Estimated reading time: 5 minutes
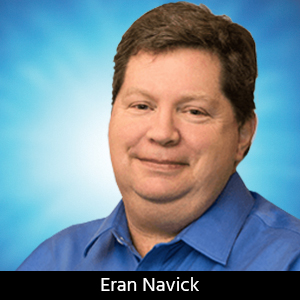
Global Technology: Assembling High-current, Heavy Copper PCBs
Many designers and assemblers are not familiar with what is readily available in high-current, heavy copper PCBs. Heavy copper boards can have 3–20 oz. of copper. There are many variations of the heavy copper technology, with buried heavy copper, multiple levels of copper, and multilayer heavy copper. The simplest form of heavy copper is a single- or double-sided PCB with 3–20 oz. thickness of copper as traces.
For single-sided boards, by starting with a heavy copper base, such as 8 oz. on FR-4, and imaging and etching the image on, single-sided PCBs have the lowest cost but suffer from very poor line resolution of a 3-mil line width per oz. of copper on the surface. On double-sided boards, the designer has the choice of the starting copper thickness and amount plated in the holes. The current required to passed through the vias will determine the amount of copper required to be plated in the hole.
For example, to plate 6 oz. of copper in the holes of an 8-oz. PCB, the manufacturer will start with 2 oz. of copper and plate up to 6 oz. in the holes and on the traces. To plate that thick, multiple layers of dry film will be sequentially layered on 3–4 times, imaged, and developed, creating very deep traces to copper plate up. The plating of 6 oz. of copper is quite slow, taking 45 minutes per oz., so the PCB will be expensive by taking up costly copper plating time. The line resolution can be as fine as 1 mil per oz., and the heavy plated vias can carry hundreds of amps and are virtually indestructible.
Multilayer heavy copper can have 4–20 layers of up to 10 oz. of copper per layer and interconnected with heavy or normal copper in the vias. In both multilayer and double-sided PCBs, the use of large thermal reliefs is of utmost importance for assembly. The heavy copper conducts so much heat you would never solder the components properly using normal methods. By designing extra vias in the large pads associated with wide thick tracks, you allow it to pass more current and keep the pad attached as well as providing a stronger pad for the bolt holding the cable in place.
Assembling a heavy copper PCB over 4 oz. can be difficult, but not impossible. Extra care and engineering when designing the board must be observed to allow the thermal transfer of the heat from a soldering iron to the pads. The use of track neck downs—as well as large, open thermal reliefs—help the soldering method deliver the heat needed. It is not recommended to use IR heat or wave solder on a heavy copper board over 4 oz. The heat picked up by the thick heavy copper will be retained for such a long time that the FR-4 joint will fail, and the copper traces will lift off the board due to the melting of the epoxy laminate.
The soldering of heavy copper PCB can present problems if your assembly company is not experienced in trying to get enough heat into the board to solder the components. Many heavy copper PCBs over 6 oz. need to be hand soldered on a hot plate just to get a high enough temperature to solder properly. The very thick copper traces can make heating the via pad to a high enough temperature quickly very difficult without losing adhesion to the FR-4 and lifting the pad.
Most experienced heavy copper designers will add extra vias around the pads to rivet the pad to the FR-4 board, and then branch out with thermal relief to the heavy copper traces. It is recommended the PCB manufacturer use high-temperature, lead-free rated laminate to assist keeping the pads attached with all the retained heat in the high thermal mass of the copper from proper soldering. Problems encountered in assembling heavy copper PCBs are mostly based on cold solder joints without full flow through to the other side of the via.
To assist in obtaining the correct heat for soldering, typically, a hot plate is used to preheat the heavy copper PCB to just below the Tg temperature of the laminate, the additional heat then allows the soldering iron to properly melt the solder. Many assemblers use special 200–300-watt soldering irons to quickly get the heat needed in, properly melt the solder, and then get off the pads, so the area cools back down below the Tg.
Assembly methods for the heavy copper PCB need to be tested and figured out before you can properly solder the heat-conducting heavy copper boards. The thickness of copper varies 4–20 oz. of copper on the surface, in the multilayers, and possibly some thick copper in the through vias. The heavy copper PCB can be on almost any type of laminate from flex to FR-4 through polyimide, further complicating the assembly soldering process.
When trying to solder 10 oz. of copper, it can be a big surprise when you place a typical solder iron on a big pad to solder it, and the solder won’t melt. A few large, adjustable, lab-style hot plates work well to preheat the heavy copper PCB. Monitor the PCB temperature with an accurate thermocouple or IR meter, and after you have soldered the board, let it cool slowly when it is flat to not delaminate or warp the board.
Designers can assist the assembly of heavy copper PCBs by adding heat-reducing pads called thermal reliefs, which look like wagon wheels. The few spokes from the via out to the heavy copper trace reduce the heat transmitted to the thick copper planes or traces, allowing the pad to heat up quicker. Properly designed thermal relief pads allow for significantly easier soldering. When calculating the number and width of the spokes, calculate the current in the via and adjust the line width to twice that required to ensure proper current flow without overheating.
In the end, the most important thing for designers, fabricators, and assemblers is to talk and create a synergistic relationship aimed at producing the best products available on the market today.
Eran Navick is CEO of FineLine USA.
More Columns from Global Technology
Global Technology: The Importance of Fine LinesGlobal Technology: The Importance of Laminate CTE in PCB Design