-
-
News
News Highlights
- Books
Featured Books
- pcb007 Magazine
Latest Issues
Current IssueThe Hole Truth: Via Integrity in an HDI World
From the drilled hole to registration across multiple sequential lamination cycles, to the quality of your copper plating, via reliability in an HDI world is becoming an ever-greater challenge. This month we look at “The Hole Truth,” from creating the “perfect” via to how you can assure via quality and reliability, the first time, every time.
In Pursuit of Perfection: Defect Reduction
For bare PCB board fabrication, defect reduction is a critical aspect of a company's bottom line profitability. In this issue, we examine how imaging, etching, and plating processes can provide information and insight into reducing defects and increasing yields.
Voices of the Industry
We take the pulse of the PCB industry by sharing insights from leading fabricators and suppliers in this month's issue. We've gathered their thoughts on the new U.S. administration, spending, the war in Ukraine, and their most pressing needs. It’s an eye-opening and enlightening look behind the curtain.
- Articles
- Columns
- Links
- Media kit
||| MENU - pcb007 Magazine
Estimated reading time: 9 minutes
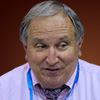
Contact Columnist Form
Analyzing the Cost of Material in Today’s Global Economy, Part 2
Last month we began a discussion on the cost of material associated with electronic product assembly.
It was recognized that any increase in material cost based solely on an assembly operation’s geographic location could cause a condition that would not allow a turnkey electronic product assembler to successfully compete on the global landscape.
Previous research has uncovered the fact that material price variation of this kind does exist. The disparity cannot be explained by shipping costs or differences in the overhead costs of a particular component manufacturer or distributer's location.1
Considering that material is typically 70–90% of the total recurring production cost of a product, even small disparities in material cost as a function of geographic location can bury the effect of labor rate differences. Regardless, it is differences in labor rates that seem to get all the press attention.
So, let’s drill down into material cost and try to understand all the variables involved, both those that can be controlled and those that cannot.
Before putting the drill in the chuck, however, a definition of terms will be needed to maintain our sanity. Specifically, how we have historically used the terms manufacturing, production and assembly, as they apply to electronic products has vexed me for about 30 years. It is the inconsistency in use that has been a source of confusion and annoyance. Here is how I have proposed to use these three terms:
Production: An overall collection of processes used in creating a product that can be sold to an end user. It includes components of manufacturing and assembly.
Manufacturing: A process or series of processes that use material fabrication techniques to create a largely inseparable part or component. It is an irreversible process. For electronic products, the fabrication techniques include thick- and thin-film wafer processing, wire bonding, machining, molding, casting, coil winding, potting, encapsulating and component testing.
Assembly: The process of putting together manufactured components or parts into a definable configuration. This may include electronic testing as a step in the assembly process. The final assembly of a product may include the joining of several sub-assemblies. Assembly processes use value-added labor and/or automation (i.e., machine labor), to create a subassembly or the final product. It is generally a reversible process.
In the current parlance when we speak about a loss of manufacturing jobs, we really mean a loss in production jobs; this would include jobs in manufacturing and assembly.
The elitist brain trusts in government and academia who came up with the acronym STEM: Science, Technology, Engineering and Math2 should have included production, or STEMP. However, product production has never gotten the respect it deserves. It is the reason that in the States, the VCR could be invented (1962, RCA Model TR-22), but the U.S. never developed a commercial version nor produced it in volume.
In a sense, it is analogous to the relationship between a company’s direct labor force and their management. This relationship has been discussed previously in this column: Direct labor pays for indirect and overhead costs such as management and indirect engineering, in a similar way that mass-produced products pay for the theoretical science, technology, engineering and mathematics that they incorporate.
Production deserves a place of its own at the top of the Mount Rushmore of technical education—next to science, technology, engineering and mathematics. STEM subjects have always been more theoretical than practical.
However, there is no question as to the importance of pure science, classroom technology, design engineering, and pure mathematics. One does not have to be a rocket scientist to understand the seminal role these technological tools play in the development of a firm foundation for the proper execution of applied high-tech electronic product production.
However, teaching how to apply the theory in production can never be effectively taught in the ivory tower.
Yet, high-tech product production relies on:
- Automation science and physics (motion control, etc.)
- Material science (solder paste rheology)
- Chemistry (solder paste and cleaning)
- Heat transfer and thermodynamics (wave and reflow soldering)
- Statistics for developing a successful assembly process (process validation and meta process control) and understanding a process with non-random variation that is beginning to trend toward an upper or lower control limit
A deep understanding of all these sciences, along with other classical subjects, is required for a production engineer to be successful.
This is where the learning for earning part comes in. Those applied production skills and the associated sciences need to be taught in a real-world setting, concurrently.
With the high-tech contributions of advanced packaging automation incorporated in the manufacturing and assembly of today’s electronic products, production should be a science on the same level as subjects classically taught in an engineering curriculum. However, production cannot be successfully taught in an antiseptic classroom.
One example of what the education community holds up as high academic achievement can be found by looking at the 90th Scripps National Spelling Bee that has just been concluded. The final round was held on June 1, in Maryland. This event was televised with all the hoopla of a major sports event. Mini-bios of the finalists from the field of 291 entrants, aged 6–15, were inserted in the coverage as the contenders sought to be enshrined at the top of this spelling Mount Olympus.
The contestants’ friends and families were present, forming the gallery—cheering, hoping and praying for a successful conclusion to what must have been countless hours of memorizing lists of obscure words.
The entrants always ask the same questions after being given their word to spell: “What is the country of origin? Are there any alternate pronunciations? Please use the word in a sentence.” Then, they inevitably ask the moderator to repeat the answers to all those questions all over again!
