-
- News
- Books
Featured Books
- design007 Magazine
Latest Issues
Current IssueProper Floor Planning
Floor planning decisions can make or break performance, manufacturability, and timelines. This month’s contributors weigh in with their best practices for proper floor planning and specific strategies to get it right.
Showing Some Constraint
A strong design constraint strategy carefully balances a wide range of electrical and manufacturing trade-offs. This month, we explore the key requirements, common challenges, and best practices behind building an effective constraint strategy.
All About That Route
Most designers favor manual routing, but today's interactive autorouters may be changing designers' minds by allowing users more direct control. In this issue, our expert contributors discuss a variety of manual and autorouting strategies.
- Articles
- Columns
- Links
- Media kit
||| MENU - design007 Magazine
New Challenges Facing Mil/Aero Segment
August 16, 2017 | Stephen Las Marias, I-Connect007Estimated reading time: 8 minutes
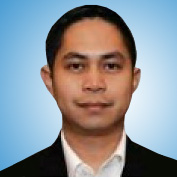
For this month's issue, we invited a sampling of professionals whose experience centers on the electronics industry in the military and aerospace world, including experts from design, PCB manufacturing, and the assembly arena to sit down with us for a frank discussion. Joining us were Freedom CAD’s COO Scott Miller; Lenthor Engineering VP of Sales/Engineering John Rolle and VP of Marketing Dave Moody; and Zentech’s CEO and President Matt Turpin and VP John Vaughan.
Our discussion centered on the challenges associated with military work, including the new regulatory requirements for cybersecurity, dealing with leaded vs. lead-free components, and the differences and similarities with the commercial world.
The discussion started on the PCB design perspective, whether the challenges are more technical or more centered on the administrative side, such as on regulations.
"I can tell you from our perspective, this year and going forward, the rules of engagement have really begun to change because of cybersecurity, and that’s having a huge impact on the engineering services community—how to comply with cybersecurity requirements that are now being mandated to us as external suppliers," explained Freedom CAD’s Miller. "It's something we’re spending a lot of time on. We’ve got work to do. We are ITAR-compliant, but cybersecurity compliance is a far deeper level of compliance than ITAR information management. That’s huge. We’re engaging with a consultant to help us understand how we can fulfill those requirements. And I think that’s going to be a game changer for a lot of the smaller companies that currently participate in the mil/aerospace marketplace, because there are some serious costs associated with cybersecurity management.
"It's a year-end objective. They want to have a supply base compliant, or at least have identified where the holes are, the weaknesses are, as far as we can tell, but there’s a huge impact. Assuming we overcome and address that, the other thing that has been kind of a mystery, and I’m sure everybody along the path sees this, is the defense budget, the DoD or Homeland Security, or whatever—any kind of government program—the defense budgets and understanding how the administrative change is going to slow down. Obviously, it looks like there’s going to be more spending in that area, but it’s not clear. Getting accurate forecast information or project information is difficult to do. We do our best to try to communicate with the customer and the subcontractor, etc., but they can only tell you so much because they only know so much."
Miller said that as the device types continue to get smaller and pin pitches get tighter, meeting traditional Class 3 requirements becomes increasingly difficult. "You can't meet Class 3 in certain applications, so you're consistently asking for a deviation or a waiver. Just because of the physics involved, you just can’t physically meet Class 3 in some cases. And if it's a rigid requirement, then you have to work with the customer’s engineers to fit the components that will allow you to meet that. From the standpoint of technology and architecture, we do things that are just as challenging in mil/aerospace, with fine lines and impedance matching, etc., that drive the consumer commercial world as well. From a technology standpoint, I don't think there's that big a gap in terms of what we’re seeing as design requirements. It’s been interesting to see how the government and the IRAD product development drives a lot of new technology as the government subcontractors try to figure out how to do things to differentiate their capabilities, and that kind of flows into the consumer world eventually, and vice versa; the commercial consumer world is developing technologies that are now being adopted readily in the mil/aerospace."
Lenthor's Moody next explained the challenges from a PCB fabricator's viewpoint. "There are a couple, though John might have some different perspectives from an engineering standpoint. The requirements in the mil/aero defense industry are mirroring what is available everywhere else. The perception that there are cost advantages or margin advantages for fabricators to work in the military industry are going away and have been disappearing for quite some time. There's a demand from a business standpoint on their end to buy more smartly—and better. So, the days where everybody thought, 'I'm going to participate in this military business because I can make more money at it' are kind of gone. There is a protection, to some degree, for the domestic fabricators because of ITAR content, so that remains as a competitive advantage on the business side for companies, domestically, who are trying to do business in this industry. But it is from the other aspects, such as design requirements, delivery requirements, etc."
Rolle added, "It's certainly challenging from a business perspective, because the expectation is to be competitive and then to continue to reduce that pricing. At the macro level, more dollars are being spent all the time. I'll build off what you were talking about earlier. Will it play down even to the fab level, where even if you’re successfully participating in a contract with really good schedule performance and very low defects, the expectation is that costs will reduce if you want to entertain the next bid on the contract? I think in some cases those contracts are summarily rejected if you came back to the same price. So, I think that’s the challenge. I don’t know that it is different from other large programs in other industries. However, I just want to add on to what Dave was saying, that our experience has been a difficult one.
