Estimated reading time: 2 minutes
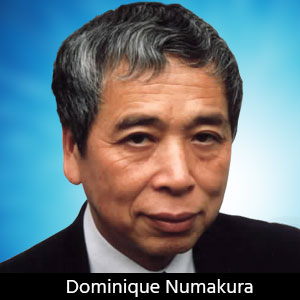
EPTE Newsletter: Next-Generation Flex Circuits–Transparent
DuPont, one of the largest chemical companies in the world, developed a super engineering plastic film during the 1960s and soon after introduced Kapton, a polyimide film that remains stable across a wide range of temperatures.
DuPont also developed basic constructions of flex circuits as the major application of Kapton films. Nowadays, the flex circuit market reels in $20 billion a year. It is the primary wiring material for smartphones and smartwatches. If you remove the back cover of a mobile device, you will discover films that are orange in color. The industry term for this is “Kapton color.” The color and low transparency of Kapton was never an issue for suppliers and contract manufacturers, so circuit designers did not require any particular color for heat-resistant films. It was Apple that decided it didn’t like the Kapton color and required flex circuit manufacturers to paint the polyimide films black.
Circuit designers never questioned the color of Kapton either (fortunately for polyimide film manufacturers). Clear films were required for some flexible circuits in display devices or photovoltaic cells; however, polyethylene terephthalate (PET) films were used instead. Low-temperature packaging processes were developed for non-heat-resistant materials.
The ever-changing electronics market requires upgrades to components, films, and circuits. New photo modules and medical equipment now demand both transparency and heat resistance for high-temperature processing, such as soldering and wire bonding. Material suppliers found a way to satisfy these new requirements, but it was not easy to have both transparency and heat resistance without a trade-off. Some material suppliers were successful in creating clear polyimide films that have transparencies greater than 85% and stable mechanical properties with temperatures over 300°C. One polyethylethylketone (PEEK) film manufacturer successfully created a heat-resistant and transparent film, and a few fluorocarbon resin manufacturers successfully developed heat-resistant and transparent films.
The next hurdle is to build copper-clad laminates with transparent and heat-resistant films. A couple of laminate manufacturers—including DKN Research—already developed a universal metalizing and copper plating process to produce copper-clad laminates. The bond strength is proven, and these laminates are ready for the standard etching processes.
The coverlay is currently under development. Laminate manufacturers are not prepared to ship reliable coverlay films with transparent glue. Chemical companies are close to delivering transparent and heat-resistant ink (actually transparent polyimide ink) as a screen-printable transparent coverlay.
There is one last detail to overcome before we complete transparent and heat resistant flex circuits—transparent conductors. We are considering several candidates. ITO film is still useful because of its long history. Low performance with flex endurance is the major issue of the flex circuits. A relatively high conductor resistance stands in the way of application expansion. Organic conductive ink could be an option, but relatively low conductivity is still a problem. A lower heat resistance restricts applications. A screen-printable silver nano-wire ink could be used, but its relatively high cost eliminates it as an option. Fine copper mesh generated by chemical etching has a very different concept as a transparent conductor. It has almost the same conductivity as copper foils but requires a very high etching capability for the fine-line mesh and is cost-prohibitive.
The perfect solution is within reach. Once it comes to fruition, there will be high demand for transparent flex circuits.
This column originally appeared in the July issue of Design007 Magazine in the FLEX007 section.
Related column from the FLEX007 section of the December 2019 issue of Design007 Magazine: EPTE Newsletter: Transparent Flexible Circuits
More Columns from EPTE Newsletter
EPTE Newsletter: Travel to Japan During COVIDEPTE Newsletter: A New COVID Surge in Taiwan?
EPTE Newsletter: COVID-19 PCR Test in Japan
EPTE Newsletter: Japan Failing in Vaccine Distribution
EPTE Newsletter: A Long Trip to the U.S.
EPTE Newsletter: Ten Years After Fukushima
EPTE Newsletter: Taiwan Releases 2020 PCB Production Numbers
EPTE Newsletter: The Printed Circuit Industry in China