-
-
News
News Highlights
- Books
Featured Books
- pcb007 Magazine
Latest Issues
Current IssueThe Hole Truth: Via Integrity in an HDI World
From the drilled hole to registration across multiple sequential lamination cycles, to the quality of your copper plating, via reliability in an HDI world is becoming an ever-greater challenge. This month we look at “The Hole Truth,” from creating the “perfect” via to how you can assure via quality and reliability, the first time, every time.
In Pursuit of Perfection: Defect Reduction
For bare PCB board fabrication, defect reduction is a critical aspect of a company's bottom line profitability. In this issue, we examine how imaging, etching, and plating processes can provide information and insight into reducing defects and increasing yields.
Voices of the Industry
We take the pulse of the PCB industry by sharing insights from leading fabricators and suppliers in this month's issue. We've gathered their thoughts on the new U.S. administration, spending, the war in Ukraine, and their most pressing needs. It’s an eye-opening and enlightening look behind the curtain.
- Articles
- Columns
- Links
- Media kit
||| MENU - pcb007 Magazine
Estimated reading time: 4 minutes
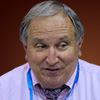
Contact Columnist Form
A New Organizational Model Using Logic, Cost-Effectiveness and Customer Service, Part 1
In the beginning, there was through-hole technology (pin-in-hole). Then, someone said, “let there be SMT,” and the earth and firmament creaked and groaned as Atlas shrugged.
In 1980, Washington’s Mount St. Helens erupted—an ominous harbinger prior to the mass arrival of the new technology, sort of like the kid’s swinging banjo from atop the bridge in the beginning of the film, Deliverance—the two canoes passing under: “Stop, stop. Go back, go back.”
But, no! Man (I mean, mankind; I wear my PC badge with pride) will take on and conquer nature. And, we all know how that turned out: “Aintry? This river don’t go to Aintry.”
It was as if the volcano cried out in nature’s language, “Stop, stop!” as it belched and spewed a profusion of greenhouse gases. The dark foreboding this event created was an omen for more cataclysmic events to come. Seven years after Mt. St. Helens erupted, there was an earth-quake in Whittier, California, near Los Angeles.
Two years later, in 1989, the Loma Prieta temblor struck the San Francisco Bay area, the epicenter near, you guessed it, the SMT epicenter of San Jose. The World Series at Candlestick Park was interrupted as Mother Nature continued her protest. Say it ain’t so, Joe—as the earth rebuked man’s (I mean, humanity’s—I’m a sensitive guy, you know) attempt to make things smaller yet.
“Smaller, Smaller,” I say, as Moore (Gordon, not Clement) became our patron saint. Those of us that were there at the creation asked, “This is good?”
But, it was. We went to sleep and when we awoke all was right with the world. Why, without it there would be no Pokemon GO, no portable social media, no ability to tell you in real time what I just had for lunch.
Probably more significant are the medical breakthroughs in monitoring and pharmaceutical delivery systems, endoscopic operating procedures, wearable electronics, “ingestible” electronics—nanobots in our bloodstream, and other electronic devices and systems that will improve the human condition. The dangers are just as provocative—the incredible processing speeds we have available to operate on the big data that is being accumulated with every credit card purchase we make, putting personal privacy at risk: technology meet the Constitution! Also, using genetic engineering to create creatures that would frighten Dr. Frankenstein’s monster, and the ability to use robotics as a destructive force. These are just a few.
For you youngsters, I want you to understand that SMT technology doesn’t go back to biblical times, and it wasn’t brought to earth by ancient alien astronauts.
However, I do remember back in the beginning, after the wheels of change (excuse the mixed metaphor) were put in motion with a gust of wind. A large computer company got the attention of component suppliers by asking, out of the blue, for quotes on millions of these new surface mountable electrical component packages.
Four Things that Haven’t Changed Since the Advent of SMT
Nearly everything in the electronic product design and production business has changed since that fateful time. I can only think of four things that haven’t:
- The laws of physics
- The laws of economics
- The basic way we educate for our industry
- The way we structure our design and production companies
The first one we don’t have much control over. Personally, I’ve tried to levitate, but can’t seem to advance past the flutter stage.
The second one pertains to all businesses (e.g., the value of a product or a service is based on what a customer is willing to pay for it—supply and demand—the ability to make a profit [cost management], etc.).
The third one I’ve studied, analyzed, talked and written about. A new educational strategy to better serve the high-tech electronic design and assembly industry has been initiated. It will co-locate a college with a for-profit EMS provider. The EMS will provide the student with a real-world classroom for a four-year undergraduate program that will lead to a B.S. in Applied Electronic Product Design and Manufacturing Sciences.
That leaves number four.
Ironically, it is firmly linked to number three. How? An alternate production organizational model has not been available to us because graduates interested in design, manufacturing and assembly have been educated in our traditional educational framework—the Ivory Tower of academia, not the real world.
In other words, the skills needed for any alternative “lean” or “flattened” organizational model can only be taught in the real world—soft skills such as working in self-managed teams, conflict resolution, aligning constituencies, and the art of rhetoric and persuasion as they apply to team dynamics. In past columns, we focused on the technical skill gap between academic preparation and industry need. However, the ability to reduce labor cost by organizational reform requires a real-world classroom, as well.
Before volume manufacturing and assembly opened on the global stage, it didn’t much matter. The severe international competitive pressure wasn’t there. Production labor rate competition was locally based. Protectionist tariff policies as well as concerns about low labor rate production skills and quality were used to resist these sources of low labor rate cost.
This partial column was originally published in the December 2016 issue of SMT Magazine. Click to continue reading.
More Columns from Jumping Off the Bandwagon
The Proper Position to Take on Voids in Solder JointsAnalyzing Material Cost in Today’s Global Economy—Hit the “Pause” Button
Analyzing the Cost of Material in Today’s Global Economy, Part 3
Analyzing the Cost of Material in Today’s Global Economy, Part 2
Reading, Writing, Listening, Speaking and Analyzing Material Cost in the Global Economy, Part 1
A New Organizational Model Using Logic, Cost-Effectiveness and Customer Service, Part 3
Leadership in Your Company: Something to Worry About?
A New Organizational Model Using Logic, Cost-Effectiveness and Customer Service, Part 2