These are beautiful young people. But, you can’t help but wonder what the psychological effect is on them—even the winner? I don’t mean to sound unkind, but is this the kind of academic achievement we want to celebrate and emphasize?
It seems it is. And, it is consistent with what academia subconsciously praises as academic achievement as students move from the primary to the secondary to the post-secondary segments of the educational pipeline. It is success built largely on the skill to “memorize, regurgitate and forget,” as Murray Gell-Mann, world-renowned particle physicist, Nobel Prize winner, and co-proposer of the existence of the Quark, credited upon receiving his Doctorate in Physics from MIT.3
Genuflecting at the altar of an academic grade point average that is built primarily on learning for learning, without regard for learning for earning, is not in the student’s (i.e., academia’s customers) best interest.4
What are the basic cost variables that influence the ability of an electronic product producer to compete?
Labor
1. Raw labor ($/hr.)
2. Indirect labor ($/hr.)
3. General & administrative cost ($)
4. Rework labor cost ($/hr.)
5. Overhead (controllable & uncontrollable) ($)
Material
1. Raw material ($)
2. Material markup ($)
a. Material attrition
b. Material scrap
c. Material handling
Raw (direct) labor costs are established by some combination of the laws of economics and local labor laws. They are dependent on where the labor is utilized.
The material that the applied labor adds value to (i.e., inspection, kit, prep, assembly and functional test) is almost all manufactured in the same few geographic regions (Pacific rim, Mexico, India). However, unless a Tier 1 or 2 assembler is using huge quantities of components from the same manufacturer, they are purchased from distributors, not the manufacturer.
The distributor will buy material from many manufacturers, stock the material, mark the material up and sell the material to an assembler. The price that the distributor establishes is based on:
- The cost that the component manufacturers charge
- The distributor’s overhead cost that must be loaded and absorbed in the component price
- The quantity the assembler orders
- The currency that will be used to pay for the material (e.g., US dollar (USD), Yuan, etc.
- Any applicable import and export tariffs
- The location where the material is shipped (although not publicized)
A more direct example of pricing disparity based on geographic location is the price of automated assembly equipment. Consider what the same automated component placement machine (i.e., pick and place) made by the same equipment company has sold for in China and the U.S.—a significant price disparity exists. Why? Is it number 4 or 5 or 6, above? Is it the costs associated with shipping this large, heavy item? If it is F.O.B. point of shipment, this item is not included in the equipment price anyway. Or, is it some combination of the above factors? Considering number 4, 5 and the shipping costs does not result in pricing parity.
Let’s examine item 4: “The currency that will be used to pay for the material...” As an example, consider the purchase of a reel of 5000, 0603 SMT resistors in both U.S. and China.
The resistors are manufactured and put on tape and reel in China.
Further, assume the price for the reel of resistors from the distributor is 340 yuan (note: the yuan is the basic unit of the Chinese currency that is called the Renminbi, literally “people’s currency”).
The current exchange rate between the USD and the yuan is: USD1 = RMB6.8. Or RMB1 is worth $0.147.
So, the reel of resistors will cost $50.
If the yuan depreciates with respect to the USD, what happens? Let’s say a USD will now buy RMB10.0 instead of only RMB6.8 or RMB1 is worth $0.100 instead of $0.147. The yuan is depreciated or devaluated with respect to the USD by 32%.
What is the impact on buying the reel of resistors? The price of the reel is still RMB340, but the price is now $34.00 instead of $50.
The opposite is true if the yuan appreciates in value with respect to dollar. The material for the U.S. product assembler will cost more.
The material purchased from distributors in the U.S. should be less expensive if the yuan is artificially kept down or devalued!
So why has the U.S. government complained about a manipulated undervalued yuan? If a U.S. company wants to sell a product it manufactures into China with the yuan at an artificially low level, let’s say at a price of $100, the Chinese consumer will have to pay more yuan making the U.S. made product less competitive.
But, here is the fallacy. Since the components made in China and purchased with USD costs less with a devalued or undervalued yuan, the U.S. assembler should be able to reduce the overall price of the product and make it more attractive to not only the Chinese consumer, but to consumers worldwide. This is especially true with material being 70–90% of the total electronic product cost and most of that material coming out of Asia. This should be significant.
But, the material is not less expensive when purchased for assembly in the States with a strong dollar and a weak yuan. Why?
We will continue next month.
Hey, what do YOU say? I’d like to hear your thoughts, reactions and opinions.
References
1. T. Borkes, “Electronic Product Assembly in the Global Marketplace: The Material Piece of the Competitive Puzzle,” SMTA International Conference Proceedings, Orlando, Fl., October 2010.
2. T. Borkes, “The STEM Trap,” SMT Magazine, July 2016.
3. M. Gell-Mann, The Quark and the Jaguar: Adventures of the Simple and the Complex, Henry Holt, 1994.
4. T. Borkes, “Moving Beyond Paideia: Learning for Earning,” SMT Magazine, August 2016
More Columns from Jumping Off the Bandwagon
The Proper Position to Take on Voids in Solder JointsAnalyzing Material Cost in Today’s Global Economy—Hit the “Pause” Button
Analyzing the Cost of Material in Today’s Global Economy, Part 3
Reading, Writing, Listening, Speaking and Analyzing Material Cost in the Global Economy, Part 1
A New Organizational Model Using Logic, Cost-Effectiveness and Customer Service, Part 3
A New Organizational Model Using Logic, Cost-Effectiveness and Customer Service, Part 1
Leadership in Your Company: Something to Worry About?
A New Organizational Model Using Logic, Cost-Effectiveness and Customer Service, Part 2