-
- News
- Books
Featured Books
- smt007 Magazine
Latest Issues
Current IssueMoving Forward With Confidence
In this issue, we focus on sales and quoting, workforce training, new IPC leadership in the U.S. and Canada, the effects of tariffs, CFX standards, and much more—all designed to provide perspective as you move through the cloud bank of today's shifting economic market.
Intelligent Test and Inspection
Are you ready to explore the cutting-edge advancements shaping the electronics manufacturing industry? The May 2025 issue of SMT007 Magazine is packed with insights, innovations, and expert perspectives that you won’t want to miss.
Do You Have X-ray Vision?
Has X-ray’s time finally come in electronics manufacturing? Join us in this issue of SMT007 Magazine, where we answer this question and others to bring more efficiency to your bottom line.
- Articles
- Columns
- Links
- Media kit
||| MENU - smt007 Magazine
Estimated reading time: 13 minutes
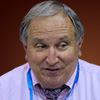
Contact Columnist Form
A New Organizational Model Using Logic, Cost-Effectiveness and Customer Service, Part 3
Many of us look to the new U.S. federal administration sworn in on January 20 with a high level of economic curiosity. How will the new president’s economic policies affect the high-tech electronic product assembly industry? Will the policies result in more jobs in our industry going to sources with low labor rates, or will they result in a renaissance of manufacturing and assembly activity here in the States and other high-labor-rate regions of the world?
As president-elect, Trump said: “Companies are not going to leave the United States anymore without consequences.”1
Does that mean that U.S. companies choosing to manufacture outside the U.S. will be penalized with an import tax (tariff) on their products when they are imported to the States for sale? That is the threat.
This is the sort of protectionist policy Brazil has had in place for decades. Products that are assembled outside Brazil and imported into Brazil are taxed. The increased price of the product is passed along to the Brazilian consumer. So, if you want to competitively sell your products into this large market (about 210 million people), you really need to assemble it there.
Historically, the evidence suggests when the government tinkers with the private business sector it never ends well. And, “ends” is the operative word.
We live in a throw-away world. Whether it is a diabolical crime or a Super Bowl victory the impact of a news story doesn’t last very long in the collective consciousness.
Politicians are aware of the public’s fleeting appetite. They will often promote a policy that sounds good in the moment and plays to the emotional mood of the people for the potential popularity or vote count it brings—establishing a straw man on which to blame the plight of the people. This promotion is often done without regard to the long term damaging effect of the policy. This is the definition of a demagogue.
Having the government pick business winners and losers, even with the noblest intentions (e.g., leveling the playing field) may seem like the right thing to do, but eventually leads to making a bad situation worse, not to mention creating an environment rife with the potential for corruption.
Brazil and Venezuela are contemporary examples of these government-centric, collectivist private business policies.
To view the opposite end of the free market spectrum, look at Hong Kong when it was under British rule: total free trade. It was a bastion of economic activity. It is interesting to note that in 1997 when Hong Kong was returned to the control of the People’s Republic of China, the free trade policy was maintained. So, where business in mainland China is regulated under a system of government controlled State capitalism, the Chinese government has refused (at least for now) to kill the Hong Kong golden goose cash machine. In addition, their business (or profit) tax rate is 16%. In the United States, it is 35%.
To Tariff, or not to Tariff, That is the Question
Milton Friedman, a father of economic freedom, described a government imposing a punitive tariff this way: Imagine you are in a canoe on a lake with a rival. An argument ensues leading to your opponent shooting a hole in his side of the canoe. You decide to get even by shooting a hole in your side. The result in the long run is that both parties lose.
The point is, many think of government protectionism as a way for a country to create and maintain jobs and promote economic prosperity. This is predicated on the assumption that it is better for a country to export rather than import goods. We speak of a favorable balance of trade, as one where a country exports more than it imports. Or, use the pejorative term trade deficit to describe a country that imports more goods than it exports. This is a hotly debated question and beyond the scope of this column except to say the following: Timing must be considered. If there develops a scarcity of jobs in an industry because companies who design products have outsourced the manufacturing of those products to areas with low labor rates, consider this: What will accompany the exodus of manufacturing jobs is a reduction in the disposable income of those consumers.
So, it’s fair to question to ask what good is it for a country to corner jobs in a particular industry if, in the long term, they destroy the buying power of the markets they want to sell the products into depressing that industry’s economy?
In the long run, the effect in the manufacturing country will be upward pressure on labor rates, causing an increase in product prices making other manufacturing sources compete more favorably. In the consuming country, prices for the imported product will rise, both from the manufacturing country’s increasing labor costs resulting in them raising their prices and the government imposing tariffs. The consumer eventually loses.
A Milton Friedman disciple would maintain that importing products made by others is actually a badge of economic success for a country, not a symbol of economic failure.
