-
- News
- Books
Featured Books
- pcb007 Magazine
Latest Issues
Current IssueThe Hole Truth: Via Integrity in an HDI World
From the drilled hole to registration across multiple sequential lamination cycles, to the quality of your copper plating, via reliability in an HDI world is becoming an ever-greater challenge. This month we look at “The Hole Truth,” from creating the “perfect” via to how you can assure via quality and reliability, the first time, every time.
In Pursuit of Perfection: Defect Reduction
For bare PCB board fabrication, defect reduction is a critical aspect of a company's bottom line profitability. In this issue, we examine how imaging, etching, and plating processes can provide information and insight into reducing defects and increasing yields.
Voices of the Industry
We take the pulse of the PCB industry by sharing insights from leading fabricators and suppliers in this month's issue. We've gathered their thoughts on the new U.S. administration, spending, the war in Ukraine, and their most pressing needs. It’s an eye-opening and enlightening look behind the curtain.
- Articles
- Columns
- Links
- Media kit
||| MENU - pcb007 Magazine
Happy’s Essential Skills: CIM and Automation Planning, Part 1
August 31, 2016 | Happy HoldenEstimated reading time: 13 minutes
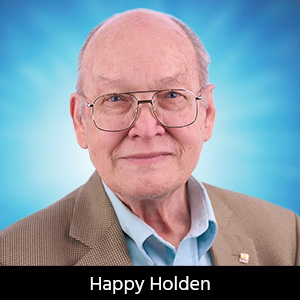
There is a lot of talk and even information about automation, but I find that there is very little available on automation planning. This is one of my specialties. I started by getting a master's in EE in control theory. This went well with my B.S. in chemical engineering as I specialized in process control and IC manufacturing. This is one reason I took my first job at Hewlett-Packard; they wanted to automate the IC production, even back in 1970. I discovered then that there were a lot of companies offering equipment and software, but not a strategy on “How to Automate!” So working with HP Labs, we developed a ‘methodology’ that has worked for HP very well over the years. In my next column, I will focus on computer-aided-manufacturing and the connectivity issues with different protocols available.
However, the benefits will be derived only if certain cardinal principles are observed. This column outlines, briefly, the background of computer-integrated-manufacturing (CIM) and six of those automation principles: Superiority, Simplicity, Flexibility, Compatibility, Manufacturability, and Reliability.
Introduction
The consistent characteristic of successful application of automation in manufacturing has been the degree to which business and technical management understands and promotes the strategies, tactics, and philosophies used in modern manufacturing. By reviewing these philosophies of CIM, automation, management roles, mechanization, SPC, TQC, LEAN, MRP and Design for Manufacturing the successful implementation of automation in any company, small as well as large, will be enhanced.
Computer Integrated Manufacturing (CIM)
The strategies outlined here are considered CIM. HP was once in the business of selling CIM and called it “The Manufacturers Productivity Network” or MPN. The products were various software, computers, networking, interfaces and measurement systems. HP had been in this business for a long time—longer than any other company. It started with government’s and others’ request for automated test and measurement systems. Because of the need to automate various measurement instruments/systems, HP created the first machine-to-machine protocol called “HP-Interface Bus” or HP-IB. This was later formulized into the IEEE-488 Communication Standard. HP needed an “Instrument Controller” and so purchased a unique 16-bit computer architecture from Union Carbide (unique in that the operating system was ‘real time and interrupt driven’). This became the HP2116 in 1964. This computer was unique in that it had space for 16 interface cards for measurement instrument. What HP didn’t realize was that many companies were using the computer, not with instruments, but with multiple input terminals and printers, creating the first ‘Time-share-systems’. So HP created a smaller and lower cost version, called the HP2114. This led to the world’s first time-share system, the HP2000. Later, this would evolve to a multi-user business system called the HP3000 and used what they called the HP-Precision Architecture (HP-PA). Today, only six Enterprise Hardware architectures have survived (all American) the endless computer wars; HP-PA, IBM’s POWER architecture, Sun’s SPARK, AMD X86-64 and Intel’s XEON and Itanium.
The CIM Architecture was defined as early as 1980, when the CASA/SME[1] published a presentation of computer integrated manufacturing in order to provide a common set of terms for its members. As published by CASA/SME, the CIM Wheel of 1980 definition was:
The ring surrounding the wheel represents various influencing factors (man and his degree of expertise as the human factor, productivity as the economic factor and computer technology as the technological factor) for the development of CIM.
The updated CIM wheel (1986) contained the following:
The wheel itself contains four functions, namely engineering design, manufacturing planning, production control and factory automation. If the individual functions are connected with each other and operate with a common database, an integrated system architecture is created which is represented by the hub of the wheel. This development has resulted in the realization that CIM, apart from factory automation and functions indirectly related to the operational performance such as design (product/process) and production planning and control, is also linked to common business administrative tasks such as manufacturing management, strategic planning, finance, marketing and human resource management. A further innovation was the addition of information resource management and communications between the different functions. Therefore, a common database alone is insufficient for achieving integration. The all-embracing nature of the CIM wheel reflects the idea promoted by CASA/SME that CIM has to be viewed as a concept embracing the company as a whole.
