-
- News
- Books
Featured Books
- design007 Magazine
Latest Issues
Current IssueShowing Some Constraint
A strong design constraint strategy carefully balances a wide range of electrical and manufacturing trade-offs. This month, we explore the key requirements, common challenges, and best practices behind building an effective constraint strategy.
All About That Route
Most designers favor manual routing, but today's interactive autorouters may be changing designers' minds by allowing users more direct control. In this issue, our expert contributors discuss a variety of manual and autorouting strategies.
Creating the Ideal Data Package
Why is it so difficult to create the ideal data package? Many of these simple errors can be alleviated by paying attention to detail—and knowing what issues to look out for. So, this month, our experts weigh in on the best practices for creating the ideal design data package for your design.
- Articles
- Columns
- Links
- Media kit
||| MENU - design007 Magazine
Material Witness: How About that Technical Roadmap!
May 15, 2015 | Chet GuilesEstimated reading time: 4 minutes
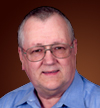
You may remember the movie What About Bob? If you do, you may recall the scene in which Bob (played by Bill Murray) confronts his psychiatrist (played by Richard Dreyfuss) and emotes, “I need! I need! I need! Gimme! Gimme! Gimme!”
As I thought recently about some of the drivers that IPC and others have incorporated into their technical roadmaps (not that they all are new by any means, but each time they come out, some of the technical parameters are squeezed a bit harder) I feel a bit like that befuddled psychiatrist. It’s tough figuring out how to make materials that meet all the “I need!” and “Gimme!” requirements and drivers while still satisfying the UMS (Universal Material Specification): “Low dielectric constant, low loss, high performance and free.”
Consider just a few of the obvious considerations:
- Thermal dissipation increasingly drives design.
- Maximum board operating temperatures are rising (watt density).
- IC’s are going 3D resulting in much higher density devices.
- Fine line/space circuitry will continue to be critical as HDI demands increase.
- Mechanical drilling is being challenged for both through holes and buried/blind vias.
- Micro via technology and laser drilling will continue to push for smaller diameters.
- Higher frequencies are increasingly necessary as transmitted data volume increases.
- Enhanced glass styles (flat glass) will help signal stability at microwave frequencies.
- Land diameters will shrink as device I/O density increases.
- Registration on larger panels (fine lines and small lands) will increasingly be an issue.
- “Green” requirements will continue to be pushed – albeit at the “right price.”
- The percentage of assembled PWBs required to be recyclable will increase.
- Dielectric properties will be increasingly important as frequencies rise.
- Digital and RF/microwave materials will converge with conventional materials.
- Data demand will push the limits of current 3G and 4G build-outs (resulting in more HDI demand and at higher frequencies).
There are a variety of design, material and manufacturability issues that these tightening requirements should suggest to PWB raw material suppliers. Just a few:
- Thermally conductive materials will continue to become a greater part of the PWB package. Heat sinks alone will no longer do the whole job as density of device mounting becomes greater and greater, and consumers want an infinite amount of functionality in smaller and smaller packages. (My maturing—i.e., old—eyes already revolt at the idea of watching streaming movies on a 4 cm x 6 cm screen however HD the resolution may be.) Keeping device temperatures down becomes critical, as every 10oC of lowered temperature doubles the mean time between failures (MTBF). Thermally conductive microwave and RF materials will also find increasing usage as less thermal variability at the device level means more signal stability.
- The implications in building multilayer microchip IC’s are also huge, in that the density of features on a PWB will increase substantially (all that functionality eventually needs to reach the real world of people with large (relative to the IC anyway) hands and the need for stuff they can handle. My 17-year-old granddaughter texts at about a gazillion wpm, but my old, larger fingers have trouble touching only one of those little bitty keys at a time. And we want things smaller still? (Maybe voice- or thought-activated electronics will eventually allow some of these barriers to be eliminated.) One of the obvious implications of increasing HDI on PWBs is that registration, always an issue with lots of holes in large panel sizes will become a bigger gorilla. This will become even more critical as land sizes and hole diameters shrink, and more and thinner layers are needed to get the necessary signal density.
