-
- News
- Books
Featured Books
- design007 Magazine
Latest Issues
Current IssueCreating the Ideal Data Package
Why is it so difficult to create the ideal data package? Many of these simple errors can be alleviated by paying attention to detail—and knowing what issues to look out for. So, this month, our experts weigh in on the best practices for creating the ideal design data package for your design.
Designing Through the Noise
Our experts discuss the constantly evolving world of RF design, including the many tradeoffs, material considerations, and design tips and techniques that designers and design engineers need to know to succeed in this high-frequency realm.
Learning to Speak ‘Fab’
Our expert contributors clear up many of the miscommunication problems between PCB designers and their fab and assembly stakeholders. As you will see, a little extra planning early in the design cycle can go a long way toward maintaining open lines of communication with the fab and assembly folks.
- Articles
- Columns
Search Console
- Links
- Media kit
||| MENU - design007 Magazine
Martyn Gaudion on Signal Integrity Modelling and Stackup Tools
December 11, 2018 | Pete Starkey, I-Connect007Estimated reading time: 9 minutes
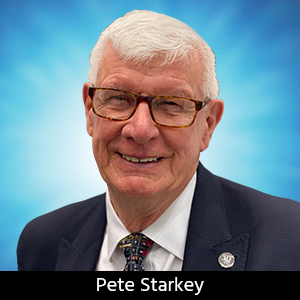
The accuracy of signal integrity modelling continues to improve, and stackup tools are becoming widely used, which now include material suppliers' datasheet information. During the recent electronica show in Munich, Germany, Martyn Gaudion, managing director at Polar Instruments, explained how Polar often serves as a bridge between PCB design and fabrication, and why educating his customers is so critical.
Pete Starkey: Martyn, it’s great to see you again. Another show! It’s extremely busy everywhere, and it would appear you've had a very successful first day at electronica 2018.
Martyn Gaudion: Yes, we're sitting here in front of a very thick pile of enquiry forms, which is fantastic for day one, so I hope it continues.
Starkey: I understand that there's a lot of interest in making sure that all of the PCB fabricators have access to all of the material suppliers' dielectric data that they need to put designs through their Speedstack software?
Gaudion: Yes, and this year, we've focused on our relationship with the material suppliers. We have some strong suppliers in the materials industry who provide us with quite rich levels of data with more than just electrical information. Some of our customers want to know about resin content or more broad material properties.
Some OEMs like to specify the materials, and about 70% of our customers are OEMs. Meanwhile, 30% of our customers are fabricators, and some of our fabrication customers run all of their jobs through Speedstack. So, it's not only the high-tech materials they need; some like to have their popular low-tech materials as well because they put everything through the same pre-planning route.
Starkey: It becomes a standard front-end process. Do you have a problem containing all of the data that people are asking you for?
Gaudion: It's always a challenge because you know what PCB base-material specs are like—there's so much information. There's a degree of cherry-picking; we pick the information that's most important for most people. When you look at the datasheets describing a base material—for example, look at the resin systems alone—and then when you start to look at copper foils and roughness, the type of surface finishes, etc., the potential quantity of data might be unmanageable.
We tend to work on the most popular materials and when there are specialist materials where an OEM says, "I want this particular family for this particular job." Then, we'll focus on that. It's very much demand-led from OEMs who are after specific materials in the library and fabricators who say, "These are the materials we like."
Starkey: In general, do you have to go to laminate manufacturers and ask for the information or do manufacturers come to you and say, "Please include the data on this, this, and this?"
Gaudion: It's about 50-50. Some base material suppliers are very cooperative. Others are a bit more reluctant, and we will ask the OEMs to pressure them to provide material information for us, so there's a mix.
Starkey: It's nice from your point of view to be that central resource—that pivot of communication about properties of materials.
Gaudion: Yes, it's something that we've always seen—Polar sits nicely between design and fabrication. We help our design and fabrication customers with the realities, matching both the expectations of what you can produce and trying to make sure that they understand what could be produced, so they get the best yield and nobody has missed expectations. If we can get people to understand what to expect, either way up or down the supply chain, that works well for us. We're well respected for that, and we try very hard to provide a service to our customers that lets them get the information they need.
