-
- News
- Books
Featured Books
- smt007 Magazine
Latest Issues
Current IssueMoving Forward With Confidence
In this issue, we focus on sales and quoting, workforce training, new IPC leadership in the U.S. and Canada, the effects of tariffs, CFX standards, and much more—all designed to provide perspective as you move through the cloud bank of today's shifting economic market.
Intelligent Test and Inspection
Are you ready to explore the cutting-edge advancements shaping the electronics manufacturing industry? The May 2025 issue of SMT007 Magazine is packed with insights, innovations, and expert perspectives that you won’t want to miss.
Do You Have X-ray Vision?
Has X-ray’s time finally come in electronics manufacturing? Join us in this issue of SMT007 Magazine, where we answer this question and others to bring more efficiency to your bottom line.
- Articles
- Columns
- Links
- Media kit
||| MENU - smt007 Magazine
Estimated reading time: 9 minutes
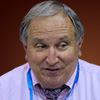
Contact Columnist Form
A New Organizational Model Using Logic, Cost-Effectiveness and Customer Service, Part 2
Words mean something, it seems, unless you are a politician.
No matter what your political views, it is hard to dispute that the recent U.S. election was unique and certainly not in a way that makes us want to stand up and cheer. Before the email deluge begins, let me make it clear that I’m talking about the election process.
Speaking truth to power has a romantic and compelling draw. However, this campaign was no Mr. Smith Goes to Washington. I have often counseled young engineers that being right on a technical point is not enough—that the package you put your information in is as important as the information itself. In team dynamics we call this aligning constituencies, and it is an important element in influencing other team members. It’s hard to gain the support of others after you’ve used your command voice—or worse, called them the devil’s spawn.
On the other hand, there is an attractive and refreshing quality to being direct when making a point, and calling one out when it is warranted—remember the child on the parade route screaming: the emperor has no clothes on! The art of rhetoric—persuading one to agree with your position on an issue—is walking the sometimes very fine line between the two approaches.
Production Volumes Take Off
Our corporate production organizations have been in place since Henry Ford created the assembly line in the early 20th century. Each line worker was given a small, repetitive task to perform in the overall assembly of an automobile. This reduced production costs and correspondingly, automobile prices. More and more of the population were able to afford this product. Production volumes skyrocketed. With the exploding volumes, more workers were needed. As the technology became more complex the workers developed areas of specialization. These workers had to be managed, so they were grouped in departments based on common skill sets and job responsibilities. A manager was assigned for each department in order to coordinate, assign and measure the activities of the group.
Management’s objective became one of maximizing the output and quality of the workers by controlling them—planning their work, reviewing their performance and keeping their nose to the grindstone. It was the Hamiltonian worldview that the workers (masses) were the beast and the beast must be controlled. See Fritz Lang’s Metropolis (1927), or on the lighter side Lucy and Ethel working on the chocolate assembly belt in the episode, Speed it Up!
So, we became chained to a production organizational model that was hierarchical and laden with supervisors whose goal was optimizing worker productivity.
There have always been areas of specialization such as wheelwrights, blacksmiths, plumbers and later soldering, welding, etc., but mass production for the first time brought many of these skills under one roof—working for one employer and grouped in departments.
Even before Henry Ford, in the 18th and 19th centuries, workers were employed in ever increasing capital-intensive industries such as textiles. Customer demand for these products caused workers to leave their cottage operations and join together in factories. Replacing water mills and other equipment with those that were steam-driven, permitted the factories to be located anywhere, not just near a source of running water.
It sounds counterintuitive, but in the early days of the new republic as this transition of the workforce took place, "[the] primary reason for the rapid industrialization of the United States was very high labor costs...American wages were high because employers had to compete [for employees] with the exceptional opportunities of self-employment in order to attract adequate numbers of qualified workers."
This competition in production still exists today. Because of the high levels of automation now required to deal with very small components in electronic products, companies that do their own product assembly have thought they could hire cheap labor to just push the buttons and let the machine do the hard stuff. Developing, programming and maintaining the automation was relegated to others with the necessary skill sets. This fit nicely in the hierarchy and organizational power pyramid.
However, now with sources of low labor rates that the global economy has ushered in, high production wages become a convenient excuse to offload the manufacturing and assembly of their products. Companies are finding that producing their products remotely to take advantage of these lower rates can have some serious drawbacks. To me there are only two reasons to produce your products remotely:
1. You want to sell them into that remote marketplace (a good reason)
2. You can’t compete with those remote sources of production (a bad reason)
In previous columns, we have talked extensively about the one of the controllable components of labor cost: the counterweight to competing against low labor rates—using automation to reduce labor content. Over the next few months we will drill down into the other controllable component of labor cost: indirect labor.
Why Do We Do Things This Way? Because We Always Have.
Does art imitate life or does life imitate art?
Is product production a result of our organizational structure, or is our organizational structure a result of the needs of product production?
It seems we have hierarchical, pyramid shaped organizational structures because they are rooted in the past, not because they are necessarily best. They certainly cost more than alternatives. If the traditional structure is not the closest to perfection, what alternative is?
