-
- News
- Books
Featured Books
- design007 Magazine
Latest Issues
Current IssueShowing Some Constraint
A strong design constraint strategy carefully balances a wide range of electrical and manufacturing trade-offs. This month, we explore the key requirements, common challenges, and best practices behind building an effective constraint strategy.
All About That Route
Most designers favor manual routing, but today's interactive autorouters may be changing designers' minds by allowing users more direct control. In this issue, our expert contributors discuss a variety of manual and autorouting strategies.
Creating the Ideal Data Package
Why is it so difficult to create the ideal data package? Many of these simple errors can be alleviated by paying attention to detail—and knowing what issues to look out for. So, this month, our experts weigh in on the best practices for creating the ideal design data package for your design.
- Articles
- Columns
- Links
- Media kit
||| MENU - design007 Magazine
Mark Thompson: It’s All About Communication
March 13, 2016 | Barry Matties and Andy Shaughnessy, I-Connect007Estimated reading time: 11 minutes
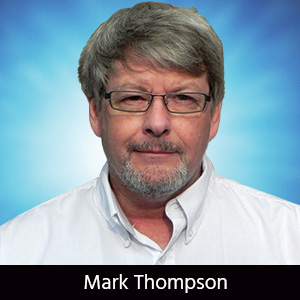
In engineering support at Prototron Circuits, Mark Thompson has seen it all. He ensures that each design is manufactured the way the designer intended, even if the CAD data is not crystal clear. During DesignCon, Barry Matties and Andy Shaughnessy talked with Thompson about why communication is paramount when designing and prototyping boards. Thompson also explained how designers can avoid making common mistakes that can set back an entire project.
Barry Matties: Mark, tell us a little bit about Prototron and what you do.
Mark Thompson: I do most of the pre-engineering/ signal integrity calculations for the Redmond facility. And when it comes to some nitty gritty stuff like strange communication issues or signal integrity issues and those types of things, I'm typically the guy that customers talk to. We’ve been in business now for 27 years. We are a debt-free company. We have heard some really fantastic testimonials just at this show alone. Our owner, Dave Ryder, was on a plane flying here, and engaged with the man sitting next to him. She said, “Oh, I work with Prototron. We love you. Everybody in the Seattle area knows you and utilizes you.” That's a nice thing to hear, and when we got here we had another guy from Silicon Valley say virtually the same thing. “Of course. I know you guys. Good company.”
Matties: You have two locations?
Thompson: Yes, one in Tucson, Arizona, and the other is in Redmond, Washington. We always talk about this—I think we may have even mentioned this in interviews past. If you can, imagine the environmental conditions of those two shops. I've got one dry and hot environment, and I have a humid and cold environment. We're trying to maintain press parameters for environmental conditions to make sure there are dielectric constants, loss tangents, and nesting values for the prepregs all jibe, based on the prepregs that we use at both facilities. With those kinds of environmental conditions, that's a real tough one.
Andy Shaughnessy: Interesting. How is Tucson doing by the way?
Thompson: They are doing really well. One of the things we did was hire Mike Graves, to run our production down there and he has done a great job with the Tucson facility and he's really made things happen for them. They're actually working with some materials that we're currently not working with in Redmond, and that's fantastic. More power to them.
Matties: Is your discipline primarily process engineering?
Thompson: My discipline is more signal integrity. My day is filled with people calling me and saying, “Mark, I have a 12-layer board. I have impedances on layers 1, 3, 4, 7, 8, 9, 11, and 12 and I need 50 ohms, 100 ohms, or 120 ohms,” and that's when a series of questions happens. That's when I start digging in and saying, “Okay, let's talk about this. What material do you want to do this on? What are the copper weights that you want? Will you have any co-planar coupling that will affect my impedances? Bear in mind, if I'm going to do 11 different calculations for you, I'm going to want to know up front if you're going to do co-planar coupling, because I don't want to redo those again when the job comes in.” I can't tell you how many times and how frequently that happens.
Honestly, we'll have a guy call and he'll say, “I've got an eight-layer board. I've got impendences on layers 1, 3, 6, and 8, and I want 50 ohms and 100 ohms.” I'll say, “Okay, here are your calculations. These are all predicated in free space. There is no co-planar coupling.” In the meantime, the engineers looked over his shoulder and said, “You know what? This is a mess. We're going to have a ton of emissions here. I want you to pour copper on all those layers within .005 inch of those impedance traces.” He has now induced co-planar coupling, which has changed my calculations. Now it comes in as a three-day turn and I've got to redo the whole thing all over again. Communication is really key.
Matties: That really was the impetus for this interview. That it's all about communication.
Thompson: Absolutely. This morning I had a great example of that. A customer asked us for something that starts out fairly simple. He wanted something like 45 ohm and 50 ohm single-ended calculations on X layers. We send a stack-up and the calculations and tell him that these are based on them being in free space, that there is no co-planar coupling whatsoever. The job comes in. Now it's an expedite and guess what? It no longer has just singled-ended entities; it has differential pairs and they've used the same size for the differential pairs as they have the single-ended entities. This puts the onus on the fabricator to be able to differentiate between those singled-ended entities and those differential pairs. That can be really problematic and that's a huge liability. What if we miss a differential pair? What have I advised in the past in my column The Bare (Board) Truth? Make them a 10th or a 100th of a mil different from the other entities.
