-
- News
- Books
Featured Books
- pcb007 Magazine
Latest Issues
Current IssueSales: From Pitch to PO
From the first cold call to finally receiving that first purchase order, the July PCB007 Magazine breaks down some critical parts of the sales stack. To up your sales game, read on!
The Hole Truth: Via Integrity in an HDI World
From the drilled hole to registration across multiple sequential lamination cycles, to the quality of your copper plating, via reliability in an HDI world is becoming an ever-greater challenge. This month we look at “The Hole Truth,” from creating the “perfect” via to how you can assure via quality and reliability, the first time, every time.
In Pursuit of Perfection: Defect Reduction
For bare PCB board fabrication, defect reduction is a critical aspect of a company's bottom line profitability. In this issue, we examine how imaging, etching, and plating processes can provide information and insight into reducing defects and increasing yields.
- Articles
- Columns
- Links
- Media kit
||| MENU - pcb007 Magazine
All About Flex: Taguchi Design of Experiments and Flexible Circuits
July 14, 2016 | Dave Becker, All FlexEstimated reading time: 4 minutes
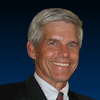
Reducing variability in a process, or a sequence of processes, can require a significant and structured amount of work and analysis. One must develop an understanding of critical variables and determine methods to control them. Statistically based experiments are often needed for proper analysis.
Classical Design of Experiments
One strategy is to use classical design of experiments (DOE).
With DOE, the technical team needs to first identify variables that are suspected to have a significant impact on the output. With best estimates of critical variables, the methodology then defines a high point and low of each identified variable. Variables don’t necessarily fall into “high” and “low” categories. They may include options like bake or no bake, alternative surface finishes, material types, etc. A series of experimental runs are designed that have variables run at the high point and a low point in combination with all the other variables low and high. The output of the experiment (i.e., the consequence of the variety of inputs), is best if it can be defined numerically.
The table below illustrates a simple two variable experimental design.
The design above is called full factorial because every combination of high and low variables is run. Of course with two variables, only four experimental runs are required to test every combination of high and low. For three variables, eight or 23 runs are required. A four-variable experiment would require 16 unique runs.
A key requirement for proper experimental design is to randomize the experimental order. This avoids results being contaminated by other conditions that were not controlled during the experiment. Randomizing the order of runs reduces the risk of built in experimental bias confounding the results.
A full factorial experiment provides the main effects of each variable plus all the interaction effects.
Designed experiments are valuable, but disruptive for three primary reasons:
- They should be performed on production equipment
- Proper examination of variables may involve a large number of experiments; if six variables are to be examined, a full factorial experiment would require 64 different runs
- Randomization adds set-up times and cost in a highly capitalized production environment
A more realistic type of DOE is called fractional factorial. Fractional factorial experiments are designed to only find out the main effects and major interactions; as such, they require fewer runs. Many good reference documents are available to assist with DOE layout, statistical interpretation, and factorial design.
Taguchi Design of Experiments
Taguchi design of experiments is a variation of fractional factorial experiments, but with a one major difference. It addresses the fact that it is not realistic to control every single variable that might affect the process. Outside temperature, humidity, time of day, raw material supplier and operator are just a few examples of variables that are either impossible or highly impractical to control. If the experiments are being done in production, they may need to be spread out over several weeks so production schedules can be accommodated. Randomizing the experiment in a full scale production environment is often prohibitively expensive.
The Taguchi method allows for the reality faced when conducting designed experiments in production: it is often not practical to properly randomize an experiment. So in addition to all the critical variables tested, another variable, noise, is allowed and defined. The noise contains all the variables that are not controlled. The high level might be the noise variables set at one realistic extreme and the low level might be all the noise variables set the other realistic extreme. One of the goals of the experiment is to determine what variables and variable settings yield the most robust results. These are settings where there is zero interaction effect with the noise variable.
Page 1 of 2
Suggested Items
I-Connect007 Editor’s Choice: Five Must-Reads for the Week
07/18/2025 | Nolan Johnson, I-Connect007It may be the middle of the summer, but the news doesn’t quit, and there’s plenty to talk about this week, whether you’re talking technical or on a global scale. When I have to choose six items instead of my regular five, you know it’s good. I start by highlighting my interview with Martyn Gaudion on his latest book, share some concerning tariff news, follow that up with some promising (and not-so-promising) investments, and feature a paper from last January’s inaugural Pan-European Design Conference.
Elephantech Launches World’s Smallest-Class Copper Nanofiller
07/17/2025 | ElephantechJapanese deep-tech startup Elephantech has launched its cutting-edge 15 nm class copper nanofiller – the smallest class available globally. This breakthrough makes Elephantech one of the first companies in the world to provide such advanced material for commercial use.
Copper Price Surge Raises Alarms for Electronics
07/15/2025 | Global Electronics Association Advocacy and Government Relations TeamThe copper market is experiencing major turbulence in the wake of U.S. President Donald Trump’s announcement of a 50% tariff on imported copper effective Aug. 1. Recent news reports, including from the New York Times, sent U.S. copper futures soaring to record highs, climbing nearly 13% in a single day as manufacturers braced for supply shocks and surging costs.
I-Connect007 Editor’s Choice: Five Must-Reads for the Week
07/11/2025 | Andy Shaughnessy, Design007 MagazineThis week, we have quite a variety of news items and articles for you. News continues to stream out of Washington, D.C., with tariffs rearing their controversial head again. Because these tariffs are targeted at overseas copper manufacturers, this news has a direct effect on our industry.I-Connect007 Editor’s Choice: Five Must-Reads for the Week
Digital Twin Concept in Copper Electroplating Process Performance
07/11/2025 | Aga Franczak, Robrecht Belis, Elsyca N.V.PCB manufacturing involves transforming a design into a physical board while meeting specific requirements. Understanding these design specifications is crucial, as they directly impact the PCB's fabrication process, performance, and yield rate. One key design specification is copper thieving—the addition of “dummy” pads across the surface that are plated along with the features designed on the outer layers. The purpose of the process is to provide a uniform distribution of copper across the outer layers to make the plating current density and plating in the holes more uniform.