Plato believed we are born out of perfection and true reality—the World of Ideas. As we begin our human existence, all we have is a quickly fading memory of that perfection. It’s as if we’re tied up in a cave, watching only shadows flit about on the wall in front of us, projected from the World of Ideas. The shadows. We mistake the shadows for reality. They ultimately become our reality.
Aristotle, Plato's student, believed we start with a tabula rasa, a blank slate. What we think and perceive become impressed on that slate (our mind) and we are quickly corrupted by the reality of our surroundings. Pick your philosopher.
So, many things have changed in our technological world. One thing that hasn’t changed is how we organize the personnel in high tech production operations. Our production reality is formed by centuries of doing things a certain way. Breaking this organizational paradigm is a daunting challenge.
The Greek theater was therapeutic for the people (polis). It permitted all the bad human impulses to be cathartically dealt with, and reinforced noble, virtuous behavior. Do we have a comparable, lesson-teaching method today? Most of the entertainment I see today has things blowing up or people rolling around together—art, I guess.
In Plato's world, juries were formed with an average of 501 members to ensure justice. Why? Because it is difficult to bribe that many people when conspiring to rig a jury verdict. Back then, if the Greek laurel wreath didn’t fit, you must acquit.
However, pure democracy could often result in mob rule, so in Plato’s mind the people should find a wise philosopher-king to rule absolutely. This person would be given total control and the people must comply. Ideally, infants would be taken away from their families and raised by the government in camps. This was the way to ensue equality—no one getting a head start because they came from a wealthy family.
In fact, it was the mistrust of the people that caused the founders not to elect the president by popular vote, but have an electoral college establish who would be President.
Political campaigns have always been savage. The election of 1800 resulted in an electoral tie between Aaron Burr and Thomas Jefferson and was filled with intrigue. Each of the 16 states had one vote as the election, according to the Federal Constitution, was to be decided by the states voting in House of Representatives. This would determine the third President of the United States. It took 36 separate votes of the 16 states to decide in Jefferson’s favor.
Even though political campaigns could be brutal, one’s honor meant something. In those days, having one’s honor challenged would sometimes result in a dual—witness Alexander Hamilton and Aaron Burr in 1804 that resulted in Hamilton’s death.
It seems we don't have that push back today. Lying for many has become a way of life. Politicians lie with conviction. It’s become a prerequisite for the job—a job that the Founders never thought of as a lifetime occupation. For them, serving their country was a drudge, a sacrifice—although a necessary and honorable one. Getting back to private life was their objective.
Today, lying is only wrong if you get caught—and then, not really wrong because everybody does it and what do right and wrong mean anyway in a relativistic (not, Einstein’s relativity), deterministic world. My DNA made me do it!
Win at all costs is the message. Winning is the only option. The end justifies the means. What happened to using, It’s not winning or losing it’s how you play the game as the pole star that guides us on how best to compete?
As mentioned above, Henry Ford helped establish the current organizational hierarchical model through the practice of assembly line specialization. Our educational system reinforced the model by offering majors in engineering, economics, political science, anthropology, history, etc. based on the current state of thinking for each discipline. However, the laws of physics don’t change. Our understanding of them changes, from believing the earth is at the center of the universe to Newton’s laws of motion to Einstein’s theory of relativity.
As mentioned last month, academia has been able to adjust their educational offering to our changing understanding of the general laws. What they haven’t done very well is adjust to the constantly changing practical application of these laws in product production—what we call Industrial Engineering.
Professors try to interpret the real world’s needs and adjust, but those without practical experience continue to fail in the learning for earning part. They are always playing catch up.
Sometimes we may have noble strategic objectives, but fail to develop or carry out a tactical plan to meet those objectives—the words are easy. Academia always has good intentions for industry, but seldom achieve good results. An academic institution has an objective of giving their students a firm understanding of the classical subjects. Part of the tactical plan that schools use to achieve this objective in technical subjects is to confront students with closed-form problems. Students that can demonstrate success in solving these problems are thought to have grasped an understanding of the underlying subject matter.
In the real world, critical thinking is an invaluable tool to solve the open-form problems that, more often than not, we are confronted with. Even with the best intentions, the academic classroom is a difficult environment to teach this important judgment tool.
The real world has had to comply with academia, rather than demand that academia meet their needs for qualified graduates. Lofty thinking and the ability to solve non-linear differential equations, while important, are not critical to success on the production floor.
To read this entire article, which appeared in the January 2017 issue of SMT Magazine, click here.
More Columns from Jumping Off the Bandwagon
The Proper Position to Take on Voids in Solder JointsAnalyzing Material Cost in Today’s Global Economy—Hit the “Pause” Button
Analyzing the Cost of Material in Today’s Global Economy, Part 3
Analyzing the Cost of Material in Today’s Global Economy, Part 2
Reading, Writing, Listening, Speaking and Analyzing Material Cost in the Global Economy, Part 1
A New Organizational Model Using Logic, Cost-Effectiveness and Customer Service, Part 3
A New Organizational Model Using Logic, Cost-Effectiveness and Customer Service, Part 1
Leadership in Your Company: Something to Worry About?