Starkey: “Service” is a very appropriate and valuable word in this context.
Gaudion: Yes, and that is what we've found. Many of our customers are on active maintenance contracts, and we work hard to make sure they get looked after and have their questions answered.
Starkey: And the tools improve all the time.
Gaudion: Absolutely.
Starkey: It's all those little refinements and incremental improvements that you make. You've talked a lot about the effect of copper roughness, for example, in presentations I’ve attended recently.
Gaudion: And we're improving the copper roughness modelling. Some new enhancements are going in there next year. Even this year, we've made some significant steps forward, which is key. We’ve also been educating design customers that actually spec’ing a copper foil doesn't mean that the foil is going to be the same roughness in the finished product because the fabricator is going to apply treatment to it, so you need to speak to the fabricator about the roughness and not necessarily the foil supplier. Those kinds of things are pieces of intelligence that we can add into that communication, which isn't always obvious when you just look at a datasheet.
Starkey: It's good that you're able to educate designers about the real world.
Gaudion: Yes.
Starkey: With no disrespect to designers, in my experience, they live in a world of their own a lot of the time without a real appreciation for the realities of the materials that they're specifying.
Gaudion: Precisely, and even our own designers will say, "I'd like to read this datasheet because I don't want to ask anybody." Designers are sometimes quite private people, and we say, "Actually, some of that information you're not going to find out unless you pick up the phone and ask somebody." Often, we can at least say, "You need to consider this. Have you thought of that? And maybe you should ask because some of that information isn't always available from the datasheet."
Starkey: What percentage of designers make themselves aware of the facilities that are available for doing modelling? And to what extent do they just produce the design, perhaps with some awareness, and then leave the modelling to the fabricator?
Gaudion: I'm not sure, but it's increasing. The larger OEMs often have somebody positioned as a PCB technologist, maybe an ex-PCB fabrication specialist, who now works for an OEM. Those PCB technologists work with the design teams to make sure that their designs are realizable, so that's certainly essential. When we find an OEM that employs a PCB technologist, we know that they’re much more likely to understand what our tools do. We also see customers who come to us and say, "Well, we spec the PCB and get it different from the same fabricator, or we get it different from two different fabricators. Why should this happen?"
We can start to explain why if you don't spec the build correctly, it's quite reasonable that you can get the same PCB with the same number of layers built in a multitude of different ways. They may perform very differently even if they're made of the same base materials. That's quite a shock to designers a lot of times.
Starkey: I could have written a book on my experiences as a PCB fabricator. Again, trying to get the message over to the designer about, "Look, these are the realities." And that was before there was much awareness about interconnects being active components rather than just passive DC connections between A and B. It has become more and more relevant and understood. From the perspective of the material suppliers, they're now getting ahead of the game. Interface people like yourselves are also ahead of the game—you know what the industry is going to need even before the industry realizes what it needs.
Gaudion: What we've found is that the traditional markets for ourselves—like telecommunications, aerospace, and defense companies—are pretty well aware of what's happening. However, there's suddenly a whole spectrum of companies that are now using electronics—low, medium, and high speed—that weren't even in the game before.
These people are brand new. They come into it cold, and that's where our help is really useful. We can work with those people to help them understand, whether they source locally in Europe, are going out to Asia, or working through value-added brokers. High-end brokers are very useful in some areas where they can add that PCB knowledge to somebody new coming in to procuring PCBs. We see those people as well.
Starkey: The quality of modelling is improving all the time.
Gaudion: It is, yes.
Starkey: I've often heard your colleague Neil Chamberlain say, "All models are wrong, but some are useful." Today's models are not as wrong as they used to be!
Gaudion: Not as wrong as they were before, I agree. Once they get the model that good, then they think, "Oh, we can push it a little bit further." And then you expose some more things to fix, which always gives us more to provide for our customers, which is great.
