin effect is the tendency of an alternating current to become distributed within a conductor such that the current density is largest near the surface, and decreases with greater depths in the conductor. The higher the frequency, the greater the tendency for current to take the path of lower inductance on the outer surface of the conductor.
More Columns from Beyond Design
Beyond Design: The Metamorphosis of the PCB RouterBeyond Design: Radiation and Interference Coupling
Beyond Design: Key SI Considerations for High-speed PCB Design
Beyond Design: Electro-optical Circuit Boards
Beyond Design: AI-driven Inverse Stackup Optimization
Beyond Design: High-speed Rules of Thumb
Beyond Design: Integrated Circuit to PCB Integration
Beyond Design: Does Current Deliver the Energy in a Circuit?