-
- News
- Books
Featured Books
- pcb007 Magazine
Latest Issues
Current IssueThe Hole Truth: Via Integrity in an HDI World
From the drilled hole to registration across multiple sequential lamination cycles, to the quality of your copper plating, via reliability in an HDI world is becoming an ever-greater challenge. This month we look at “The Hole Truth,” from creating the “perfect” via to how you can assure via quality and reliability, the first time, every time.
In Pursuit of Perfection: Defect Reduction
For bare PCB board fabrication, defect reduction is a critical aspect of a company's bottom line profitability. In this issue, we examine how imaging, etching, and plating processes can provide information and insight into reducing defects and increasing yields.
Voices of the Industry
We take the pulse of the PCB industry by sharing insights from leading fabricators and suppliers in this month's issue. We've gathered their thoughts on the new U.S. administration, spending, the war in Ukraine, and their most pressing needs. It’s an eye-opening and enlightening look behind the curtain.
- Articles
- Columns
- Links
- Media kit
||| MENU - pcb007 Magazine
Practical Application of Lean Six Sigma to Drive Cycle Time Reduction, Part 1
October 22, 2015 | Kathy Nargi-Toth, NCAB Group USA Inc.Estimated reading time: 2 minutes
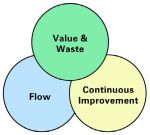
One of the most systematic and successful approaches to the challenge of cycle time reduction can be found in the principles and tools of lean six-sigma methodology. The success of this strategy requires commitment. It is not a quick fix, nor will it be effective if it is only used as an occasional housecleaning activity. To be successful requires a long-term commitment of time and resources and a tireless dedication to improvement. As a result you should expect and welcome change as your company focuses from inward (my product) to outward (my customer), with a goal of total customer satisfaction. It's a win-win solution.
Some might argue that Walter Shewhart was the inspiration for the concept of six sigma. It was Shewhart who in the 1920s identified common and special cause process change and introduced the control chart. The credit however for the term "six sigma" is given to Bill Smith and co-founder Dr. Mikel Harry of Motorola. In the mid-1980s, Motorola CEO Bob Galvin supported a quality initiative based on six sigma methodologies that changed the way Motorola did business, which improved quality, increased customer satisfaction and ultimately saved hundreds of millions of dollars in the process.
Motorola's six sigma concept began with four basic principles: measure, analyze, improve, control (MAIC). The D (define) of DMAIC was added later by GE. Today, six sigma includes lean principles as well as methods that introduce six sigma earlier into the design phase of the process, which enables faster time-to-market with products that better meet the customers’ specific requirements. By using six sigma principles and lean techniques together, PCB manufacturers can reduce both process variation and cycle time together effectively.
Getting Started
The PCB manufacturing process is by nature a batch process, following a predetermined sequence that is developed to meet the products’ specific design requirements. In PCB manufacturing not all products go through the exact same process, which complicates the task of cycle time reduction. As an example, a standard multilayer board will probably not be laser-drilled or plasma-etched unless it has some very unique characteristics. And HDI products may cycle through lamination, drilling, laser drilling, plating and etching two or more times before moving on to solder mask application. Cycle time reduction efforts for these two products will require individual evaluation.
Editor's Note: This article originally appeared in the October 2015 issue of SMT Magazine.
Suggested Items
SHENMAO Strengthens Semiconductor Capabilities with Acquisition of PMTC
07/10/2025 | SHENMAOSHENMAO America, Inc. has announced the acquisition of Profound Material Technology Co., Ltd. (PMTC), a premier Taiwan-based manufacturer of high-performance solder balls for semiconductor packaging.
KYZEN to Highlight Understencil and PCB Cleaners at SMTA Querétaro Expo and Tech Forum
07/09/2025 | KYZEN'KYZEN, the global leader in innovative environmentally responsible cleaning chemistries, will exhibit at the SMTA Querétaro Expo & Tech Forum, scheduled to take place Thursday, July 24, at Centro de Congresos y Teatro Metropolitano de Querétaro.
Driving Innovation: Direct Imaging vs. Conventional Exposure
07/01/2025 | Simon Khesin -- Column: Driving InnovationMy first camera used Kodak film. I even experimented with developing photos in the bathroom, though I usually dropped the film off at a Kodak center and received the prints two weeks later, only to discover that some images were out of focus or poorly framed. Today, every smartphone contains a high-quality camera capable of producing stunning images instantly.
Hands-On Demos Now Available for Apollo Seiko’s EF and AF Selective Soldering Lines
06/30/2025 | Apollo SeikoApollo Seiko, a leading innovator in soldering technology, is excited to spotlight its expanded lineup of EF and AF Series Selective Soldering Systems, now available for live demonstrations in its newly dedicated demo room.
Indium Corporation Expert to Present on Automotive and Industrial Solder Bonding Solutions at Global Electronics Association Workshop
06/26/2025 | IndiumIndium Corporation Principal Engineer, Advanced Materials, Andy Mackie, Ph.D., MSc, will deliver a technical presentation on innovative solder bonding solutions for automotive and industrial applications at the Global Electronics A