-
- News
- Books
Featured Books
- design007 Magazine
Latest Issues
Current IssueCreating the Ideal Data Package
Why is it so difficult to create the ideal data package? Many of these simple errors can be alleviated by paying attention to detail—and knowing what issues to look out for. So, this month, our experts weigh in on the best practices for creating the ideal design data package for your design.
Designing Through the Noise
Our experts discuss the constantly evolving world of RF design, including the many tradeoffs, material considerations, and design tips and techniques that designers and design engineers need to know to succeed in this high-frequency realm.
Learning to Speak ‘Fab’
Our expert contributors clear up many of the miscommunication problems between PCB designers and their fab and assembly stakeholders. As you will see, a little extra planning early in the design cycle can go a long way toward maintaining open lines of communication with the fab and assembly folks.
- Articles
- Columns
Search Console
- Links
- Media kit
||| MENU - design007 Magazine
Slash Sheets and Material Selection
June 1, 2023 | I-Connect007 Editorial TeamEstimated reading time: 2 minutes
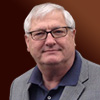
In a recent I-Connect007 survey to PCB designers, about one third of respondents said they consult IPC’s so-called slash sheets, such as IPC-4101/126, that contain a variety of information about PCB materials. But many designers say these specs don’t contain enough information. Some ask their fabricator to pick a material, and still others say, “It’s an RF board, and I always use supplier X for RF.” What’s the best process for selecting your PCB materials?
Doug Sober helped pioneer the development of IPC’s first slash sheets in 1996 for IPC-4101 Specification for Base Materials for Rigid and Multilayer Printed Boards and we asked him to discuss slash sheets—what they are, what they are not, and why PCB designers might benefit from an IPC materials guide developed specifically for designers.
Andy Shaughnessy: Doug, let’s start with your work with IPC and slash sheet development.
Doug Sober: I started in the laminate and prepreg business in 1978 for General Electric and was sent to my first IPC meeting in 1980. I got heavily involved right away with the task groups regarding specifications for laminates, prepregs, copper foils, glass fabric, resin coated foil, etc. The first standard we did was IPC-4101, but it did not just come out of thin air. We had a document from the military called MIL-S-13949H that had requirements for base materials. The requirements were physical such as flex strength and peel strength, electrical such as Dk and Df, thermal such as Tg and solder float, and environmental such as moisture absorption and fungus resistance. After IPC-4101 was all finished, it had specification sheets for simple FR-4s and polyimide base materials of various types.
The military had these specification sheets which described specific base materials and, as laminate and prepreg producers, we had to qualify our products to the requirements of the sheets. With specification sheet 21, for example, a bevy of lab tests proved that we met the requirements. Then the Defense Electronics Supply Center (DESC) would list our product by commercial name on their qualified product list (QPL). For example, Westinghouse’s FR-4 product 65M38 as listed on the QPL for specification sheet 21. Once a year, Lowell Sherman or Dave Corbett from DESC came to audit each base material supplier. When the 3-11 subcommittee created IPC-4101, we duplicated MIL-S-13949 because we wanted the military to sign off on it, discontinue their document, and use IPC-4101 in its place. In 1996, with the help of Dave Bergman negotiating with the military higher-ups, IPC-4101 was launched and Mil-S-13949 was discontinued.
To read this entire conversation, which appeared in the May 2023 issue of Design007 Magazine, click here.
Suggested Items
BEST Inc. Introduces StikNPeel Rework Stencil for Fast, Simple and Reliable Solder Paste Printing
06/02/2025 | BEST Inc.BEST Inc., a leader in electronic component rework services, training, and products is pleased to introduce StikNPeel™ rework stencils. This innovative product is designed for printing solder paste for placement of gull wing devices such as quad flat packs (QFPs) or bottom terminated components.
See TopLine’s Next Gen Braided Solder Column Technology at SPACE TECH EXPO 2025
05/28/2025 | TopLineAerospace and Defense applications in demanding environments have a solution now in TopLine’s Braided Solder Columns, which can withstand the rigors of deep space cold and cryogenic environments.
INEMI Interim Report: Interconnection Modeling and Simulation Results for Low-Temp Materials in First-Level Interconnect
05/30/2025 | iNEMIOne of the greatest challenges of integrating different types of silicon, memory, and other extended processing units (XPUs) in a single package is in attaching these various types of chips in a reliable way.
E-tronix Announces Upcoming Webinar with ELMOTEC: Optimizing Soldering Quality and Efficiency with Robotic Automation
05/30/2025 | E-tronixE-tronix, a Stromberg Company, is excited to host an informative webinar presented by Raphael Luchs, CEO of ELMOTEC, titled "Optimize Soldering Quality and Efficiency with Robotic Automation," taking place on Wednesday, June 4, 2025 at 12:00 PM CDT.
CE3S Launches EcoClaim Solutions to Simplify Recycling and Promote Sustainable Manufacturing
05/29/2025 | CE3SCumberland Electronics Strategic Supply Solutions (CE3S), your strategic sourcing, professional solutions and distribution partner, is proud to announce the official launch of EcoClaim™ Solutions, a comprehensive recycling program designed to make responsible disposal of materials easier, more efficient, and more accessible for manufacturers.