-
- News
- Books
Featured Books
- smt007 Magazine
Latest Issues
Current IssueThe Rise of Data
Analytics is a given in this industry, but the threshold is changing. If you think you're too small to invest in analytics, you may need to reconsider. So how do you do analytics better? What are the new tools, and how do you get started?
Counterfeit Concerns
The distribution of counterfeit parts has become much more sophisticated in the past decade, and there's no reason to believe that trend is going to be stopping any time soon. What might crop up in the near future?
Solder Printing
In this issue, we turn a discerning eye to solder paste printing. As apertures shrink, and the requirement for multiple thicknesses of paste on the same board becomes more commonplace, consistently and accurately applying paste becomes ever more challenging.
- Articles
- Columns
Search Console
- Links
- Media kit
||| MENU - smt007 Magazine
Vapor Degreasing Chemistries to Remove Difficult Lead-Free and No-Clean Fluxes from PCBs
May 26, 2017 | Venesia Hurtubise, Elizabeth Norwood, Wells Cunningham, and Laura LaPlante, MicroCare Corp.Estimated reading time: 7 minutes
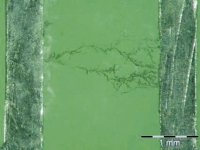
Abstract
Advancements in the electronics industry are continuously leading to more sophisticated, more intricate and more miniaturized circuitry. In conjunction with increasing regulations on electronics manufacturing, many changes have been made to the electronics world, and thus the circuit board manufacturing process. Lead-free, no-clean and halide-free flux formulations have introduced new cleaning obstacles, especially on ever-shrinking component sizes. In order to maintain high cleanliness standards for modern circuitry, new sophisticated cleaning chemistries are required.
The purpose of this paper is to present a cleaning process for difficult no-clean, lead-free and high temperature flux residues on reflowed PCBs. The proposed cleaning solvents are drop-in replacements for outdated solvent technology, or alternatives for elaborate aqueous systems. These cleaning technologies are used in traditional vapor degreaser systems, which allow for fast cleaning times and spot-free results without the need for additional rinsing or drying equipment. The improved formulas have low surface tensions (less than 20 dynes/cm), which allow access to low stand-off components and high solvency to combat the most difficult flux formulations and white residues. Visual and quantitative data are presented to assess the overall cleaning efficiency of the solvent system. Cost analysis is investigated to assess the efficacy of solvent vapor cleaning for PCB industry.
Introduction
Background
The beginning of the electronics manufacturing industry was, for lack of a better word, messy. Circuit boards were slathered with thick layers of fluxes, primarily foam flux agents, which would coat the entire underside of a circuit board. Aside from the inefficiency and visual untidiness, excessive flux can also lead to electro-chemical migration within the circuit and cause unintentional failures during use. Figure 1 shows an example of dendritic growth between two contacts. This migration can occur due to changes in temperature or humidity. Once the dendrite connects the two leads, the circuit can short and cause failures to the overall system. Needless to say, cleaning quickly became as important to the electronics production process as assembly.
Figure 1: Dendrite growth between two leads.
At the start of the electronics cleaning frenzy, vapor degreasing reigned dominant thanks to its ease-of-use, quick processing times and spot-free, dry results. One of the most common electronics cleaners of the 1980s was CFC-113 (more commonly known as FREON 113). Roughly 70% of FREON 113 use was designated to the electronics industry and in 1986 roughly 94 million pounds of FREON 113 was used in electronics manufacturing1. However, FREON’s reign was cut short in 1988 when the US ratification of the Montreal Protocol on Substances that Deplete the Ozone Layer forced the cleaning industry to discontinue the production of CFCs2. The Clean Air Act Amendment of 1990 increased the enforcement of ozone depleting substances and further restricted the cleaning industry3. At the same time, advancements in flux formulations lead to the development of no-clean and low-residue fluxes. These no-clean flux formulations are intended to remain on the board and leave minimal residues, which allows manufacturers to skip the cleaning process altogether. However, time has shown that these residues are still capable of attracting moisture, inhibiting conformal coating uniformity, or simply leaving aesthetically unacceptable visual results.
Page 1 of 3
Suggested Items
Indium Corporation to Showcase Precision Gold Solder Solutions at MEDevice Silicon Valley 2024
11/18/2024 | Indium CorporationIndium Corporation® will feature its high-reliability AuLTRA® MediPro gold solder solutions at MEDevice Silicon Valley, taking place on November 20-21 in Silicon Valley, California. AuLTRA® MediPro is a family of high-performance, precision gold solder solutions for critical medical applications.
AIM to Highlight NC259FPA Ultrafine No Clean Solder Paste at SMTA Silicon Valley Expo & Tech Forum
11/14/2024 | AIMAIM Solder, a leading global manufacturer of solder assembly materials for the electronics industry, is pleased to announce its participation in the upcoming SMTA Silicon Valley Expo & Tech Forum taking place on December 5 at the Fremont Marriott Silicon Valley in Fremont, California.
Data-driven Precision in PCBA Manufacturing
11/13/2024 | Julie Cliche-Dubois, CogiscanThe intricacies involved in electronics manufacturing require more than just expensive equipment and skilled technicians; they necessitate an accurate understanding of the entire production flow, informed and driven by access and visibility to reliable data.
Rehm Thermal Systems Mexico Wins the Mexico Technology Award 2024 in the Category Convection Soldering
11/13/2024 | Rehm Thermal SystemsRehm Thermal Systems Mexico has won the Mexico Technology Award in the category convection soldering with the patented mechatronic curtain for convection soldering systems.
SMTA: Capital Chapter & Connecticut Chapter Joint Technical Webinar
11/12/2024 | SMTAThe SMTA Capital Chapter is co-hosting a free webinar for SMTA members with the SMTA Connecticut Chapter on Tuesday, November 19 at 11:00 a.m. EST.