-
- News
- Books
Featured Books
- pcb007 Magazine
Latest Issues
Current IssueThe Hole Truth: Via Integrity in an HDI World
From the drilled hole to registration across multiple sequential lamination cycles, to the quality of your copper plating, via reliability in an HDI world is becoming an ever-greater challenge. This month we look at “The Hole Truth,” from creating the “perfect” via to how you can assure via quality and reliability, the first time, every time.
In Pursuit of Perfection: Defect Reduction
For bare PCB board fabrication, defect reduction is a critical aspect of a company's bottom line profitability. In this issue, we examine how imaging, etching, and plating processes can provide information and insight into reducing defects and increasing yields.
Voices of the Industry
We take the pulse of the PCB industry by sharing insights from leading fabricators and suppliers in this month's issue. We've gathered their thoughts on the new U.S. administration, spending, the war in Ukraine, and their most pressing needs. It’s an eye-opening and enlightening look behind the curtain.
- Articles
- Columns
- Links
- Media kit
||| MENU - pcb007 Magazine
Happy’s Essential Skills: Design of Experiments
March 17, 2016 | Happy HoldenEstimated reading time: 9 minutes
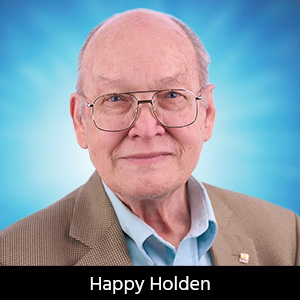
Design of experiments (DOE) is one of the most powerful and influential engineering tools for product yield improvements, new products or processes development, or for problem solving. As mentioned in my last column, process problems led me to a career in printed circuits, and quickly solving those problems led me to a bonus stock award and a great life. Even though I knew nothing about printed circuit manufacturing processes, I was able to quickly find the root causes of all the problems and fix them. My secret? Total quality control (TQC), statistics, and DOE.
Experimentation is the manipulation of controllable factors at different values to see their effect on some desired result. An engineer can use three methods of experimentation:
- Trial and error
- One factor at a time
- Design of experiments
Trial and Error
Hopefully a trained engineer will not use this technique. But in the rush to fix the problem, one might think they know the true root cause and start changing parameters. In my case, I didn’t know the parameters so first I talked to the other engineers, line-workers and supervisors and created a pareto of possible causes. Then I called the chemical suppliers and asked them what they thought was important. Lastly, I went to the industry bible, the Printed Circuit Handbook by Clyde Coombs, and read what it had to say. From this list I got an inkling of what the possible causes could be.
One Factor at a Time
The objective of any experiment is to establish a probable cause-and-effect relationship. The common sense approach is to make trial changes of the most likely factors contributing to the observed problem, keeping all other contributor variables constant during the experiment, and then seeing if a significant correlation can be established between the suspected cause and the effect. If the experiment with the factor chosen gives no conclusive results, the next most likely factor is tried in the same way. Although this experimental strategy sounds logical, as you can see in Figure 1, it tests only a part of the process matrix and only what you know (variables X1, X2 and X3 and changing one at a time from -1 to +1 levels). Four steps are involved in this process:
- Observation: Study all phases of the situation in which the effect to be controlled occurs.
- Reflection: Try to think of all the causes which might influence this effect. Consult with others who have had experience with this or similar situations.
- Trial: Try the influence of the most likely factor; if not successful, try the next most likely one, and so on.
- Check: With a purported relationship established, attempt to turn the effect on and off, like a water faucet, by varying the suspected cause back and forth between its different levels.
The common sense approach is always recommended as a first try. It is fast and cheap when it works— as it often does for confirming single or independent factors whose presence can be logically suspected. However, when it has been tried several times on a problem with no clear cut solution emerging, a more sophisticated approach is called for—that of statistical experimentation.
This was the situation when asked to help the printed circuit plant. Months of tests and experimentation had not resulted in finding a cause for the problems and the solution.
Figure 1: Experimental methods: Can be trial and error or factorial design of experiments (DOE) that is much more comprehensive and effective than one-factor-at-a-time method. The DOE software can be found in The NIST/SEMETECH e-Handbook of Statistical Methods[1].
Page 1 of 3
Suggested Items
DownStream Acquisition Fits Siemens’ ‘Left-Shift’ Model
06/26/2025 | Andy Shaughnessy, I-Connect007I recently spoke to DownStream Technologies founder Joe Clark about the company’s acquisition by Siemens. We were later joined by A.J. Incorvaia, Siemens’ senior VP of electronic board systems. Joe discussed how he, Rick Almeida, and Ken Tepper launched the company in the months after 9/11 and how the acquisition came about. A.J. provides some background on the acquisition and explains why the companies’ tools are complementary.
Elementary Mr. Watson: Retro Routers vs. Modern Boards—The Silent Struggle on Your Screen
06/26/2025 | John Watson -- Column: Elementary, Mr. WatsonThere's a story about a young woman preparing a holiday ham. Before putting it in the pan, she cuts off the ends. When asked why, she shrugs and says, "That's how my mom always did it." She asks her mother, who gives the same answer. Eventually, the question reaches Grandma, who laughs and says, "Oh, I only cut the ends off because my pan was too small." This story is a powerful analogy for how many PCB designers approach routing today.
Siemens Turbocharges Semiconductor and PCB Design Portfolio with Generative and Agentic AI
06/24/2025 | SiemensAt the 2025 Design Automation Conference, Siemens Digital Industries Software today unveiled its AI-enhanced toolset for the EDA design flow.
Cadence AI Autorouter May Transform the Landscape
06/19/2025 | Andy Shaughnessy, Design007 MagazinePatrick Davis, product management director with Cadence Design Systems, discusses advancements in autorouting technology, including AI. He emphasizes a holistic approach that enhances placement and power distribution before routing. He points out that younger engineers seem more likely to embrace autorouting, while the veteran designers are still wary of giving up too much control. Will AI help autorouters finally gain industry-wide acceptance?
Beyond Design: The Metamorphosis of the PCB Router
06/18/2025 | Barry Olney -- Column: Beyond DesignThe traditional PCB design process is often time-consuming and labor-intensive. Routing a complex PCB layout can consume up to 30% of a designer’s time, and addressing this issue is not straightforward. We have all encountered this scenario: You spend hours setting the constraints and finally hit the Go button, only to be surprised by the lack of visual appeal and the obvious flaws in the result.