Why? Because it is a country’s consumer who rules and makes the rules based on immutable economic law. This happens automatically without any conscious action. Adam Smith (the Scottish economist and contemporary of Thomas Jefferson) called it the “invisible hand.”
Product prices are set, demand is created and industries are ultimately successful not because of government—the government hand—but by the natural laws of economics, or the invisible hand.
So, what is the general guideline for global business success? Find products, services and industries you can compete in successfully: on the merits of your product designs and/or value of your manufacturing services—not by hiding under your government’s protectionist shield.
Back to Brazil: In Florida, as a prime tourist destination, we have a huge population of Brazilian visitors each year. As popular as the theme parks are there is another destination many will add to their holiday itineraries—the Apple Store. Why? Apple smart phones cost 50% less in Orlando than in Sao Paulo.
So there it is: If you buy the premise, then the way to win is to sell better products at lower prices—not whine about the protectionist policies of the competition.
What these Jumping Off the Bandwagon columns have attempted to do is provide a roadmap toward that end. Assuming the company’s controllable component of product cost is labor, the columns have analyzed the corridors of labor looking for advantages and edges to realize the cost reduction part of this goal.
The other part of the product cost pie is material and shouldn’t be ignored out of hand. However, at this point, it is beyond the scope of our discussion2.
In summary, the following has been concluded:
- Automation is the counterweight to low labor rates. High labor rate environments can compete by reducing labor content through automation.3
- In this automated environment, the workforce needs to be transformed from many low paid direct personnel to a few high paid engineers with the ability to develop and maintain the automated processes.4
- This new workforce must be cross-disciplined with each member having multiple skill sets and the versatility to multitask and wear whatever hat is necessary at a particular point in time. They will be focused on the products they are assembling, not the departments from whence they once resided.
- What must accompany this workforce transformation is a transformation in the company’s organizational model. The reduction in labor content must be accompanied by a corresponding reduction in indirect and overhead cost since there is less direct labor to absorb these costs5.
- This new organizational model is a structural disruption from the traditional hierarchical form of power pyramid (Figures 1 and 2).
- What is needed for the new workforce requirements and new organizational structure is a new approach to education6.
Figure 1: Direct and indirect labor cost contributors in a hierarchical pyramid organizational structure.
Doing Things the Way We Always Have Done Them
As discussed in last month’s column, it seems we have hierarchical, pyramid shaped organizational structures because they are rooted in the past, not because they are necessarily best (Figures 1 and 2). They certainly cost more than alternatives.4
As mentioned last month, over the centuries academia has been able to adjust their educational offering to our changing understanding of the general laws of science. What they haven’t done very well is adjust to the constantly changing practical application of these laws in product production—what we call industrial engineering.
Professors try to interpret the real world’s needs and adjust, but those without practical experience continue to fail in the learning for earning part.6 They are always playing catch up.
Figure 2: The effect of loading indirect labor cost on the direct labor rate.
Noble Intentions, Failed Results
Sometimes we may have noble strategic objectives, but fail to develop or carry out a tactical plan to meet those objectives—the words are easy. Academia always has good intentions for industry, but seldom achieve good results. An academic institution has an objective of giving their students a firm understanding of the classical subjects. Part of the tactical plan that schools use to achieve this objective in technical subjects is to confront students with closed-form problems. Students that can demonstrate success in solving these problems are thought to have grasped an understanding of the underlying subject matter.
In the real world, critical thinking is an invaluable tool to solve the open-form problems that, more often than not, we are confronted with. Even with the best intentions, the academic classroom is a difficult environment to teach this important judgment tool.
The real world has had to comply with academia, rather than demand that academia meet their needs for qualified graduates. Lofty thinking and the ability to solve non-linear differential equations, while important, are not critical to success on the production floor.
How are We Going to Pay These People?
In previous columns, we introduced a fictional electronic product assembly company, Chips and Dips Inc. or what we affectionately call C&D.7
Two of the organizational charts for C&D at the top of the hierarchical pyramid are found in Figures 3 and 4. There are about 20 more. All of these departments, sections and groups are managed and nested into those above them until we reach the top level organizational chart (Figure 3), where they ultimately reside in one of six directorates, hence, the term hierarchical:
- Operations
- Engineering
- Business Development
- Finance
- Quality
- Human Resources
Figure 3: C & D top level organizational chart.
Adding the total cost of this top level chart alone results in $1.285 million in salaries (this does not include the cost of each employees benefits, at an average of 40% of salaries, or $514,000) and incentives. This adds up to a general & administrative cost of about $1.8 million, plus indirect cost that MUST be absorbed by the direct labor rate when we quote a job—say, to build electronic home alarm security systems for an original product developer (OPD).
