-
-
News
News Highlights
- Books
Featured Books
- design007 Magazine
Latest Issues
Current IssueCreating the Ideal Data Package
Why is it so difficult to create the ideal data package? Many of these simple errors can be alleviated by paying attention to detail—and knowing what issues to look out for. So, this month, our experts weigh in on the best practices for creating the ideal design data package for your design.
Designing Through the Noise
Our experts discuss the constantly evolving world of RF design, including the many tradeoffs, material considerations, and design tips and techniques that designers and design engineers need to know to succeed in this high-frequency realm.
Learning to Speak ‘Fab’
Our expert contributors clear up many of the miscommunication problems between PCB designers and their fab and assembly stakeholders. As you will see, a little extra planning early in the design cycle can go a long way toward maintaining open lines of communication with the fab and assembly folks.
- Articles
- Columns
Search Console
- Links
- Media kit
||| MENU - design007 Magazine
Estimated reading time: 5 minutes
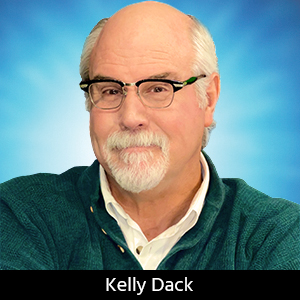
Contact Columnist Form
Target Condition: The Tale of Five CAD Monkeys
“But that’s the way we’ve always done it.”
Many electronics engineering groups have a hierarchical structure, with senior-, mid-, and junior-level engineering personnel possessing various depths of subject matter expertise. The head of an engineering group is usually one who has risen through the ranks of the organization and has fought and won many project battles; they’ve survived and can pass on knowledge, wisdom, and guidance.
Every so often, though, an engineering group leader must call together their team, and tell an ancient story passed down from the “elders” to steer the group in the right direction.
I recall a gathering like this: Several PCB project stakeholders could not agree upon a way to move forward with a challenging PCB assembly which had suffered failures on the SMT line. Small, newly-specified chip capacitors were “tombstoning” and “skewing” on the PCB, and the root cause could have been attributed to many different variables.
The conference meeting room was packed, and the VP of engineering wisely started the meeting by giving each one an opportunity to share their experience regarding the assembly defects.
One by one, they methodically went around the room. The first one spoke up, “We’re using all our standard equipment, materials, and processes the same way our people always have; our manufacturing constraints have not changed for many moons.” Then he looked to the customer’s PCB design stakeholder, who pronounced: “Our DRC rules have remained set to the defaults of our people since the beginning of time.” This continued around the table as they pointed to charts and data to show how their workflows were never altered in ways that would cause component defects such as these.
After the stakeholder feedback was given—and just before they had a chance to begin pointing fingers at each other—the VP of engineering began to talk about a profound parable.
“Sit down and I’ll tell you about the ‘Five Monkeys Experiment,’” he said, and began weaving a version of the story specially adapted for his group. It went something like this:
Long, long ago (in the ’90s), five “CAD monkeys” were placed in a cage as part of an experiment. In the cage were a bunch of bananas hanging by a string from the ceiling, as well as a spring-loaded test bed and a ladder, which needed to be precisely repositioned under the bananas to reach them.
The CAD monkeys had no use for the test bed at first. They knew intuitively that the ladder was the key to reaching the bananas. But each time a CAD monkey reset the ladder to climb toward the bananas, a crazy PCB cleaning process engineer sprayed all the CAD monkeys with icy de-ionized water. The CAD monkeys quickly formed some tribal knowledge about being sprayed down by the icy de-ionized water whenever attempting to reset the ladder. From then on, they agreed to inflict severe beatings on any who would dare go near the ladder.
Following their new tribal agreement, not a single CAD monkey went near the ladder. Instead, they spent all their time trying to figure out other creative ways to reach the bananas. Spontaneously, all five CAD monkeys tried reaching the bananas by bouncing higher and higher on the test bed. But you know what happens when five CAD monkeys jumped on a bed? Yep, one fell off and broke his head—a program manager then came along and substituted the injured CAD monkey in the cage with a new CAD monkey.
Intuitively, the first thing the new CAD monkey did was try to use the ladder to reach the bananas. After a training session involving several tail lashings from the already schooled CAD monkeys, the new CAD monkey learned the social norm. He was never taught “why” the other CAD monkeys wouldn’t let him use the ladder to reach the bananas because he had never been sprayed with icy de-ionized water. Nevertheless, he quickly learned that this behavior would not be tolerated by the other CAD monkeys. They continued trying to reach the banana without using the ladder. They even tried making a CAD monkey pyramid, but again, another monkey was injured.
One by one, each CAD monkey in the cage was injured trying to find a workaround for fear of using the ladder. Each time, the injured CAD monkey would be replaced by a new CAD monkey, who intuitively tried to climb the ladder, only to get beaten up. This happened a few more times until none of the original group remained.
By the end of the experiment, all five CAD monkeys in the cage had learned to never touch the ladder, though none knew the source of this strange reasoning. None of the remaining CAD monkeys knew about the icy de-ionized water abuse—the true root cause of their behavior modification (or tribal knowledge) in the first place. If they had, would they have called HR and recommended that the abusive test engineer be terminated? Once HR created a less toxic, experimental workplace, would the CAD monkeys have freely moved the ladder and reached the bananas?
If we could have asked the CAD monkeys for their rationale behind not letting their cage mates reset the ladder to reach the bananas, their answer might have been, “I was just following orders.” In other words, “That’s the way we’ve always done it.”
The Moral of the Story
Whether you consider yourself a PCB engineering stakeholder, PCB designer, or even a CAD monkey, let us avoid assuming or creating unfounded conspiracy theories for workflow items in your company which may seem backward. Let’s get to the root cause of stakeholder’s problems and challenges. Let’s communicate and find ways to climb the ladder with the understanding to reach the goals. If icy water is about to be dumped on you, refuse to be subjected to it. Bust out of the cage and head for HR.
Our engineering managers must see that holding on to the old ways can be a two-edged sword. Values and character traits—both good and bad—exist in the past. A group can be easily wiped out by the competition unless it cultivates a culture which fosters continual exploration and experimentation with new processes, materials, and machinery.
This column originally appeared in the March 2023 issue of Design007 Magazine.
More Columns from Target Condition
Target Condition: Designing vs. InventingTarget Condition: ‘Boomer to Zoomer: Do You Copy?’
Target Condition: Advanced Packaging Technologies—Look Before You Leap
Target Condition: My Anti-venom to PCB Cost Adders
Target Condition: Taking the Stand at Your Own Design Review
Target Condition: Designing Unconventional Geometries
Target Condition: What the Heck? A PCB Tech Spec Check
Target Condition: Keeping Your Design on the Road