According to Rolle, another challenge when it comes to engineering and tooling perspective are the drawings with existing requirements. "You're trying to comply with the drawing and you’ll have situations, like you were mentioning. You have to get a waiver, to do something differently, or something’s very cost-prohibitive due to an impact to yields. Getting changes through is always one of the supreme challenges. Even in cases where you provide a good service and your customer agrees to what you're requesting, often there’s no funding in the program to pay for your engineering change. We’ve come across that recently where we all agree with this, it makes a lot of sense, and it’s going to help you reduce costs, but nobody’s going to pay you any money to fix that. Or cases where it does go through, but the length of time it takes to go through automatically puts the entire program on schedule jeopardy and puts immense pressure on the entire supply chain to perform to levels that maybe are unreasonable or difficult to come out looking good, when really you were just trying to do the right thing and build to print or reduce costs," he said. "Those are some challenges as well. I've seen many cases where jobs go on hold for three months, and then of course everyone needs it tomorrow. And I certainly understand that, no matter who that customer is. Everyone is making a product, and we’re all feeding upwards towards some goal, and you can’t recover that lost time. I’d say to Dave’s point, there are certainly business challenges with that. I think change management, where it changes, and their impact on the overall schedule is also a challenge that’s worth noting."
From an EMS standpoint, Zentech's Turpin also mentioned the need to comply with the new cybersecurity rules. "The NIST 800-171 guidelines are complex. It’s night and day. ITAR is really nothing compared to the cyber rules. Complying with ITAR would be maybe a three, and to comply with the NIST 800-171 is more like an 83. It’s orders of magnitude more complex and we’ve been working on it, and we already had a head start. We started about three years ago down this path, but the NIST 800-171 is formidable and it’s being driven at us as flowdowns from all the military primes. Fortunately, it doesn’t have to kick in now, but soon everybody is going to have to do it," he said. "To the earlier point about the military being more commercial in terms of pricing, this NIST 800-171 is going to be an unbelievable barrier to entry. I don’t know how a lot of people are going to have the infrastructure and the capability to comply with it. They’re either going to have to close their eyes when they self-certify, or they’re just going to be completely non-compliant and hope it will go away. NIST 800-171 is huge, and I'm surprised a lot of people aren’t talking about it yet. That will be a big challenge. We’re doing pretty good. We should be compliant before the end of this year."
Regarding how long it takes to go through that compliance process, Turpin said it depends on how mature the organization is. "For us, we currently have only two sites, and we’re getting ready to add a third. If you are a multi-site organization, or you’ve got the challenge that Scott does in terms of kind of a virtual organization, it’s unbelievably difficult because very specific hardware issues must be dealt with. I can’t even begin to talk about it. I mean, I’ve got a whole team that’s dealing just with this compliance."
But isn’t this industry over-regulated already? Absolutely not, according to Turpin. He said that there is such a disparity in terms of the due diligence the companies in the mil/aerospace undertake, and it's absolutely needed. "What a lot of companies do that I’ve seen, that we’ve audited, it’s almost criminal the lack of protections they have, relative to firewall, file security, data security, who they send files to, how they store stuff. It’s absolutely needed," he stressed.
To read the full version of this article, which appeared in the July 2017 issue of SMT Magazine, click here.
Testimonial
"In a year when every marketing dollar mattered, I chose to keep I-Connect007 in our 2025 plan. Their commitment to high-quality, insightful content aligns with Koh Young’s values and helps readers navigate a changing industry. "
Brent Fischthal - Koh YoungSuggested Items
Meet the Author Podcast: Martyn Gaudion Unpacks the Secrets of High-Speed PCB Design
07/16/2025 | I-Connect007In this special Meet the Author episode of the On the Line with… podcast, Nolan Johnson sits down with Martyn Gaudion, signal integrity expert, managing director of Polar Instruments, and three-time author in I-Connect007’s popular The Printed Circuit Designer’s Guide to... series.
Intervala Hosts Employee Car and Motorcycle Show, Benefit Nonprofits
08/27/2024 | IntervalaIntervala hosted an employee car and motorcycle show, aptly named the Vala-Cruise and it was a roaring success! Employees had the chance to show off their prized wheels, and it was incredible to see the variety and passion on display.
KIC Honored with IPC Recognition for 25 Years of Membership and Contributions to Electronics Manufacturing Industry
06/24/2024 | KICKIC, a renowned pioneer in thermal process and temperature measurement solutions for electronics manufacturing, is proud to announce that it has been recognized by IPC for 25 years of membership and significant contributions to electronics manufacturing.
Boeing Starliner Spacecraft Completes Successful Crewed Docking with International Space Station
06/07/2024 | BoeingNASA astronauts Barry "Butch" Wilmore and Sunita "Suni" Williams successfully docked Boeing's Starliner spacecraft to the International Space Station (ISS), about 26 hours after launching from Cape Canaveral Space Force Station.
KIC’s Miles Moreau to Present Profiling Basics and Best Practices at SMTA Wisconsin Chapter PCBA Profile Workshop
01/25/2024 | KICKIC, a renowned pioneer in thermal process and temperature measurement solutions for electronics manufacturing, announces that Miles Moreau, General Manager, will be a featured speaker at the SMTA Wisconsin Chapter In-Person PCBA Profile Workshop.