If you've got a single-ended trace that's five mils, make your differentials .00501 or .005001. Those are not numbers that a fabricator can resolve. We can't resolve a 1,000th of a mil, but it's a clue to the CAD operator that this is a differential pair. Look at me. Deal with me properly so that I can make sure your impedance is correct.
In addition to that, this particular customer changed the configuration. They added copper pour and changed all the scenarios. Originally, my calculations were for single-ended entities on layers 4 and 5, using layers 3 and 6 as the reference planes. When they poured copper on all the layers, guess what? They turned them from dual asymmetric striplines into striplines. They've not only changed all of that, but now we're going to have to reduce the line sizes potentially down to a point where we have to ask for 15%. You don't want to do that.
Matties: Don't the designers know their job? [laughter] I say that tongue in cheek, but there's some legitimacy in that question.
Thompson: You'd be surprised at what level and at what companies you have those sorts of issues. I think that's really been because at one point in the big downturn, everybody had a whole group of people doing a whole slew of tasks. We had design folks. We had engineers. We had layout people. We had schematic capture people. We had all these different people, and now all of those people are rolled into the same guy, and he needs to learn all of those things. These are those kinds of things that he may not be aware of. He may not be aware that when you're mixing dielectrics, you run into these kinds of issues.
Shaughnessy: It seems like the designers have to deal with more engineering problems now, but some of them actually want to know why. Instead of throwing a capacitor on it and going home, they say, “Run a model, or find out what's going on behind the scenes instead of just throwing a quick fix on it.”
Thompson: Exactly. In fact, a lot of our customers actually really like us because one of the things I try to do is explain why I'm asking what I'm asking. It's really a jeopardy for them. We're trying to save them some grief down the road when they go someplace else and they just have it built verbatim, without any additional information. All of a sudden, they get a whole bunch of doorstops back and they call me, and they say, “Mark, I got 500 doorstops from Korea. Why are these different than what you have?” and I have to explain. It happens.
Matties: What's the answer? How do we make the design pool smarter, stronger, and more capable?
Thompson: Communication.
Matties: Isn't it too late at that point, realistically?
Thompson: Sometimes it is. That's a really good point, Barry, because think about the industry and the way it's become. There is very little direct interaction now. If I can call the engineer or the designer directly, it is so much better, because I can get through the problem. But we're going through contract manufacturers quite often, so now we have a third party involved and we're obligated to involve them and then they go back to the customer and that may take a modicum of time. In the meantime, this three-day turn has now lost all its time.
Matties: Who absorbs the cost? There's no time to do it right, but plenty of time to do it over? Who pays for the do-over of a bad design?
Thompson: That's a very good question, because it happens so frequently.
Matties: Because what you described in the earlier scenario is you get a design in, the design is poor and you catch it, but all of that time is wasted because the design came in poor. One bad design can cost your team 20–30 hours when you really start adding it up. Those are 20–30 hours you don't get back and you're not billing for.Page 1 of 2
Suggested Items
Copper Price Surge Raises Alarms for Electronics
07/15/2025 | Global Electronics Association Advocacy and Government Relations TeamThe copper market is experiencing major turbulence in the wake of U.S. President Donald Trump’s announcement of a 50% tariff on imported copper effective Aug. 1. Recent news reports, including from the New York Times, sent U.S. copper futures soaring to record highs, climbing nearly 13% in a single day as manufacturers braced for supply shocks and surging costs.
I-Connect007 Editor’s Choice: Five Must-Reads for the Week
07/11/2025 | Andy Shaughnessy, Design007 MagazineThis week, we have quite a variety of news items and articles for you. News continues to stream out of Washington, D.C., with tariffs rearing their controversial head again. Because these tariffs are targeted at overseas copper manufacturers, this news has a direct effect on our industry.I-Connect007 Editor’s Choice: Five Must-Reads for the Week
Digital Twin Concept in Copper Electroplating Process Performance
07/11/2025 | Aga Franczak, Robrecht Belis, Elsyca N.V.PCB manufacturing involves transforming a design into a physical board while meeting specific requirements. Understanding these design specifications is crucial, as they directly impact the PCB's fabrication process, performance, and yield rate. One key design specification is copper thieving—the addition of “dummy” pads across the surface that are plated along with the features designed on the outer layers. The purpose of the process is to provide a uniform distribution of copper across the outer layers to make the plating current density and plating in the holes more uniform.
Trump Copper Tariffs Spark Concern
07/10/2025 | I-Connect007 Editorial TeamPresident Donald Trump stated on July 8 that he plans to impose a 50% tariff on copper imports, sparking concern in a global industry whose output is critical to electric vehicles, military hardware, semiconductors, and a wide range of consumer goods. According to Yahoo Finance, copper futures climbed over 2% following tariff confirmation.
Happy’s Tech Talk #40: Factors in PTH Reliability—Hole Voids
07/09/2025 | Happy Holden -- Column: Happy’s Tech TalkWhen we consider via reliability, the major contributing factors are typically processing deviations. These can be subtle and not always visible. One particularly insightful column was by Mike Carano, “Causes of Plating Voids, Pre-electroless Copper,” where he outlined some of the possible causes of hole defects for both plated through-hole (PTH) and blind vias.