-
- News
- Books
Featured Books
- design007 Magazine
Latest Issues
Current IssueProper Floor Planning
Floor planning decisions can make or break performance, manufacturability, and timelines. This month’s contributors weigh in with their best practices for proper floor planning and specific strategies to get it right.
Showing Some Constraint
A strong design constraint strategy carefully balances a wide range of electrical and manufacturing trade-offs. This month, we explore the key requirements, common challenges, and best practices behind building an effective constraint strategy.
All About That Route
Most designers favor manual routing, but today's interactive autorouters may be changing designers' minds by allowing users more direct control. In this issue, our expert contributors discuss a variety of manual and autorouting strategies.
- Articles
- Columns
- Links
- Media kit
||| MENU - design007 Magazine
Estimated reading time: 4 minutes
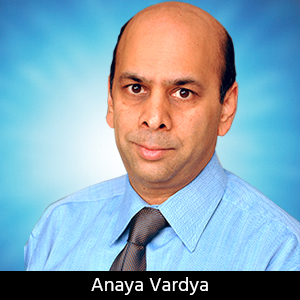
Standard of Excellence: Microwave PCB Bonding Methods—What Designers Need to Know
There are three methods commonly used for bonding multiple layers of RF and microwave PCB laminates such as PTFE (Teflon) materials like Rogers Duroid. These three methods are thermoplastic films, thermoset prepregs, and direct bonding (often called fusion bonding). Each has their own pros and cons that PCB designers need to understand to balance cost and performance.
Thermoplastic Film Bonding
Bonding films are designed to flow into the laminate stackup under heat and pressure to encapsulate the traces left on the surface of the inner layers after the etching process. This means that the bond is primarily mechanical in nature. Several thermoplastic bond films are available for use in PCB applications including polyethylene (PE), chlorotrifluoroethylene (CTFE), fluorinated ethylene propylene (FEP), and polytetrafluoroethylene (PTFE). Major suppliers of this material over the past 40 years include Rogers, Taconic, and Arlon. Thermoplastic bonding films are not well suited for use in hybrid multilayers due to the temperature required to melt these materials. The lower thermal degradation point of thermosetting materials may cause these materials to oxidize and decompose.
The transition (melting) temperature of these films must be considered to assure the right material match to the application. Polyethylene has the lowest melt temperature from approximately 190–250°F (88–121°C), depending on the density of the resin and degree of molecular cross-linking. CTFE is about 380°F (193°C), which is prohibitive for PCBs that will see manufacturing processes with higher temperatures such as hot air solder leveling (HASL). FEP has a transition point of 500°F (260°C) and is capable of handling HASL temperatures. PTFE has the highest transition temperature above 630°F (332°C), so it will survive subsequent high-temperature processes.
The primary advantage of using thermoplastic films is their low electrical loss factor. PTFE multilayer boards are well known for their excellent electrical properties, but using a hybrid construction of a high-loss epoxy-based prepreg would defeat the purpose of the PTFE. While a particular bonding film may not exactly match the dielectric constants of the laminate, the effect of any difference is typically negligible, or if not, the board can be designed to allow for the difference. The downside is that thermoplastic film bonding is typically limited to low layer PCBs and not suited for sequential lamination.
Thermoset Prepreg Bonding
Thermoset prepregs harden and cure as a result of a thermochemical reaction such as the reaction that hardens the two components of epoxy when mixed together that you can buy at the hardware store. Thermoset prepregs can also be reinforced with fillers to improve the stability of the final product. Once hardened or cured, thermoset materials are typically harder than their thermoplastic counterparts. Unlike thermoplastic materials, thermoset materials go through the thermochemical reaction only once, and cannot be re-melted like a thermo-plastic. Before the cure of thermoset prepregs, they have a limited shelf life compared to thermoplastic films.
The primary advantages of thermoset pre-pregs are the ability to manufacture sequentially laminated PCBs and produce higher layer count stackups, and a closer match to traditional laminate properties in hybrid constructions. The primary disadvantage is a high electrical loss factor.
Fusion Bonding
The first two methods require additional films or prepreg materials, which function like glue to keep the multiple layers in one piece. The third approach for forming RF and microwave PCBs, fusion bonding, uses heat and pressure to direct bond the material substrate layers into one piece. The layers are joined together through extremely high temperature and precisely controlled pressure without the addition of any bonding materials.
This method has its challenges such as the additional control over the lamination fixture, pressure, and elevated temperature. But the increased performance over thermoplastic and thermoset bonding are significant in the right application. The fusion bonding results yield a fully homogeneous dielectric constant structure with no mismatch of properties from different films or prepregs. Fusion bonding produces a single, uniform dielectric constant value throughout the PCB package, which can instrumental for high-frequency applications that must meet critical performance requirements.
Comparison of Pros and Cons
Thermoplastic Films
Pros
- Good to excellent loss characteristics
- Lower dielectric constant (Er) than most thermosetting prepregs (close to pure PTFE
- Pure isotropic material
Cons
- Not a good choice for sequential lamination
- Lamination temperature unsuitable for many thermosetting prepregs
- Poor drilling performance with potential for smearing
- Cannot be desmeared or etched back
Thermosetting Prepregs
Pros
- Possible to match resin system and electrical properties of thermosetting laminates with an Er of 2.95 and above
- Superior CTE to thermoplastic bond films
- Can be desmeared and typically etched back
Cons
- Anisotropic material
- Not available with an Er ≤ 2.94
- Traditionally higher loss than thermoplastic resin systems
Fusion Bonding
Pros
- Best electrical performance
- Er is almost perfectly matched to adjacent laminate materials
- May be sequentially laminated depending on copper thickness
Cons
- Not typically suited for bonding plated subassemblies unless PTFE bond-ply is used
- Long lamination cycle
- Extremely high lamination temperature required ≥700°F (371°C)
- Not compatible with thermosetting resin systems
Conclusion
As you can see, each of the discussed microwave bonding methods has distinct advantages and disadvantages that must be considered when choosing which method will be the right one for a specific application. PCB designers need to fully understand these characteristics to balance cost and performance when selecting the optimum bonding method.
More Columns from Standard of Excellence
Standard of Excellence: The Human Touch in an Automated WorldStandard of Excellence: Training Your Team to Excel in Customer Service
Standard of Excellence: Delivering Excellence—A Daily Goal
Standard of Excellence: The Role of Technology in Enhancing the Customer Experience
Standard of Excellence: Turning Negative Customer Feedback Into Positive Outcomes
Standard of Excellence: Anticipating Customer Needs Early and Often
Standard of Excellence: The Power of Personalization in Customer Care
Standard of Excellence: Building Trust with Customers—The Foundation of Excellent Service