-
- News
- Books
Featured Books
- design007 Magazine
Latest Issues
Current IssueShowing Some Constraint
A strong design constraint strategy carefully balances a wide range of electrical and manufacturing trade-offs. This month, we explore the key requirements, common challenges, and best practices behind building an effective constraint strategy.
All About That Route
Most designers favor manual routing, but today's interactive autorouters may be changing designers' minds by allowing users more direct control. In this issue, our expert contributors discuss a variety of manual and autorouting strategies.
Creating the Ideal Data Package
Why is it so difficult to create the ideal data package? Many of these simple errors can be alleviated by paying attention to detail—and knowing what issues to look out for. So, this month, our experts weigh in on the best practices for creating the ideal design data package for your design.
- Articles
- Columns
- Links
- Media kit
||| MENU - design007 Magazine
Designing PCBs With Additive Traces
April 28, 2022 | Tomas Chester, Chester Electronic DesignEstimated reading time: 2 minutes
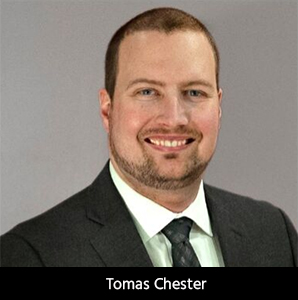
Advances in technology have been clear to see within the component packaging industry, as the ball grid array (BGA) package sizes reduce from 1.0 mm pitch to 0.8 mm, 0.4 mm, and even beyond. However, while these improvements have occurred with component packages, it has become increasingly more difficult to break out and route the dense circuitry associated with these parts. Currently, the high-density interconnect (HDI) method typically used for the breakout of such parts has been to create the smallest possible subtractive-etched traces with microvias to allow for connections and escapes on the innerlayers of your PCB.
Now there are new fabrication processes that change how we can approach some of these layout difficulties. Additive and semi-additive construction now allows us to get down below 0.075 mm trace and gap sizes easily and reliably, however, utilizing it brings its own series of challenges to the table. Before designers and engineers can start to use this technology, we need to understand the difference between the standard subtractive fabrication method and these new additive fabrication methods, as well as their respective design requirements for trace impedance, and the signal integrity impact from routing traces closer together.
Subtractive vs. Additive
Let's start by taking a brief high-level view of the different fabrication processes. With subtractive fabrication, our PCBs start with a base layer of copper of some thickness already laminated to the substrate. Then copper is electrolessly plated onto the board’s outer layers, including inside the drill and via holes. A design image is then applied, an etch resist plated onto the exposed traces and holes, after which etching will occur. This is our subtractive step, where we remove the copper in areas where there was no image applied. This is also the limiting step in the subtractive fabrication process, because as we etch vertically down through the copper, the etching agents also remove copper in a horizontal direction, under the applied design image. The result of this process is a final copper trace cross-section with a trapezoidal shape. The critical concern here is that if the trace height is half as tall as its width, likely the etching process will remove the trace.
With additive fabrication, the process can be imagined as similar to 3D printing. The PCB starts with no copper on the laminate material and is instead “built” up on top of a thin seed layer of electroless copper, or on top of a thin laminated copper foil. This not only allows for trace and gap sizes down to 0.010 mm; it also creates a trace cross-section that has a rectangular shape.
To read this entire article, which appeared in the April 2022 issue of Design007 Magazine, click here.
Suggested Items
I-Connect007 Editor’s Choice: Five Must-Reads for the Week
07/18/2025 | Nolan Johnson, I-Connect007It may be the middle of the summer, but the news doesn’t quit, and there’s plenty to talk about this week, whether you’re talking technical or on a global scale. When I have to choose six items instead of my regular five, you know it’s good. I start by highlighting my interview with Martyn Gaudion on his latest book, share some concerning tariff news, follow that up with some promising (and not-so-promising) investments, and feature a paper from last January’s inaugural Pan-European Design Conference.
Elephantech Launches World’s Smallest-Class Copper Nanofiller
07/17/2025 | ElephantechJapanese deep-tech startup Elephantech has launched its cutting-edge 15 nm class copper nanofiller – the smallest class available globally. This breakthrough makes Elephantech one of the first companies in the world to provide such advanced material for commercial use.
Copper Price Surge Raises Alarms for Electronics
07/15/2025 | Global Electronics Association Advocacy and Government Relations TeamThe copper market is experiencing major turbulence in the wake of U.S. President Donald Trump’s announcement of a 50% tariff on imported copper effective Aug. 1. Recent news reports, including from the New York Times, sent U.S. copper futures soaring to record highs, climbing nearly 13% in a single day as manufacturers braced for supply shocks and surging costs.
I-Connect007 Editor’s Choice: Five Must-Reads for the Week
07/11/2025 | Andy Shaughnessy, Design007 MagazineThis week, we have quite a variety of news items and articles for you. News continues to stream out of Washington, D.C., with tariffs rearing their controversial head again. Because these tariffs are targeted at overseas copper manufacturers, this news has a direct effect on our industry.I-Connect007 Editor’s Choice: Five Must-Reads for the Week
Digital Twin Concept in Copper Electroplating Process Performance
07/11/2025 | Aga Franczak, Robrecht Belis, Elsyca N.V.PCB manufacturing involves transforming a design into a physical board while meeting specific requirements. Understanding these design specifications is crucial, as they directly impact the PCB's fabrication process, performance, and yield rate. One key design specification is copper thieving—the addition of “dummy” pads across the surface that are plated along with the features designed on the outer layers. The purpose of the process is to provide a uniform distribution of copper across the outer layers to make the plating current density and plating in the holes more uniform.