-
- News
- Books
Featured Books
- smt007 Magazine
Latest Issues
Current IssueSupply Chain Strategies
A successful brand is built on strong customer relationships—anchored by a well-orchestrated supply chain at its core. This month, we look at how managing your supply chain directly influences customer perception.
What's Your Sweet Spot?
Are you in a niche that’s growing or shrinking? Is it time to reassess and refocus? We spotlight companies thriving by redefining or reinforcing their niche. What are their insights?
Moving Forward With Confidence
In this issue, we focus on sales and quoting, workforce training, new IPC leadership in the U.S. and Canada, the effects of tariffs, CFX standards, and much more—all designed to provide perspective as you move through the cloud bank of today's shifting economic market.
- Articles
- Columns
- Links
- Media kit
||| MENU - smt007 Magazine
Estimated reading time: 3 minutes
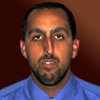
Got Whiskers?
The tin whisker phenomenon is an issue that has plagued the electronics industry for many years now; however, with even more sectors of the industry now looking to shift or go “lead-free”—eliminating or limiting lead—in their processes and products, focus on this potentially devastating issue appears to be on the rise once again. A topic that was a huge concern within the industry a decade or so ago, appeared to have waned in recent years, only to be re-establishing itself again from where I sit in the independent test laboratory world.
The phenomenon itself has been studied by many for years now and the question—why do whiskers form—has many answers and theories. In this column, I’m not focusing on the hows and whys of whisker formation, which can be an exhaustive discussion, but more so the testing side of things—more specifically, the testing that has been established to test your mitigation strategy or strategies. To that point, there is no single, perfect strategy for preventing tin whisker formation—other than putting lead in it, which kind of defeats the purpose I suppose—so don’t assume that one strategy fixes everything. For background, mitigation practices include all sorts of strategies, from heat treatments/annealing to conformal coatings/potting to matte versus bright tin finishes to many others.
As you may already know or have heard about, trying to control, influence, or predict the growth of tin whiskers is difficult to accomplish. With that, testing of your mitigation practices is critical and prudent for those truly doing their due diligence in the development of a reliable product. Various passages on tin whisker mitigation strategies can be found in industry magazines, scholarly journals, reference books, etc., so be sure to do a little research before you get too deep. As discussed in my October 2016 column, experience is everywhere and you can learn a lot of dos and don’ts by just doing a little homework.
An easy place to start when it comes to the testing of whichever mitigation strategy or strategies that you’ve implemented is a group of documents that are well-established in the tin whisker testing world. Specifically, the Joint Electron Device Engineering Council (JEDEC) has established two test standards that are very commonly used for tin whisker testing or are used as a basis for the establishment/development of your own tin whisker test. For reference, these documents are:
- JESD201A—Environmental Acceptance Requirements for Tin Whisker Susceptibility of Tin and Tin Alloy Surface Finishes[1]
- JESD22-A121A—Measuring Whisker Growth on Tin and Tin Alloy Surface Finishes[2]
Within these standards, the testing protocols call out three different environmental exposures: high temperature/humidity storage, low temperature/humidity storage, and thermal cycling.
Given the nature of tin whisker formation, which is slow and incremental, the testing typically performed is long, relatively speaking, to other common environmental exposure tests. For example, a common duration for the storage tests is 4,000 hours, which is almost 24 weeks, and 1,500 cycles for the thermal cycling test. Additionally, the specific test conditions—temperatures and humidity levels—can vary dependent on the exact test method being followed.
Supplementing the environmental exposure tests themselves, visual examination is a critical part of the evaluation process. Stereomicroscopes and scanning electron microscopes (SEM) are common tools of the trade for this type of inspection, as whisker formations can easily range from the micron level up to millimeters.
Of interest, in addition to the JEDEC documents, other groups have provided information on the whisker phenomenon, most notably iNEMI[3]. Also, others have developed additional test methodologies. The automotive and commercial electronics industries have had interest in the topic of tin whiskers for many years now as the RoHS directive’s ban on lead forced manufacturers to make the change to Pb-free materials, most notably solder as it pertains to the printed circuit assembly sector of the industry. Currently, the more traditional high reliability sectors of the industry—aerospace, medical, military…to name a few—are beginning to make some transitions for various reasons. Supply chain issues are a key factor in this more recent shift as component level manufacturers scale back their Pb-containing operations.
Ultimately, as with any process change for whatever the reason might be, a solid test protocol is crucial to ensuring that your product can meet your customer’s expected level of reliability.
References
- JEDEC, JESD201A
- JEDEC, JESD22-A121A
- www.inemi.org
More Columns from Let's Talk Testing
Let’s Talk Testing: Professor Plum in the Library with the Candlestick…Right?Random Thoughts on Employment, from Both Sides of the Table…
Let's Talk Testing: You’re in for a (Thermal) Shock!
Let's Talk Testing: How Strong is Your Foundation?
Let's Talk Testing: Are You Getting What You’ve Asked for?
Vias for Dummies
Don’t Reinvent the Wheel—Find an Expert!
Does your Product have a Military Application?