-
- News
- Books
Featured Books
- pcb007 Magazine
Latest Issues
Current IssueSales: From Pitch to PO
From the first cold call to finally receiving that first purchase order, the July PCB007 Magazine breaks down some critical parts of the sales stack. To up your sales game, read on!
The Hole Truth: Via Integrity in an HDI World
From the drilled hole to registration across multiple sequential lamination cycles, to the quality of your copper plating, via reliability in an HDI world is becoming an ever-greater challenge. This month we look at “The Hole Truth,” from creating the “perfect” via to how you can assure via quality and reliability, the first time, every time.
In Pursuit of Perfection: Defect Reduction
For bare PCB board fabrication, defect reduction is a critical aspect of a company's bottom line profitability. In this issue, we examine how imaging, etching, and plating processes can provide information and insight into reducing defects and increasing yields.
- Articles
- Columns
- Links
- Media kit
||| MENU - pcb007 Magazine
Splitting Hairs: The Manufacture of HDI and Substrate Test Fixtures
May 14, 2015 | Todd Kolmodin, Gardien ServicesEstimated reading time: 2 minutes
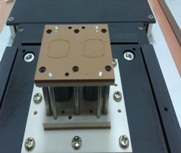
Testing of higher-density product has become ever more challenging with the advancement of chip technology. BGAs, CCDs and other active components have decreased in size so much that historical industry accepted test methodology can no longer effectively test these newer substrates incorporating this higher technology.
Universal grid test machines in North America, for the most part, are limited to single and double-density grids. Dedicated (wired) fixtures can combat some of the density issues faced in today’s test arena, but to successfully succeed in the high-volume demand market a test solution must be found to efficiently test the product and also provide automation to reduce cost.
Universal multi-plate fixtures routinely use test pins down to .3 mm. As pin size decreases, the need for extra plates in the fixture increases, so as to stabilize the pin and provide accurate loading of the pin. However, critical mass is soon reached as the fixture can no longer be solved due to inadequate grid contact availability. Further, as the density is maximized the fixture loses internal support and finally becomes unstable producing false defects, excessive troubleshooting and lost time.
Additionally, there is an ever-increasing demand for 4WK measurement especially on HDI boards, requiring two probes contacting the same pad simultaneously, which can only be tackled, especially for volume production, with this or similar technology.
HDI Fixtures vs. Substrate Fixtures
Quad and octal density universal equipment is used for standard HDI fixturing. Pin sizes for this type of fixturing are usually 90–110μm with a length of 20–30mm, therefore much smaller and shorter than standard universal grid fixtures.
To put this in to perspective the human hair has an average diameter of about 70μm (micron.) Pins in a substrate fixture of current generation typically are 70–50μm; the next generation under development will reach 40–25μm.
Substrate fixtures are typically not used with universal test machines. They require a much higher grid density; therefore the grid itself is generated as a wired solution either to standard connectors or to a universal one-touch interface depending on the final machine used.
HDI fixture usually test a complete test array, whereas substrate fixtures usually test only one or two images of the entire array and the machine will step the board through in multiple tests. That is mainly done to achieve the high accuracy required to test those kinds of boards and the extreme cost and time involved to make these fixture.
HDI fixture typically can be produced within 48 hours, the manufacturing time for a substrate fixture is usually 100–200 hours, and extreme cases can even take longer.
The manufacturing process for the substrate fixture is much more complex than the standard universal fixture. Accuracy is absolutely critical for the success of registering the product to the fixture.
There are basically six steps in the manufacturing process whether it is a hybrid design or a tension probe design:
1. DFM—Engineering
2. Drill
3. Electrode level—wiring, electroplating
4. Probe level—adding probes (wires)
5. Final assembly
6. Final QC and test setup
Editor's Note: This article originally appeared in the April issue of The PCB Magazine.
Suggested Items
TRI to Exhibit at SMTA Queretaro Expo 2025
07/16/2025 | TRITest Research, Inc. (TRI), the leading provider of test and inspection systems for the electronics manufacturing industry, is pleased to announce plans to exhibit at the SMTA Querétaro Expo 2025, scheduled to take place on July 24, 2025, at the Querétaro Centro de Congresos y Teatro Metropolitano.
Knocking Down the Bone Pile: Addressing End-of-life Component Solderability Issues, Part 4
07/16/2025 | Nash Bell -- Column: Knocking Down the Bone PileIn 1983, the Department of Defense identified that over 40% of military electronic system failures in the field were electrical, with approximately 50% attributed to poor solder connections. Investigations revealed that plated finishes, typically nickel or tin, were porous and non-intermetallic.
Meet the Author Podcast: Martyn Gaudion Unpacks the Secrets of High-Speed PCB Design
07/16/2025 | I-Connect007In this special Meet the Author episode of the On the Line with… podcast, Nolan Johnson sits down with Martyn Gaudion, signal integrity expert, managing director of Polar Instruments, and three-time author in I-Connect007’s popular The Printed Circuit Designer’s Guide to... series.
TTCI Joins Printed Circuit Engineering Association to Strengthen Design-to-Test Collaboration and Workforce Development
07/09/2025 | The Test Connection Inc.The Test Connection Inc. (TTCI), a leading provider of electronic test and manufacturing solutions, is proud to announce its membership in the Printed Circuit Engineering Association (PCEA), further expanding the company’s efforts to support cross-functional collaboration, industry standards, and technical education in the printed circuit design and manufacturing community.
Study on Resonance Mitigation in Metallic Shielding for Integrated Circuits
07/08/2025 | Maria Cuesta-Martin, Victor Martinez, Vidal Gonzalez Aguado, Würth ElektronikInherent cavity resonant modes often lead to significant degradation of shielding effectiveness, responsible for unwanted electromagnetic coupling. Cavity resonant modes of the metal shielding enclosure can produce two adverse problems: the mutual coupling among different RF modules and shielding effectiveness reduction of the metal enclosure. The cabinets serve to shield certain components from electromagnetic interference (EMI). However, these cavities present some resonance peaks at 5 GHz, making it impossible to use them at higher frequencies.