Starkey: It's an iterative process; it will never be perfect, but it will get closer to being perfect. Martyn, is there anything else that we should talk about?
Gaudion: I think we've pushed the high-speed capability in our stackup tools; whereas gigahertz modelling was in a separate tool that you had to cut and paste from the stackup, we've now built in multi-gigahertz insertion loss modelling directly into the stackup tool. People now can document the stackup with insertion loss as well as impedance, so when they're pushing 20, 30, 40 gigahertz; that's possible with our tools.
The other thing we've done is that, with more and more people doing HDI and filling vias with different materials, whether they're sintering or plugging them with resins or different types of materials, for next year, we're expanding the number of different fills you can have in via holes. There are not just simple integrity things happening in our tools, but a broadening out of the capabilities. People are saying, " I know signal integrity is important, but there's more to a PCB than just the high-speed performance." The other embellishments in the tool, which help our general population of customers, are being worked on as well as the SI stuff. Drilling is an area we'll focus on for next year.
Starkey: Expand on that a little bit.
Gaudion: Well, people are plugging, tenting, or laser-drilling whether they want to fill the holes with sinter or plate them full. We can now document the different types of fills you can have in the drilled holes.
Starkey: So, the holes effectively become a sort of active component of the interconnect through which you understand the properties and take them into account in the modelling.
Gaudion: Yes, and to finish what you were saying in terms of the sentiment of the show, I just talked to Neil Chamberlain about the atmosphere of 10 years ago when the industry was at its lowest, and John Ling was saying, “Would the last person in the European electronics industry please close the door and turn the lights off.” And look at what's happened—it’s unbelievable.
Starkey: Yes, just look at the size of this show and the level of activity. And on the first day, you already have a stack of meaningful inquiries.
Gaudion: Yes, very meaningful inquiries.
Starkey: I hope your energy lasts for the rest of the week!
Gaudion: I hope so too! Thank you, Pete.
Starkey: Thank you, Martyn.
Visit I-007eBooks to download your copies of Polar Instruments’ books today written by Martyn Gaudion: The Printed Circuit Designer’s Guide to… Secrets of High-Speed PCBs, Parts 1 and 2.
Suggested Items
RF PCB Design Tips and Tricks
05/08/2025 | Cherie Litson, EPTAC MIT CID/CID+There are many great books, videos, and information online about designing PCBs for RF circuits. A few of my favorite RF sources are Hans Rosenberg, Stephen Chavez, and Rick Hartley, but there are many more. These PCB design engineers have a very good perspective on what it takes to take an RF design from schematic concept to PCB layout.
Trouble in Your Tank: Causes of Plating Voids, Pre-electroless Copper
05/09/2025 | Michael Carano -- Column: Trouble in Your TankIn the business of printed circuit fabrication, yield-reducing and costly defects can easily catch even the most seasoned engineers and production personnel off guard. In this month’s column, I’ll investigate copper plating voids with their genesis in the pre-plating process steps.
Elephantech: For a Greener Tomorrow
04/16/2025 | Marcy LaRont, PCB007 MagazineNobuhiko Okamoto is the global sales and marketing manager for Elephantech Inc., a Japanese startup with a vision to make electronics more sustainable. The company is developing a metal inkjet technology that can print directly on the substrate and then give it a copper thickness by plating. In this interview, he discusses this novel technology's environmental advantages, as well as its potential benefits for the PCB manufacturing and semiconductor packaging segments.
Trouble in Your Tank: Organic Addition Agents in Electrolytic Copper Plating
04/15/2025 | Michael Carano -- Column: Trouble in Your TankThere are numerous factors at play in the science of electroplating or, as most often called, electrolytic plating. One critical element is the use of organic addition agents and their role in copper plating. The function and use of these chemical compounds will be explored in more detail.
IDTechEx Highlights Recyclable Materials for PCBs
04/10/2025 | IDTechExConventional printed circuit board (PCB) manufacturing is wasteful, harmful to the environment and energy intensive. This can be mitigated by the implementation of new recyclable materials and technologies, which have the potential to revolutionize electronics manufacturing.