- Environmental issues, whatever any of us may think about the validity of the science behind some of the evolving requirements, will continue to require material suppliers to produce products that are “greener” (that is, having low levels of halogens and other banned chemicals) and more environmentally sustainable (including recycling, recovery of metals, recovery of energy from hydrocarbon based components, etc.). That includes finding sustainable substitutes for traditional brominated flame retardants and developing low cost materials that will survive in lead-free soldering environments. What solder systems may eventually become “standard” is not yet clear, but I have a sort of back of my mind worry that my new $2,500 Mitsubishi 3D HDTV will suddenly go “poof” and shut down because of tin whisker growth from the “environmentally safe” solder being used. The military OEMs are leery of newer solders for several reasons. All of us in the materials business need to wonder if the improved solutions to green and environmental issues have longer term issues (technical and political) we haven’t even considered yet. Are phosphorus-based flame retardants actually safer than halogens?
- The basic multilayer PWB is not going to go away soon. It remains needed to connect all this incredible functionality to the real world in packages that are suitable for human interconnection. When we get microchip ICs implanted in our brains that can project info into our ears and eyeballs directly (a super Google Glass?) and interconnect via microwaves with equally small chips in desktop computers that can be a few cubic inches in size, then maybe the PWB will start to fade away. But for now we need to interact with a technologically very adaptive world by tuning materials to the current needs set.
The “needs” and “gimmes” will never go away, and hopefully there will be common sense applied at the government regulatory level in the U.S. and elsewhere, though common sense and government sometimes to be antithetical. But as a materials guy, I see the challenges of the early 21st century demanding that we continue to evolve better and more cost effective materials, and to fine tune the ones we have. Our success at being flexible and adaptable will be a major definer of our success in the next few interesting years.
Chet Guiles is a consultant for Arlon Electronic Materials Division.
Suggested Items
SHENMAO Strengthens Semiconductor Capabilities with Acquisition of PMTC
07/10/2025 | SHENMAOSHENMAO America, Inc. has announced the acquisition of Profound Material Technology Co., Ltd. (PMTC), a premier Taiwan-based manufacturer of high-performance solder balls for semiconductor packaging.
KYZEN to Highlight Understencil and PCB Cleaners at SMTA Querétaro Expo and Tech Forum
07/09/2025 | KYZEN'KYZEN, the global leader in innovative environmentally responsible cleaning chemistries, will exhibit at the SMTA Querétaro Expo & Tech Forum, scheduled to take place Thursday, July 24, at Centro de Congresos y Teatro Metropolitano de Querétaro.
Driving Innovation: Direct Imaging vs. Conventional Exposure
07/01/2025 | Simon Khesin -- Column: Driving InnovationMy first camera used Kodak film. I even experimented with developing photos in the bathroom, though I usually dropped the film off at a Kodak center and received the prints two weeks later, only to discover that some images were out of focus or poorly framed. Today, every smartphone contains a high-quality camera capable of producing stunning images instantly.
Hands-On Demos Now Available for Apollo Seiko’s EF and AF Selective Soldering Lines
06/30/2025 | Apollo SeikoApollo Seiko, a leading innovator in soldering technology, is excited to spotlight its expanded lineup of EF and AF Series Selective Soldering Systems, now available for live demonstrations in its newly dedicated demo room.
Indium Corporation Expert to Present on Automotive and Industrial Solder Bonding Solutions at Global Electronics Association Workshop
06/26/2025 | IndiumIndium Corporation Principal Engineer, Advanced Materials, Andy Mackie, Ph.D., MSc, will deliver a technical presentation on innovative solder bonding solutions for automotive and industrial applications at the Global Electronics A