-
-
News
News Highlights
- Books
Featured Books
- design007 Magazine
Latest Issues
Current IssueAll About That Route
Most designers favor manual routing, but today's interactive autorouters may be changing designers' minds by allowing users more direct control. In this issue, our expert contributors discuss a variety of manual and autorouting strategies.
Creating the Ideal Data Package
Why is it so difficult to create the ideal data package? Many of these simple errors can be alleviated by paying attention to detail—and knowing what issues to look out for. So, this month, our experts weigh in on the best practices for creating the ideal design data package for your design.
Designing Through the Noise
Our experts discuss the constantly evolving world of RF design, including the many tradeoffs, material considerations, and design tips and techniques that designers and design engineers need to know to succeed in this high-frequency realm.
- Articles
- Columns
- Links
- Media kit
||| MENU - design007 Magazine
Material Witness: Low-Flow Prepregs–Defining the Process
March 19, 2015 | Chet GuilesEstimated reading time: 5 minutes
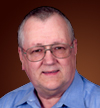
One of my favorite authors once wrote about perception: “For now we see in a mirror, dimly…” speaking in an era when mirrors were at best polished metal surfaces. In the infancy of low-flow products, we used to speak about “no-flow” prepregs as if “no-flow” was sufficient definition of the product, but as we have recently pointed out in our discussions of rheology, “everything flows.” And as we consider these increasingly essential but sometimes hard-to-define products, much consideration will have to be given to what the products need to do, how they do it, how we test them, what the testing means, and how or if the testing relates meaningfully to how the products work in a PWB rigid-flex production environment.
Let’s try to define “low flow” in terms that will make sense to both suppliers and users of the products. A low-flow prepreg is a prepreg that flows sufficiently to wet out and adhere to bonding surfaces and to fill inner layer copper details, but does not flow so much as to fill in cut-out areas in a heat sink or run unevenly out of the interface between rigid and flexible elements of a rigid-flex PWB. That being said, how to define that flow quantitatively and to control it in such a way that the resulting product has wide applicability in a variety of PWB heat-sink and rigid-flex designs has been an issue with both producers and users of the products since the introduction of the concept. (My personal involvement in low flow materials began in the Early Mesozoic Period.)
How low is low flow compared to “normal” prepregs? Figure 1, the chart labeled as 35N Rheology, and Figure 2, 47N Rheology, are respectively a standard polyimide prepreg—35N—with a minimum viscosity about 800 poise at heat-up rate 5oC/minute, and a standard epoxy low-flow product—47N—with a minimum viscosity about 8000 poise at heat-up rate of 5oC/minute. As you can see, the viscosity of the low-flow product is about an order of magnitude higher than that of the full-flow prepreg.
Note also that as the heat-up rate is adjusted, the minimum viscosity of the low-flow product behaves similar to that of a standard-flow resin. As the heat-up rate increases, the minimum melt viscosity is lower, and hence, the product will flow more, all other conditions being equal. If only it were practical to use a three-temperature ramp rate test to characterize low-flow products during manufacture!
Instead, we have an IPC test procedure (IPC TM-650 2.3.17.2) that defines low flow in terms of average reduction of the diameter of a cut-out circle when the material is tested under “standard” conditions of temperature and pressure. Page 1 of 2
Suggested Items
The Evolution of Picosecond Laser Drilling
06/19/2025 | Marcy LaRont, PCB007 MagazineIs it hard to imagine a single laser pulse reduced not only from nanoseconds to picoseconds in its pulse duration, but even to femtoseconds? Well, buckle up because it seems we are there. In this interview, Dr. Stefan Rung, technical director of laser machines at Schmoll Maschinen GmbH, traces the technology trajectory of the laser drill from the CO2 laser to cutting-edge picosecond and hybrid laser drilling systems, highlighting the benefits and limitations of each method, and demonstrating how laser innovations are shaping the future of PCB fabrication.
Day 2: More Cutting-edge Insights at the EIPC Summer Conference
06/18/2025 | Pete Starkey, I-Connect007The European Institute for the PCB Community (EIPC) summer conference took place this year in Edinburgh, Scotland, June 3-4. This is the third of three articles on the conference. The other two cover Day 1’s sessions and the opening keynote speech. Below is a recap of the second day’s sessions.
Day 1: Cutting Edge Insights at the EIPC Summer Conference
06/17/2025 | Pete Starkey, I-Connect007The European Institute for the PCB Community (EIPC) Summer Conference took place this year in Edinburgh, Scotland, June 3-4. This is the second of three articles on the conference. The other two cover the keynote speeches and Day 2 of the technical conference. Below is a recap of the first day’s sessions.
Preventing Surface Prep Defects and Ensuring Reliability
06/10/2025 | Marcy LaRont, PCB007 MagazineIn printed circuit board (PCB) fabrication, surface preparation is a critical process that ensures strong adhesion, reliable plating, and long-term product performance. Without proper surface treatment, manufacturers may encounter defects such as delamination, poor solder mask adhesion, and plating failures. This article examines key surface preparation techniques, common defects resulting from improper processes, and real-world case studies that illustrate best practices.
RF PCB Design Tips and Tricks
05/08/2025 | Cherie Litson, EPTAC MIT CID/CID+There are many great books, videos, and information online about designing PCBs for RF circuits. A few of my favorite RF sources are Hans Rosenberg, Stephen Chavez, and Rick Hartley, but there are many more. These PCB design engineers have a very good perspective on what it takes to take an RF design from schematic concept to PCB layout.