Figure 1: The CIM Wheel defined by CASA/SME[1].
The outer ring
The common business administrative tasks related to CIM are located on the outer ring of the wheel. They mainly form the connection of the company to the outside world in general. Data processing applications can be found in the most diverse areas. Most software systems applied in these areas were originally self-styled developments, which are increasingly being replaced with commercial standard software packages. Currently this software is installed primarily on mainframes. Overlaps of its functionality exist mainly with the software of the production planning and control.
The inner ring
On the inner ring of the wheel, the functions closely related to the operational performance of the company are situated. Data processing applications of the development and design area are computer aided design (CAD), simulations, analysis programs such as the finite element method (FEM) as well as drawing storage and management, for instance with the help of group technology (GT).
The types of data found in this area are diverse: drawings, technical specifications, and bills of material. In manufacturing companies, the data itself are often in considerable disorder. Frequently there are several types of part numbers, more than one group technology system, many kinds of bills of material, a number of different CAD systems each having its own sort of computer internal representation of geometric data, etc. The applied software rarely runs on the same hardware, resulting also in a large number of different hardware systems.
The second group of applications on the inner ring of the wheel is attributed to process planning and production planning and control. It comprises tasks such as routing generation, resource planning, material requirements planning, capacity planning, order distribution and supervision, but also the planning of quality assurance (quality process and resource planning). In the USA, software in the production planning and control area mostly runs on large client/servers, although the software itself is more often than not supplied by sundry software houses and not by the computer vendor. As in the common business administrative area, the software packages—which at least are integrated within themselves—have a modular structure and their single components can also be bought and applied. Therefore, a company rarely has purchased and installed all modules of such a package, which in turn frequently results in functional overlaps and data redundancy (one example: material requirements planning and purchasing systems).
The third group on the inner ring includes the automation of the manufacturing installations. Examples are robots, numerically controlled machines, flexible manufacturing systems and computer-aided measuring and testing methods. This area is characterized by the extreme heterogeneity of the systems involved, the diversity of which being much more pronounced than in the previously mentioned groups of functions. Another view is the CIM Hierarchy, as seen in Figure 2.
The hub
The statements made above have already shown that at present within these groups of applications there are serious impediments with regard to integration. There are few suppliers covering all three sectors. Therefore, little or nothing has been done by the suppliers with regard to interfaces, not to mention the integration of the various groups of applications. Information and communication management, represented by the hub of the wheel which links everything, is intended to serve as the information management and communication control function between the single areas. It operates on a common, integrated database.
Figure 2: The seven arenas of a CIM strategy.
Page 1 of 4
Suggested Items
Infineon Advances on 300-millimeter GaN Manufacturing Roadmap as Leading Integrated Device Manufacturer (IDM)
07/10/2025 | InfineonAs the demand for gallium nitride (GaN) semiconductors continues to grow, Infineon Technologies AG is poised to capitalize on this trend and solidify its position as a leading Integrated Device Manufacturer (IDM) in the GaN market.
TTCI Joins Printed Circuit Engineering Association to Strengthen Design-to-Test Collaboration and Workforce Development
07/09/2025 | The Test Connection Inc.The Test Connection Inc. (TTCI), a leading provider of electronic test and manufacturing solutions, is proud to announce its membership in the Printed Circuit Engineering Association (PCEA), further expanding the company’s efforts to support cross-functional collaboration, industry standards, and technical education in the printed circuit design and manufacturing community.
GlobalFoundries to Acquire MIPS to Accelerate AI and Compute Capabilities
07/09/2025 | GlobalFoundriesGlobalFoundries announced a definitive agreement to acquire MIPS, a leading supplier of AI and processor IP. This strategic acquisition will expand GF’s portfolio of customizable IP offerings, allowing it to further differentiate its process technologies with IP and software capabilities.
LITEON Technology Reports Consolidated June Sales of NT$13.6 Billion, Up 16% Y-o-Y
07/08/2025 | LITEON TechnologyLITEON Technology reported its June consolidated revenue of NT$13.6 billion. Thanks to the growth from power management in cloud computing, advanced server, and networking, the revenue is up 2% M-o-M, 16% Y-o-Y. The cumulative sales for January to June totaled NT$76.8 billion, up 24%, Y-o-Y.
Inside Aimtron’s Cross-border EMS Strategy
07/08/2025 | Nolan Johnson, SMT007 MagazineMukesh Vasani immigrated from a very small farming village in India to the U.S. in 1995 as a civil engineer. After shifting into electronics, Mukesh built his Chicago-based company, Aimtron, into a successful enterprise by combining quality with competitive pricing. He leveraged his roots in India to expand manufacturing without compromising on quality.