Add to this the indirect labor expended by the operations directorate (Figure 4), about $2 million more. This causes us to load the average direct labor rate (the average salary with benefits) of machine operators, hand assemblers, test personnel, hand soldering, etc., typically hourly employees used for the direct assembly of the product with about $3.8 million. But that’s just part of the indirect cost iceberg—there are five more directorates!
All the department managers and some entire departments in the other five directorates are indirect labor sources as well, and must be absorbed by selling direct labor. This brief discussion makes it clear why the volume of direct labor that we sell is critical.
Figure 4: C & D quality assurance organizational chart.
As striking as these indirect costs are, the organization’s departments also create natural silos. This results in an employee’s sense of working for operations or engineering or quality assurance first, not C&D!
Unless we have very strong leadership and managers who put the welfare of the company ahead of their own departments, decisions are often made in the best interest of a department, not C&D.
And let the warfare begin as the hunt for the root cause of a bad company result is fought on an organizational battlefield that pits department against department, using weapons of denial, blame and finger pointing. I’ve seen it many times; maybe you have as well. It’s not a pretty picture.
The tentacles that tie the employees together across departments in the power pyramid are projects and/or new products. Good company leadership is essential to have personnel who reside in their department silos and are matrixed into a project team, work solely for the benefit of the project.
The lesson here is that an organization should try to maximize direct labor and minimize indirect labor to the extent possible.
Toward that end, a hierarchical, power-pyramid organizational structure biases labor in the opposite way, creating fractionalization built upon job specialization. This model in effect creates many towns, each town requiring a mayor and town council. But, where towns can operate in a quasi-autonomous fashion within a county, most departments in a product production company are intimately connected and each one’s performance is dependent on their neighbors.
Isn’t it amazing that we hire people to create and shorten an assembly process that reduces direct labor, but often don’t give the indirect labor, labor paid for by direct personnel, the same scrutiny and academic treatment—maybe that’s because many in these management ranks are academics.
New Model Considerations
I hope you recognize by now that it’s a bit ironic that indirect costs are only paid for with direct labor. If we reduce direct labor content through automation, we can support less indirect labor.
Maybe even more than a bit ironic and more of a way of protecting indirect labor, was keeping direct labor. So, box build assembly and other labor-intensive processes were valuable. This worked, whether conscious or subconscious, until production companies in high labor rate markets were thrust into a global manufacturing marketplace. Alarmingly low labor offshore rates being available caused enormous pressure to reduce labor cost. Most companies took the easy route as they knee-jerked their production to the low labor rate sources.
Next month, we’ll wrap up our discussion on organizational structure by presenting a radical alternative to the traditional hierarchical, pyramid-shaped one—one that greatly reduces the amount of indirect and overhead labor that needs to be absorbed by direct labor—one that ultimately permits a more efficient and cost effective way to manage electronic product assembly.
Hey, what do YOU say? I’d like to hear your thoughts and experiences.
References
1. Trump, Donald J., from Speech at Carrier, a division of United Technologies. December 1, 2016.
2. Electronic Product Assembly in the Global Marketplace: “The Material Piece of the Competitive Puzzle.” SMTA International Conference Proceedings, Orlando, Fl., October 2010.
3. T. Borkes, “Electronic Product Assembly in High Labor Rate Markets—A Case Study in Exploiting the Counterweight to Low Labor Rate Competition: Automation,” Pan Pacific Microelectronics Symposium, Big Island of Hawaii, February 12, 2014, pp. 4-5.
4. T. Borkes, “‘Like Holding the Wolf by the Ears…—The Key to Regaining Electronic Production Market Share: Breaking Free of the Division of Labor Manufacturing Model in High Labor Cost Global Regions,” SMTA International Conference Proceedings, Orlando, Florida, August 2008, pp. 4-7.
5. T. Borkes, “A New Manufacturing Model for Successfully Competing in High Labor Rate Markets,” Pan Pacific Microelectronics Symposium, Big Island of Hawaii, January 22, 2013.
6. T. Borkes, “Moving Beyond Paideia: Learning for Earning,” SMT Magazine, May 2016.
7. T. Borkes, “Toward a New Organizational Model Using Logic, Cost Effectiveness and Customer Service,” SMT Magazine, December 2016.
More Columns from Jumping Off the Bandwagon
The Proper Position to Take on Voids in Solder JointsAnalyzing Material Cost in Today’s Global Economy—Hit the “Pause” Button
Analyzing the Cost of Material in Today’s Global Economy, Part 3
Analyzing the Cost of Material in Today’s Global Economy, Part 2
Reading, Writing, Listening, Speaking and Analyzing Material Cost in the Global Economy, Part 1
A New Organizational Model Using Logic, Cost-Effectiveness and Customer Service, Part 1
Leadership in Your Company: Something to Worry About?
A New Organizational Model Using Logic, Cost-Effectiveness and Customer Service, Part 2